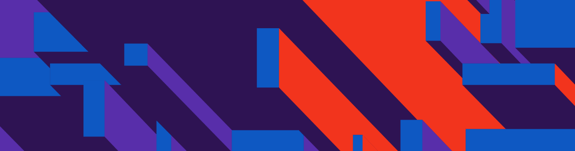
Behind The Built Environment
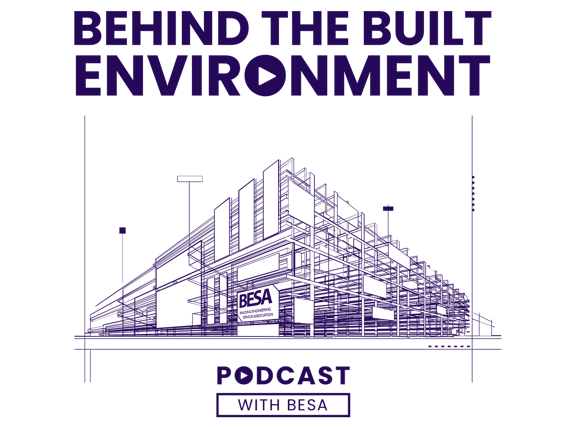
Behind The Built Environment, a podcast from BESA where we delve into the latest industry news in the building engineering services sector. Join us for insightful discussions and exclusive interviews with leading industry experts, as we explore the trends and innovations shaping the future of the built environment and what impact they will have on you and your business.
World Refrigeration Day Special - BTBE Extra Podcast Bonus Episode
Dr Marques shares insights from her 15+ years of experience across food service cooling, Net Zero innovation, and integrated energy systems.
The conversation emphasises the urgent need to prioritise sustainable refrigeration in the built environment and recognise the sector’s vital contribution to achieving Net Zero targets.
Behind Grenfell Tower - BTBE Extra Podcast Bonus Episode
On Friday 20 June, Netflix released Grenfell: Uncovered on Netflix — a powerful and painful reminder of the human cost of systemic failure.
To mark this moment, we’ve released a bonus episode of the Behind the Built Environment Podcast Extra, featuring Pete Apps, one of the UK’s most respected investigative journalists and author of the Orwell Prize-winning book Show Me the Bodies: How We Let Grenfell Happen, and keynote speaker at last year’s BESA Annual Conference.
Pete sat down with David Frise for a frank, sometimes uncomfortable, always necessary conversation about the Grenfell Inquiry, its impact on the construction industry, and what still urgently needs to change.
Episode 11: Behind the CCPI
In this episode of Behind the Built Environment, BESA Chief Executive David Frise speaks with Amanda Long, Chief Executive of Construction Product Information Ltd (CPI), about the critical role of accurate, transparent construction product data.
Amanda discusses the Code for Construction Product Information (CCPI), a post-Grenfell initiative designed to drive cultural and behavioural change in the way manufacturers provide information. Drawing on her background in ethical business and consumer protection, Amanda highlights the importance of leadership, accountability, and continuous improvement—especially in an industry long reliant on checklists over responsibility.
[00:00:00] David: Hello, I'm David Frise, Chief Executive of Beezer, and welcome to Behind the Built Environment, the podcast where I delve into the major issues facing our industry through in-depth conversations with key industry leaders. Join us as we explore the trends, challenges and innovations shaping the future of the built environment. And today we welcome Amanda Long. Welcome, Amanda. She's Chief Executive of Construction Products Information Limited, the not-for-profit organisation set up to guard, manage and assess conformance of the Code for Construction Product Information CCPI. That's quite a mouthful, I've got to say, Amanda. It doesn't roll off the tongue. Amanda has a wealth of experience driving ethical business practice and championing consumer protection, including the Considerate Constructor Scheme, Building a Safer Future and now leading the Code for Construction Product Information. We like to kick off with five simple yes-no answers. Now, I know we discussed this in, shall we say, the green room beforehand, you said you'd struggle with this, but yes-no, please. Have product manufacturers changed the way they provide information since the Grenfell disaster? No. Have manufacturers been properly held to account for misleading information provided in the past?
[00:01:26] Amanda: I think that one's a question for the police and the justice, not for me, David.
[00:01:30] David: Will the Building Safety Act transform the construction industry?
Amanda: Not on its own.
David: Yeah, OK. Will there always be bad actors who put building occupants at risk?
Amanda: Yes.
David: Is progress towards a better standard of product information moving fast enough?
Amanda: No.
Right. You did better than I thought you might do.
[00:01:48] Amanda: I'd love to put caveats against all of those comments, but that's for later.
[00:01:54] David: We'll come on to that later. Can you tell us a bit about yourself and how it all began for you and how did you end up working within the construction sector?
[00:02:04] Amanda: My career has gone across a number of different sectors and the golden thread, I think, that sits throughout my career is driving ethical business and transformational change and I've done that in different sectors in relation to being part of creating the first or one of the first eco-labels for consumers around sustainable fisheries and knowing where you're buying your fisheries from. So certification, traceability, we're all sort of part of that, as well as product information. Directly before I moved into the construction sector, I was six years as director general of a global charity representing 200 consumer organisations from across 120 countries as the statutory consultee at the United Nations, the OECD, the World Trade Organisation, all of those other places where there's sort of international discussion about that affects government policy in countries and consumer protection was sort of the piece that I was championing there. So six years of that and working very internationally, I decided I wanted to bring that skill set back home and do something back home. At that time, the Considerate Constructor Scheme were advertising for a chief executive and I was really interested in it because it was one of those sort of ubiquitous brands that I had seen. But what I wanted to know is, if you look under the bonnet, does it actually do the job that it should do for consumers and the public? So I applied for that role and spent the next three years transforming considerate constructors and really sort of looking at how we make sure it is delivering for the public. And within that, I also found myself looking at the whole industry debate that was going on following the Grenfell Tower fire and its response to Dame Judith Hackett's Building Safer Future review. And I volunteered my time on developing a couple of initiatives which were really about culture change because actually most of my career in transformational change and ethical business has all been about culture change. So it's all about trying to get industries to move to a different mindset in terms of their behaviours. And so I volunteered my time, set up the Building Safer Future charter and then was invited to set up the independent not-for-profit body that is the Code for Construction Product Information and that one really grabbed my attention.
[00:04:34] David: When you came into the industry from outside, were you surprised by what you saw in construction?
[00:04:39] Amanda: Yes, yes I was, yes. It's such an interesting kind of diverging tale that exists in construction in my view. On the one hand, you've got people of problem solvers, dynamic problem solvers, people who want to get things done, who really do sort of throw themselves at their work and believe in their industry and what they're delivering. But on the other hand, I found myself worried about, really worried about, how the industry was actually responding to the challenges that had been brought following the Grenfell tragedy and just not seeing the change that they needed to be making. So I really wanted to be part of that story which is why I got involved with setting up these organisations.
[00:05:23] David: And so your leadership of the CCPI comes at sort of a critical time for the industry. What motivated you to take that role and what's been your primary focus since becoming the CEO?
[00:05:38] Amanda: So it dovetails really well with a lot of the sort of work I've done in the past, just looking at product information and product safety, whether that was when I was working in consumer protection or even back in the earlier days when I was creating eco-labels. What really motivated me is the product information element of this discussion is one of the sort of key points in the whole discussion. You only need to read the report that came out from the inquiry on September the 4th last year to be horrified by some of the behaviours that manufacturers displayed and been found wanting through that report. But Dame Judith Hackett talked about that in her Building Safer Future review when that was published. And Paul Murrell and Annalise Day also talked about issues with product information in their report. So it's been a really consistent area of major concern coming out of the learnings from the Grenfell tragedy. It's an area that's got to be addressed and it's absolutely critical because how can you get the right product in the right place, which is fundamental to building safer buildings, if you can't have greater confidence in the product information that's being provided? It doesn't seem possible to me. So it's one of the key elements.
[00:07:07] David: So the CCPI sets out to ensure sort of clear, accurate and unambiguous construction product information. How has adoption been so far and what are the challenges do you think that remain?
[00:07:19] Amanda: So David, to be more precise, what CCPI does is setting out to move the industry to a place where product information is clear, accurate, accessible, up-to-date and unambiguous. It isn't a simple tick list that if you just check that these boxes are ticked, we can rely on the product information. But the industry loves a tick list. It's predicated on tick lists. Yes, and so that is why I say that because actually I think that's one of the key elements of mindset change that needs to happen. At CCPI, the assessment process has got a number of elements to it. Before a company can even come to us with its product information, the company goes through an organisational assessment, which looks first and foremost at its leadership and culture. And it does so using processes that we have adopted from other major hazard sectors, oil and gas, chemicals, nuclear, aviation, all use those processes to say what are the ethics and behaviour of this company? Is this company creating a culture and environment where actually if there are concerns about product information, they're being learnt and individuals within the company can speak up. So the first thing we do is look at the leadership and culture of a company and say, can you actually work to the standard that the code is asking you to? Because if you can't, we can't work with you. Because at the end of the day, at the code, we corroborate the information that's being provided with the claims that are being made in marketing. But we still have to rely on the manufacturer presenting us with that information as being correct. And we will look at it and we will question it if it doesn't feel right. But we have to be able to work with the manufacturers on a level of trust and approve. So that leadership and culture piece really matters. We've got to see that we're working with an organisation that has got those cultural behaviours in place. Only if they've got that and then also only if they go through our management system questionnaire and provide evidence behind the questionnaire and all of that is independently checked by one of our assessors. Only if they go through those things can they then show us product information around a specific product set and the marketing that goes with it. And only then will we look at what's presented and allow them to carry the mark. But even then, David, they can only carry the mark for two years. During that time, and this is for me the most important bit of the code actually, they stay registered with us. They are contractually obliged to continually improve their product information. So we can randomly sample anything that's out there that's carrying the mark and check that they are actually abiding by the code. And if they're not, we can call them to account to do it or remove the mark. And we also have, which I think is a key bit, a whistleblower sort of issues portal online where anybody looking at that product information, that mark, can come and tell us if they're seeing something that perhaps our sampling hasn't seen and we can get it corrected. So really what the code does is it gets manufacturers to present themselves to working to a certain standard that we've checked, but also to be willing to be held to that standard over time. So it is not a tick box. It is actually a continuous improvement approach. And fundamentally, it's about driving that change in that culture change of ‘you're responsible, you're accountable for your product information, you've got to keep it up to date and you're going to have to keep working on it.’ And that's much, much better than just saying, here's a list. You must do that. You mustn't do this. It's never going to change this industry.
[00:10:56] David: But…I can hear commercial directors in these organisations say, but this is cost. This is going to drive our costs up. How do they balance the commercial pressures with the regulatory and other pressures that they face? And particularly if you are, say, a manufacturer in the US or China or somewhere like that, you'll not, you've not been subject to the Grenfell inquiry and the reports and part of that culture, shall we say, or the behaviours. Do you hear any kickback on them from them?
[00:11:26] Amanda: Of course, cost is always the debate, isn't it? We're able to answer it very well at CCPI because we are not for profit. So we're not here to make money. We are here to engage the industry as far as, as much as the industry as we can possibly get to engage with us. So not being profit making helps us keep our costs down and be able to sort of cross transfer so that we can get from micro organisations right the way through to very large organisations and manage our cost base accordingly. So we keep the cost down and that does help keeping companies engaged. But you are right, there is a challenge for companies to sort of cope with what they're now being asked to do, especially in an environment where they've been in a fairly flat market for some time. The reality is, I think I turn that on its head, David, and say, what's the cost of not doing it? I think what we have seen from Grenfell, but actually not just Grenfell, you even look at the example of Lackanaw House is another example. You look at issues like the Scottish schools. Actually, what we've seen is there are costs to product information not being clear, accurate, accessible, up to date and unambiguous. And actually, it is one of those scenarios where I think it has to become business as usual and working with CCPI, because we're not for profit and we seek to keep the costs down, we create an environment where companies actually get real value. We recently went to the first wave of organisations who've gone through our process and asked them the difficult question, is this actually bringing value for you? Do you agree that it's helping you market your products better to customers, show that they can have greater confidence in product information? You ask a question like that, you don't actually know what the answer is going to be coming back. I was really pleasantly surprised to see 97% of the companies, the first companies that went through the process with us, came back and said, yeah, we agree or we strongly agree this is really helped us in positioning ourselves as an organisation that's being responsible with product information that you can have greater confidence in. And they also gave us similar percentages around how it's helped them engage their staff in it and how it's helped them engage their staff in culture change. I think that that's what matters. So when you're thinking about costs, there's also the costs of not doing it, not being part of the change.
[00:14:01] David: We kind of divide up, in BESA, we divide the industry into thirds. There's one third who get stuff straight away and understand they have to do it. And I would suggest that's the group you're talking to who've done the first lot. There's a second group who go, I don't know why I'm being asked for this, but I will do it because I need to stay compliant. And there's one third go, we're never going to do that. We're fine as we are. We're just going to ignore all of that and it'll be fine. Is that what you see within the manufacturer groups?
[00:14:29] Amanda: I think I'd make the percentages a little smaller.
David: Would you?
[00:14:33] Amanda: I'm afraid I think the early adopters in this industry is much smaller than 30%. That's not what I've seen. I maybe reduce it to fifths. So one fifth as early adopters, three fifths as that middle ground trying to work out why I should do this and engage with it. And the last fifth that's probably never going to bother. Sorry, that's probably very, I don't see the sector moving fast enough towards what I think is the future of this industry.
[00:15:05] David: So would you then, another thing we say is that we're an industry where just good enough is a bit too good. As long as it looks like the thing that you is in the specification that will do, thank you very much.
[00:15:18] Amanda: It's very hard because that I think that that does ring true, but not of everyone. There is a real world of where that is very unfair, where there are individuals and companies who really take this seriously and engaging with it. There's just not enough of them. That's all that just good enough. It probably does live in that middle three fifths that I mentioned, but perhaps in the back end of it, in the front end of it, there are those that I see starting to sort of look at it and say, yeah, we're going to have to engage with this. And perhaps what's held them back is is not necessarily the motivation that you're talking about, David, just good enough, but actually the reality of managing all of the other things they have to manage. You know, I think there's a little bit of that as well.
[00:16:05] David: As it becomes easier to check, do you think digital tools and technologies and maybe AI will help this become more widespread because it is easier to check? Therefore, people will check?
[00:16:17] Amanda: I think eventually, but I don't think now. Right now, we're talking about culture change. We fundamentally are talking about an industry getting a new mindset, which is about being part of collective responsibility and having individual responsibility. That is the mindset that when Judith Hackett presented the Building Safer Future Review, that is what she was talking about. You have a collective responsibility to deliver quality, safe buildings, but you also have individual responsibilities that actually she laid out very clearly, particularly in relation to high-rise residential buildings. But it's not just that. It should be across the built environment, obviously. Eventually, AI checking for different phrases or words that are being used and things can be very helpful. But then we're just back to checklists and tick lists. And that's what technology can help us with eventually. But right now, I think we're talking about culture change, and that's where at CCPI, things like our continuous improvement approach and being registered with us and making those changes and being part of reassessment over time, absolutely critical. We're not going to shift this industry without that.
[00:17:29] David: How do you engage with the SMEs and smaller manufacturers who might lack the resources of larger organisations? Well, they definitely will do, but to help them implement compliance frameworks?
[00:17:41] Amanda: Yeah, it's really important. It's particularly important in the manufacturing sector. Depending on whose data you look at, there's somewhere around 26,000 companies in UK manufacturing, and 19,000 of them are SMEs or micros. So they're micro, small, and medium. So big chunk of the industry. So it matters to us at CCPI to be able to work with SMEs. And so that's where our cost structure is really sort of weighted to be helpful and engage SMEs. We've still got to cover our costs, and we've got independent assessment, that costs, but you also get value out of it from a company. So we try to help by making sure we've got an appropriate sliding scale of cost. But actually, it's our system and process that we try to modify to help SMEs. And actually, yesterday I was having a discussion with, we have our monthly assessor forums where assessors come together to talk about the assessments they're doing, not in terms of the names of the company, but their experience of what's going on. And we were talking just then about how we want to modify our leadership and culture process a bit more so that actually, when we're dealing with a micro or very small organisation, you've got staff under 20, filling in a statistically significant culture survey and having assessors do validation interviews with individuals works well when you've got a large organisation. When you've got a smaller organisation, it's much harder. And also within those leadership and culture surveys, anonymity for the employee is actually really important. It's very hard to stay anonymous if there's five of you in a company. So our system and process for micro and small organisations is really being sort of shaped and honed by what we've learnt with working with the ones that we've worked with up until now. And there have been some very good ones step forward to say, how do we make sure we can get under the culture, under the skin of the culture of those organisations, but be able to really work with staff by talking to staff and understanding what's going on in the company and doing structured interviews rather than relying too much on a survey tool and validation interviews. So we alter it depending on the size of the company, because that matters for this sector.
[00:20:02] David: So in BESA, we represent companies engaged in design, installation, maintenance and building engineering services. So contractors, how would you see them using the CCPI?
[00:20:13] Amanda: There's a really important side of the CCPI, which is about clients, which is about the demand side, whether you're a client, whether you're a contractor, if you're demanding or you know, if you are part of the demand side of the industry, then you've got the opportunity to say, well, actually, I'd prefer to work with products that have been CCPI assessed and I can have greater confidence in their product information. And I know that that manufacturer is working with CCPI and willing to address issues that either have been found or when they're found, if something comes up that hasn't come up in the assessment. So there's a whole demand side supporter piece where companies can come to us and join pledge to support CCPI and promote CCPI within their supply chain. And we began that conversation in this very obvious place of contractors and developers to go to them and say, well, actually, don't you think you should be building this into your supply chain? And we're building quite a register of organisations that have actually signed up to it and are working through their supply chain to encourage and promote and engage them in getting on and doing CCPI. Members of the BESA could also do that, can also be looking for that or promoting that, encouraging that within the suppliers that they're working with. So just come to us and engage with us. We've got a pledge you can sign.
[00:21:40] David: There's currently a construction products reform green paper. How's that going to impact the CCPI, do you think?
[00:21:46] Amanda: So the paper, I think is a very important piece indeed. I think it was a very sensible thing for the government to do, to do a green paper. On the one hand, I was sort of frustrated to, when are we actually going to get the secondary legislation that follows from the Building Safety Act? Let's get it done. So on the one hand, I sort of wanted to just see the change happen. On the other hand, I think what they've done right and what they're doing right is to genuinely consult with the industry. It's a really complex sector, construction products and construction product manufacturing, and actually not jumping to conclusion and actually seeking to get it right is a sensible thing. So I think they're right to put it out there. I was really pleased to see that CCPI is mentioned a number of times in the green paper. I sort of learned some of it off by heart. And chapter six is all about putting safe products on the marketplace and product information. And there's actually a whole section and call to action, which says that the government expects the industry to adopt CCPI. And that just echoes calls that have been made by people like Dame Judith Hackett and Paul Morell and Anneliese Day in their report. So I really hope that what comes out of the green paper is that they follow up on that call to action, and they push further the adoption of the code. Because I don't think we will see the sort of culture change we need in terms of product information management, and therefore the quality of product information management go up without it.
[00:23:24] David: And looking ahead, what are your hopes for the future of construction product standards in the UK? And what will success look like? Do you think for CCPI?
[00:23:35] Amanda: I think the industry has a real opportunity. Like I said, you asked me, what was it like when I first came into the industry? And I said that, you know, on the one hand, I was surprised by some of the issues that clearly existed. And they're very substantial issues. And there's pretty clear proof of those issues exist in all sorts of corners. And then there is the horror of the Grenfell tragedy, which which makes it undeniable. So on the one hand, you know, I've been absolutely horrified by that. But I think that what it presents is the opportunity to really drive change for an industry to actually embrace what it needs to embrace responsibility, accountability, it's got to embrace those aspects and transparency. All things that this industry yet is not good at, and is not culturally what it should be doing. At the end of the day, we all should be playing our part in assuring that whatever building project we're in, the part that we're playing is delivering on building safety. Everybody has that responsibility. And if you haven't got that responsibility in your head, in your heart, if you're not winning hearts and minds on that, then I don't think you should be in the sector. That's the change that I want to see for the future.
[00:24:50] David: And does it go beyond building safety, though? It's about building performance, isn't it? So that actually, if you claim a performance of a product, it should perform to that standard that you claim it can go to.
[00:25:00] Amanda: Absolutely. And in fact, at CCPI, we don't just look at building safety or performance claims, we look at environmental claims, sustainability claims. If you're doing CCPI, actually, it will help you in the future with things like your digital product passport. At the end of the day, product information needs to be clear, accurate, accessible, up-to-date, and unambiguous, so that whatever we're using the information for, we can have greater confidence in it.
[00:25:29] David: And that's a great place to end it on, I think. So I'm going to try now and summarise what we've discussed. Good luck to me there. So you came into the industry as a complete outsider, surprised by what you found, but have a drive and desire to change the culture within the industry and behaviours within the industry. The CCPI has been set up to make sure that manufacturers deliver products that are safe, but also perform in the way that they are designed to do. There is an issue within the industry about the number of companies who are really at the forefront of this drive for change. Legislation will help that process on the way through. The clarity, the unambiguity of the information that's provided can only be a benefit to everybody within construction. Most importantly, I guess, those who occupy these and use these buildings. We always say it's important because 90% of us spend 90% of our time inside a building. So buildings that work is really important and the products are really important within that. And we're making significant steps, but we're waiting for the breakthrough on the CCPI to get real traction. Would that be a fair summary? I think so. I think we've got to push forward. There's still a lot to do. So once again, Amanda Long, Chief Executive, Construction Product Information Limited. Thanks for joining me on Behind the Built Environment podcast.
Amanda: Thank you for having me.
David: And now on to the podcast news. So join us for the must-attend event of the year, the BESA Annual Conference, which returns on Thursday the 16th of October with game-changing insights, expert panels and powerful networking. This year's theme, Race to the Top. Don't miss your chance to be part of the conversation shaping the future of building services and tickets are now available via the BESA website. Protect your business with BESA's legal support and training. As a BESA member, you can get access to expert legal advice, contract templates and dispute resolution support, plus free online legal courses via the BESA Academy. We have recently developed a new course, Understanding Collateral Warranties and Third Party Rights. So learn how to spot unfair terms, reduce your legal risk and protect your business on major contracts, and also available an Introduction to Contract Law, perfect for building your legal confidence. Start learning at the BESA Academy and explore your legal member rights today. Start learning at the BESA Academy and explore your legal member benefits today via the BESA. Start learning at the BESA Academy and explore your legal member benefits. It's all available at the BESA website for members. Thank you for tuning in to Behind the Built Environment. Don't forget to subscribe to our podcast for more in-depth conversations with industry leaders. If you enjoyed this episode, leave us a review and share with your colleagues. Stay connected with BESA for the latest updates and insight into our industry. Until next time, I'm David Frise and this has been Behind the Built Environment. Goodbye.
Episode 10: Behind the BPIC Network
In this episode of Behind the Built Environment, BESA Chief Executive David Frise speaks with Amos Simbo OBE, Founder of BPIC Network and Winway Group, about improving diversity in construction.
Amos shares his career journey and explains why representation, inclusion, and access are vital for attracting and retaining talent from ethnic minority backgrounds. He introduces BPIC’s mission to support inclusive workplaces and its upcoming Skills Academy.
The key message: inclusion benefits everyone and leads to innovation, better business outcomes, and stronger industry culture. For companies of all sizes, authenticity matters—don’t fake it, make it real. Inclusion isn’t a trend—it’s good business.
[00:00:00] David: Hello, I'm David FrIse, Chief Executive of BESA. Welcome to Behind the Built Environment, the podcast where I delve into the major issues facing our industry through in-depth conversations with key industry leaders. Join us as we explore the trends, challenges, and innovations shaping the future of the built environment. And today we welcome Amos Simbo, OBE. He is the founder of the BPIC Network and Winway Group and recently joined City & Guilds as an industry board member for construction. With a background in mechanical engineering from Loughborough University, Amos began his career as a trainee projects engineer before rising through the ranks to become a technical services manager. In 2019 he launched the BPIC network, a built environment inclusion organisation focused on improving ethnic minority representation, retention and support for minority-led businesses. It now has over 15,000 members and 45 industry partners. BPIC delivers career guidance, training and events to support and inspire talent across the sector. Amos also runs Wimwe Group, a growing M&E specialist contractor in London. Originally a small design consultancy, Wimwe has evolved into a key player in mechanical and electrical installations with ambitions to scale across the UK by delivering sustainable expert-led solutions. Welcome Amos.
Amos: Thank you so much for the introduction, David.
David: Absolute pleasure and you know the format of this so we start up with five quickfire questions which require a yes and no which sounds simple, is not so easy. The first one, has Donald Trump killed DEI?
Amos: No.
David: Do you believe the construction industry is making progress on diversity and inclusion?
Amos: Yes.
David: Is lack of representation a barrier for young people from ethnic minority backgrounds entering the sector?
Amos: Yes.
David: Can greater diversity improve innovation and performance in engineering and construction businesses?
Amos: Yes.
David: Should all companies have a dedicated strategy for recruiting from under-represented groups?
[00:02:21] Amos: Yes.
[00:02:22] David: And do you think visibility of diverse role models can genuinely influence career choices?
Amos: Yes.
David: Excellent. You passed that bit. Can you start by telling us a bit about how you, how you came into the industry, what your, what drives you and a bit about Winway?
[00:02:41] Amos: Yeah, absolutely. I've been in the industry now since 2011, finished my mechanical engineering degree from Loughborough University and I think I'd done a couple of interviews across sort of other engineering sectors and I found my first opportunity in construction at the time with an M&E contractor back then and lucky enough for me they were involved in the 2012 Olympics and I'd grown up in East London Leytonstone so it was quite close to me in terms of proximity so I got placed on site there in Stratford and got to see the completion of the infrastructure there, but also there at the Games, during the Games in 2012, which was actually quite good, as the company had a maintenance contract as well during the Games. So that was my start, you know, starting phase into the industry and I'd never heard about construction as the industry It's hard to explain, I guess, once you're in the industry, that there are people that walk past the built environment, but they just never really see it. I started seeing cranes when I was working in construction, but they were just around me. I never saw them. And it's just something that I never caught. So that was my first experience into the sector. And then from there on, you know, moving on to other parts in the sort of house building of the industry. So that was sort of my start there, David, and how I got into the industry.
[00:04:17] David: So genuinely a case of because you could see it, see it in operation, you thought, actually, I want to be part of that.
[00:04:22] Amos: Yeah, I think for me, it was more rather than seeing it in operation, what I'd studied, which was mechanical engineering, it didn't really suit me as a person. So I'd done some, you know, sort of, I call it internships with Lux and Rolls-Royce, seen some stuff with and sort of triumph national greed and all that which was more your design engineering side of things and that's not something that I really enjoyed doing as me as a person whereas when I came into construction there was a bit of a balance so there was the technical things but there was the people side of things where I could interact with people every day there were so many different things every day I was experiencing you can imagine on a a building site, you meet all sorts of people. And I really found that interesting, learning from people, interacting, and I think at a site level, I made friends really quickly on site, even though at the time, I was quite shy coming in, but so many people wanted to help me. So I think for me, it was, that's what caught my attention with the industry, to say, with this industry, I can be very dynamic, I can speak to people, I can interact every day and I can also do the sort of technical elements and things are always changing, it's never the same environment and there's a whole spectrum of people. I think for me that was the thing that really got me to say I actually like this industry and I never had, it wasn't a situation where I said I want to try another industry. For me that was that I should, this is what I like and I'll stay and sort of make it work.
[00:06:01] David: And help other people.
[00:06:02] Amos: Absolutely.
[00:06:03] David: Yeah. Let's grasp the nettle straight from the off if we can about diversity, equity and inclusion. How would you define that? What is it do you think?
[00:06:13] Amos: For me coming into this space I was also learning about what this is, what's diversity, what's equity, what's inclusion, but I think at the centre of it people should see it as practice of how people can access spaces, how people can see role models that they can look up up to, people feeling valued in where they are, where they're working, people feeling heard. I think at the bottom of everything that happens across the world, you know, it's mostly people feeling like, am I seen, am I heard, from whichever way you're looking at. You know, us as an industry, people feeling like it's a space that they can also belong. I would say, just to sum it up in terms of, you know, the diversity, the equity, the inclusion part, those are the underlying elements. And I also say it's not a competitive space. So it's not that when you're getting, when there's diversity, when there's inclusion, it should not be at the detriment of something else. It should be in the world, it should be inclusion. So inclusion shouldn't be about elements fighting each other. It should really be, and I think with how things happen in the world and how things are executed, it could end up being like almost like competitive forces fighting each other, but actually it should be about inclusion at the very bottom of it and that should be the underlying stream of we want to include and not exclude.
[00:07:42] David: So, because Donald Trump, I think, has described it as reverse discrimination. It's been caught up in the woke agenda and so become very political. I think what you're saying is that actually it's not, for me to win, you have to lose. It's a win-win.
[00:07:57] Amos: You're absolutely right. And I think people also just got to be careful, especially, you know, leaders out there running businesses and all that. You know, politics is a political game, yeah? And it comes and goes, it changes. And that's just the nature of politics, you know, from time, you know, politicians, they lean on elements they think will leverage them, support for different agenda. So it might be that if they want to introduce a completely different policy to young people, they'll give them free toys. And they might look like they love toys, but actually that's not the end goal. That's just leverage to win over certain people. So I don't think businesses should really be so much influenced by the political environment. However, politics, and as you know, for big business, you know, or let's say the public sector, is a big part of big businesses, and how policies are shaped is also in line. So I think it's for businesses to really, you know, so it shouldn't be something that's divisive, but I think what makes things divisive, or politicians to play on the division, is how things are executed. So we're in executing policies, and in the nature of things, some people feel like they're being excluded. That's what then attracts the politics to that, to say I can take advantage of this. But the origins of it has been in how elements around inclusion and diversity are being executed. And I think that's what should really be corrected. But as businesses, it's all about the people that are working for the company. And I think business have to tread a fine line sometimes. What's happened in America is, I guess, with the whole Donald Trump thing, I think it's not just an inclusion, it's on so many different things that we're seeing, like tariffs and all this, I think it's on the extreme end. And it's putting a lot of the businesses in a very difficult space, because some of them want to be inclusive, but they're being told they'll lose their contracts if they do that sort of stuff. So it's like, what do you do in that case? And try and have a balancing effect, because if they lose the contracts, they won't have the people in the first place to employ. But I think the principles shouldn't really change with and business, I think they gotta be careful because it's like, how do you reverse that? Let's say if there's a change of government, are you gonna go back to your people and say, well, we care now because there's a different government and you don't wanna be there. So I think businesses should really, really think about the messaging of how things are and how things are being shaped. And I'm sure some already stuck to their guns in terms of weathering, riding out the storm and all that sort of stuff. But I think as an industry, as businesses, inclusion should not be about exclusion and it's something that we should have and we should continue with, despite what happens out there and all the political influences.
[00:10:55] David: So if we turn to the construction industry, I think more than 18% of the UK population is from the BAME community. However, they're less than 7% of our workforce in construction or construction related professions. Why do you think that is?
[00:11:12] Amos: I think it's a number of factors, to be honest. I think the industry itself can do a lot more to just open up to wider society. So you probably see certain numbers around women, et cetera, et cetera, as well. I think as an industry, it's such a people ingrained industry. I think the leadership of the sector as well could be a bit more joined up, aligned, whichever way you want to put it. You can see it, and I'm not just talking about the industry people, I'm talking even from government level, where there's very focusing leadership to really address, I mean, we've had issues, for example, just kind of going off a tangent, we've had issues around mental health that's gone on for a really long time, and I recall I was on a call with one of the leading non-construction industry body, and they were talking about mental health, they were talking about the NHS, and I said, look, when it comes to things like suicide, construction is three times more. Do you know that? And they were actually quite shocked. They didn't know about it. But they were on a call to address mental health across all industries, and they just didn't know that actually, in some aspects, you're barking in the wrong tree. Like, you probably should be addressing where it's the most affected, and then look at, so I guess it's the, you know, how the industry is represented out there, the people that are sitting in this. So what I'm getting at here, David, is it's a number of issues of why that number is low, because that then translates to, so you could look in a simple way to say, I just because there isn't any ethnic minority leaders and all that, but that's not the only reason. There are other mechanisms in there that are then leading to those outcomes of actually the reason there are a lot of minorities because it could be for the fact that people from ethnic minority backgrounds just don't know about that sector to start with. It doesn't reach out to them. And then people coming in don't stay, they might be leaving. So you might not end up with role models, people that can look up to you. I mean, you could ask parents that are in the industry to say, would you let your kid come into the sector, whatever their ethnicity is. And you get some answers, people be like, no, I wouldn't. And that's not an ethnic minority thing, that's just an industry-wide thing. So I think that there are different factors in there which then lead to the numbers being low and not being representative of the society.
[00:13:36] David: Is that, we use the same argument, it doesn't matter where the kid's from, parents discourage children from going into the industry, teachers discourage, so that's the same across the board. Are there any unique things, do you think, which are preventing people from the BAME community coming into the industry?
[00:13:55] Amos: Yeah, I think it could narrow it down to a few things. One of which will be people not knowing about the sector. Like I said at the start, I didn't know about the industry and my dad is an engineer in maintenance, facilities management and all that. So it wasn't that, it's not that I wasn't, I was actually quite close to the industry. I just didn't know about this, the construction side of it. So I think people knowing about the opportunities available within their own communities. I think when it comes to reward and salaries, we're actually quite high up there across all the sectors. So people are well paid within the sector, but people don't know about it. So I think that's one element of education. But then some of the reasons why people wouldn't know about it is from where they're from, perhaps there isn't any success stories of people that would say, you know, I've come with the industry. So from where I'm from, people will be encouraged more to go into, to be a doctor or a lawyer because they're the success stories people are seeing. So the other factor will be People, when they come into the industry, at times they don't make it, they don't progress. So they can come in, stay in the industry, not progressing, and then they end up leaving. So you're losing a lot of leaders, losing a lot of role models. And the reasons for that, there's quite a few of them, but it could be that it's such a people-oriented industry, so you end up with people that are in their groups and cliques, continuously working with people in their groups and cliques. And in a roundabout way, that was one of the reasons behind actually creating a network, to say, we're such a people-oriented industry, so you need to know people. As a way of solving, it might not be the perfect way to do it, but it's to say, if you're a network, that could help. So that could be a second reason of why people are not exposed or come into the industry and do not know about it, because the role models that they see, they see themselves staying, and all that is just not there.
[00:15:49] David: That's perfect, because I'm going to come on to the BPIC network in a moment. But before I do that, I just wanted to say, why would companies be interested in this? What are they missing out on by not being as diverse as they could be?
[00:16:02] Amos: Some companies, in some aspects, could be missing nothing. And that's probably not something that you'd hear out there but they could just be missing something. But I think as you're growing, you're growing your teams, your businesses and all that, I think there's a sense of belonging people also look at when they're joining business. It's for businesses that really want to grow, want to encourage their own innovation, and really want to progress with the way the world is progressing. I think that there's a lot of things that you could learn from having a mix of diverse teams. The most obvious was innovation, and people thinking differently, and profits, and all that sort of stuff. But that's an argument you put out there to say the reasons you should be diverse and inclusive. But actually, the underlying reason for me personally, should just be, you know, people feeling like, you know, they're welcome in your business and they can stay in somewhere where there is access. Because in that, that's where you get the talent, you get all the benefits, et cetera. But the underlying thing should be, would you not want your business to be a place where talent can thrive, people can come in. And when it talks, like I said, when we're talking about inclusion, we are focused on ethnic minority inclusion. But it doesn't mean your company should just focus on that. You should focus on everyone being included. So you don't wanna make it divisive within your own business. So it should be an underlying theme of we're an inclusive business. So if you are lacking ethnic minorities, then you can make an effort on that. If you have people in your network that are probably, I don't know, women, then that's an area you can address. If you have an older population of people in your business who are like, Oh, we want to be more flexible in our working. That's an area to focus. It should not be divisive. The underlying, the underlying thing should be one inclusive organization that want to keep our people, that want to encourage, um, good culture within our business, that want to encourage, you know, people thriving and people, you know, making a cross and that really should be, um, a value that a company holds and genuinely holds.
[00:18:13] David: So basically it's just a good business.It makes good business sense.
[00:18:13] Amos: It makes good business, it makes good business sense, and then that business sense translates into, you know, into other outputs like, you know, your business growth, you know, people retention, your creativity, etc, etc, all growing. That's some of the benefits that you'd have from doing that, but the underlying theme should be, you know, the values and then the outcomes that you get from that.
[00:18:37] David: So tell me a bit about BPIC, what is it and who's it for?
[00:18:43] Amos: BP Network, we started it just as a network out there to, like I said before, to try and get people access to say, look, if you feel like this is not your industry, actually you might be wrong. It actually is your industry. You belong. And the fact that you're on your own or you see people like yourselves in your business doesn't mean you're the only one across the sector. So there is a network here that's to support you. And then on the other hand, if you're a non-ethnic minority and you feel like, you know, our industry should be inclusive and we should see people from other backgrounds thrive and come into the industry, it's also your network. So the network itself is for everyone that believes our industry should be inclusive, irregardless of their ethnicity. And that's really at the core of our network to say the narrative of the built environment slash construction, we can write it ourselves. There is a, in any walks of life, there's a big percentage of people that believe in doing the right thing, and, you know, everyone, you're having, you know, good opportunity and all that, but typically, those people never do anything about it, because it might not affect, directly affect their life, and for us, it's to say, let's put a good image to our sector, rather than our sector being misrepresented out there, And there's a lot of people that actually, and that's our network group, with people saying, actually, this is what our industry is. Our industry is not people being out there whistling when they're building sites. Our industry is not builders making noise at midnight and all that sort of stuff. Our industry is not bad practice, which you typically see as highlights, especially in media. They always talk about things when they've gone wrong, but actually no one is saying, this whole city has been built the right way. You know, like things are very functional, all the skyscrapers you're seeing, all the engineering that you see is actually working. But what you see is always the negative things. So our network was set to say, we can actually paint a good image to what our industry is. Our industry is inclusive, our industry is very supportive, our industry wants people from all backgrounds to come in and thrive. And that's really what's at the core of BPIT network, to say, that's the message we should be pushing out there. And it's for everyone, despite this, who really believes we can make a difference in our industry and have our industry also follow the trend of other industries, like, you know, IT became tech, very attractive to young people, so many success stories. And I believe we can do the same thing following the same narrative.
[00:21:24] David: If I'm running a small business and I've really, you know, I don't know where I'm based, but I employed five, 10 people. Should I be involved in the network? And if so, how do I get in?
[00:21:38] Amos: Yeah, absolutely. So the network itself, like if you're too few five man band, you probably on the face of it, not gonna be so diverse because you know, it's mom, dad, uncle, you know, it's a business. There's nothing wrong with that. We're not here to be pushing, to say, do this, do that, do that. No, no, no. The whole point of it, what's underlying is, we wanna give access to our industry, when I painted the right image to it. So as a small business, it's giving you the right tools to be inclusive and showing the spaces where you can go to access talent, to diversify your viewpoints on things and to really help our industry grow. So if you're a small business, when you're talking about the BP membership, for example, we have our small business membership, which really what we're doing is giving the assurance that you've got the right things in place to reach a wider audience as a small business. Big businesses have got different capabilities really, and we do a lot more with them, but it's the underlying thing for us, for small businesses, if you really want to have an outlook there to say your business is inclusive, it's got the best practice in place, you've got a reach, that's what we do, and we're here to support that for the small businesses to really thrive within our sector.
[00:22:52] David: So what sort of supporting things do you do for your members and the industry in general?
[00:22:57] Amos: Yeah, so for the industry in general, starting with our membership. So companies are really looking at the best guide and best practice when it comes to strategies. If you're looking to attract diverse talent, strategies on how to retain that talent when it comes to the cultural practices of a business. And from attracting people, we've got the the network itself. So it's giving that access to people, you know, jobs, et cetera, et cetera. When within a business of how you can structure things, which again, have an impact mostly on retention and keeping people valued in some instances, because it's in the name is an ethnic minority. So you're going to end up with minorities within your business. Yeah. And sometimes not seeing someone like yourself can have an impact on a person. And it's the So how'd you get around that? So it's that best practice that we provide. And then on the other hand, we've got engagements across the sector that we do. We do lots of events. We do lots of events where the big and the small businesses can also meet each other and align with companies that have the same values. So if you're a small business, we have a lot of large organizations that we work with. So we've got something like a small business breakfast that we do. We have an award ceremony that we run each year at the end of the year. And we've got various networking events in the middle. And one thing that we have coming up now, only because we're growing and we're able to, well, we're launching a skills academy. This is the first time I'm saying it, by the way. So I like your podcast. And it is to do with the whole drive for construction skills lately, so that we can grow our workforce as an industry. And we're part and parcel of that now. We're really, we are partnering with training providers, so we can bring in people from our network, but we can also connect them to the industry, so big and small business industry, on that space that we're looking at, because most businesses, especially small businesses, you want people to hit the ground running? You know, people, the government is saying they're training people and all that sort of stuff, but small businesses don't have time to then train again. So we're looking at how we can get around that with the Skills Academy. So all those three aspects there, David, is how we, the sort of work that we do with our members, and there is a team of six, luckily enough now, where I don't have to run around everywhere.
[00:25:21] David: Well, thank you for that exclusive. And you should be talking to the BESA Academy at Short Canal. Oh, brilliant, absolutely. Certainly around the course content, those kind of areas. We talked a bit about mentoring. Is that something that you think is really important?
[00:25:35] Amos: Yeah, I think so, yeah. I think mentoring is really important. I think with increased capabilities now, especially with the academy, we're looking to encompass that, where people that are coming in, they get the right skills or training, let's say with Visa Academy, I'll be really happy to discuss that. And then they get the right training. However, they'll need a network to support them as well in terms of staying in your sector. One thing I've benefited from is I got mentored by people, but it wasn't labeled mentoring. It's just people that really took their time with me to show me how things are done. And sometimes it can be quite difficult because the industry itself is, you know, people are really busy in what they're doing. is you're always driven by a deadline somewhere, or every time you come to work, there's a program on the wall telling you that you're behind. So you never have time for anyone, of which for me, that's the number one thing I really benefited from, people coming, you know, really just give their time. And it's small things, small things. So that mentoring really goes a long way in terms of guiding people along their career, showing them what they can do, because you've got so many different things. You've got, you know, lack of confidence, all that when you're coming in. But then there can be a different dimension, which is more career coaching, where people sometimes are at the mid-level and they feel like they're hitting a ceiling. And it's like, how do you break through to the next level, you know, getting senior. So it's an area that we work with and we collaborate with across the sector.
[00:27:01] David: So final question on this section, that really is, it often comes up in sort of social value exercises as part of the training process. And I strongly believe that we kind of have an industry there's a big difference between what you say you do and what you actually do. Do you see that there is a gap between what people say they do and actually do deliver, what are their outputs?
[00:27:23] Amos: Yeah, I think so. Yeah, and I think, like I was saying initially, the underlying factor is it should really be something that to make it easy that a business really believes in to start with. And that's only because if you really think about it, if you're faking it rather than actually doing it, you're also just wasting your time. So you might as well use your resources properly because what's the point of investing into something and then just going halfway? Because what will happen is we see it sometimes in this sector where companies, they would employ people to do this, but then they're just not empowered to do anything. So it's almost like you're actually wasting money on employing those people. And if someone was to look at, let's say an exec, I mean, you're a chief exec, you know, look at the business and say, well, what have we gotten from this? And there's nothing, so it might sound bad, but it's probably better off not doing anything to start. Because at the very start, you're actually wasting a lot of time and resource. And it's just better to go all in. In some cases, things are led by, you know, from a client perspective. So companies feel like they have to kind of like, you know, pretend they're doing it. But for me, I think the best approach is, if you're doing it, even if you don't wanna go all out, try and do the bare minimum properly, at least. So you can say, you know what, we're not doing everything, we're just doing this, but we're actually doing it properly. Otherwise it end up being a waste of time for you and the business. So we do see it every now and then. And I think progressively, it's probably gonna get less and less. I mean, you can never tell. But I think businesses should just have to commit to it or not commit to it. And the middle ground really benefits no one, you or the business. It should just be something that's a company value.
[00:29:16] David: Well, Amos, I'm gonna try and summarize now what we've discussed. And you're gonna correct me if I'm wrong. Basically, Donald Trump has not killed diversity, equity and inclusion. It's got life in it. It makes good business to be more diverse, you have a better company at the end of it. You should get involved in the BPIC network because you'll learn more about how to become more diverse, therefore a better company. And if you're gonna do it, don't fake it, make it real.
[00:29:46] Amos: Absolutely, yeah, I think you summarised it really well and I'm really happy I came today.
[00:29:50] David: Once again, Amos Simbo, OBE, founder of BPIC network and the Winway Group, thanks for joining us on Behind the Built Environment and good luck at Windsor Castle when you get there.
[00:30:01] Amos: Thank you so much, David. I really enjoyed the podcast and I'm equally looking forward to work with the Visa Academy going forward.
PODCAST NEWS
[00:30:16] David: And now onto the podcast news. Catch our on-demand Visa webinar featuring Amos Simbo, founder of the BPEC Network, as he explores how businesses can unlock growth by embracing inclusive practices, Building a competitive advantage through diversity, strategies for winning business and attracting top talent offers practical insights into creating diverse teams, improving representation and leveraging inclusion as a business strength. Whether you're looking to attract new talent, win contracts or drive innovation, this session is packed with valuable takeaways to help you lead with purpose and impact. watch now at thebesa.com forward slash webinars and entries are now open for the Equality, Diversity and Inclusion Award at the BESA Industry Awards 2025. This category celebrates individuals, teams or organisations driving real change in building services, championing inclusion, breaking down barriers and creating a more diverse and equitable industry. If you're leading by example or know someone who is, now is the time to shine. Enter today via the BESA website and let's celebrate the people building a better future for everyone. And join us on the 19th of June for the BESA Clean Air Day Walk, a powerful event supporting the Ella Roberta Foundation, raising awareness about the dangers of air pollution. Whether you're strolling through the city or hiking the countryside your steps can make a difference. Choosing from two inspiring walks, a London route starting at Ellers Memorial, exploring air quality through live data comparisons sponsored by S&P UK and led by the BESA IAQ group. A Peak District walk on the 20th of June led by the BESA Next Gen group and sponsored by NewAir leads in an energizing and scenic trek up Mam Tor to show young professionals commitment to cleaner air. Air pollution causes 43,000 UK deaths a year so it's time to act. Walk with us, raise vital funds and help spread the word about indoor air quality and health. Sign up, sponsor or donate at thebesa.com/cleanairday because every breath matters. So thank you for tuning in to Behind the Built Environment. Don't forget to subscribe to our podcast for more in-depth conversations with industry leaders. If you enjoyed this episode please leave us a review and share with your colleagues. Stay connected with BESA for the latest updates and insights into our industry and until next time I'm David Frise and this is Behind the Built Environment. Goodbye.
Episode 9: Behind Build UK
In this episode of Behind the Built Environment, BESA Chief Executive David Frise speakswith Suzannah Nichol, Chief Executive of Build UK, about her career journey and the organisation’s impact over the past decade.
They explore Build UK’s role in improving payment practices, introducing the Common Assessment Standard, and tackling industry-wide issues like productivity, skills shortages, and cultural change.
Suzannah shares insights on the Building Safety Act, the importance of collaboration, and embracing innovation and AI. She highlights the success of the Open Doors initiative and emphasises the need for the sector to modernise, reduce duplication, and unite around shared goals.
David Frise: Hello, I'm David Frise, Chief Executive of BESA, and welcome to Behind the Built Environment, the podcast where I delve into the major issues facing our industry through in-depth conversations with key industry leaders. Join us as we explore the trends, challenges and innovations shaping the future of the built environment. And today our guest is Suzannah Nichol. Welcome, Suzannah. Thank you very much, David. Suzannah is the Chief Executive of Build UK, the leading representative body for the UK construction industry. Her passion for construction began with a site visit during work experience, leading her to study construction management and begin her career as a site engineer. She later qualified in health and safety and went on to lead the National Specialist Contractors Council. In 2015, Suzannah spearheaded the creation of Build UK by merging key organisations, uniting the industry under one voice. Under her leadership, Build UK has driven major industry improvements, including better payment practices through benchmarking and the introduction of the common assessment standard. Suzannah is a respected voice in government, the media and across industry bodies. She holds an MBE 2005 and an OBE 2024 for services to construction. Her leadership roles include serving on the Construction Leadership Council, Building Advisory Committee, Women's Business Council and others. A strong advocate for flexible working, she also one of Timewise's first power part-timers. Again, welcome, Suzannah. Thank you. We like to kick off with quickfire. Yes, no, it's more difficult than it looks on this one. So, here we go. Will the building safety regime be delivered in the next 10 years? Should say fully delivered. No. Will we ever not have a skills crisis in construction? Yes, but not a crisis. Can the industry help deliver the government's targets for growth and house building? Yes. Are buildings safer now than they were before the Grenfell disaster? Yes. Has collaboration across the sector improved since the formation of Build UK? Yes. And finally, one for our members. Will cash retentions ever be abolished? I'd like to say yes. So would I, and I know our members would. First of all, how did you come into the industry? What was it that drew you into construction and what held you in construction, shall we say?
Suzannah Nichol: Back in the days when at school you did work experience, I did two weeks work experience, a week in a children's nursery. I thought I might like to work with children. One week in a nursery put me off that. I went out on a week's work experience with a friend's dad who was an estate agent. And one of the days he took me out on a house building site. I presume he was responsible for selling the houses. And as soon as I walked on site, the noise, the smells, the look, I just knew there and then I wanted to be part of that. So I went home to my parents, my father's a police officer, my mother's a nurse and said, I want to get into construction. And this is before the days of Google and the internet. But we found a company willing to sponsor me and I toddled off to Liverpool University to do a construction management degree. And I've loved it ever since.
David Frise: Yeah, I wonder how many people have had that experience for the first time they went on a building site and they loved it. But that's great to hear. And no regrets since?
Suzannah Nichol: Not at all. I was out yesterday on HS2 Old Oak Common project, part of our Open Doors initiative. And I had that same feeling. And this is now 30 something years later. And I just love the buzz, love seeing what we do, seeing what we contribute to society. I pretty much enjoy every day I go to work. I think I'm really lucky in that. But there's not a day that I've regretted joining the construction industry.
David Frise: That's great to hear. So Build UK reaches a significant milestone this year, which is 10 years. Can you tell us why was it created? And what would you say are the organisation's most important achievements?
Suzannah Nichol: It was created, if I look back about 17, 18 years ago, when I was sitting around tables, particularly in front of government with an ever changing array of ministers, and the industry would sit down with its various voices and bodies and essentially argue amongst itself in front of the minister of the day, which gave them complete licence for them to make the decision. And I think the industry should have, should be ones making the decision. A lot of what we do, a lot of what we could change is within our gift. So I sat there thinking about how we could do this differently. The first step was to start organising the industry before it went to the meetings, work out what we agreed on, and talk about that, not the things that we disagreed on. And then there came the opportunity to bring together initially that what we call the core contracting supply chain, the major contractors, the tier one contractors and the specialist supply chain, which I represented. And there was an opportunity with two people. So James Waits, who was chair of the tier one contractors group, and Kevin Louch, who was chair of the specialists, to do something different, to actually say, shall we bring everybody together? We then have the difficult conversations round the same table, but we work out what we agree on. And actually, most businesses at their core, we agree on the same things. We want financially resilient, good, strong, safe businesses that employ people, that deliver great buildings, and we grow as a sector together. And I often say we fight over the slice of the pie, whereas if we grow that pie, there's much more for everybody. So that's what led to the creation of Build UK. And to answer the second part of that question, I think people thought it would be more difficult than it was. Right at the beginning, there were a few voices who said, you'll never do it. You'll never come together. Within nine months, both parties had said, yes, let's give it a go. It's almost what could possibly, you know, what's the worst that could happen? Having everybody around the table immediately changed the conversation, and it was really refreshing. Yeah, there's difficult conversations. You mentioned retentions earlier. We still haven't resolved that. But we've made steps forward in it. We've fundamentally changed the conversation on payment, and we've improved payment metrics. So you ask, what have we done in that time? We've improved payment metrics. Our members, when we started benchmarking them, and transparency is key, when you start to put things in a league table, it starts to drive different behaviours. Our members have improved their average payment terms from 45 days. Now it sits at 29. That's big. That's in the last seven years. We've introduced the common assessment standard. So we've started to unravel the very complicated landscape of pre-qualification. I think there were 21 schemes. You now can get the common assessment standard from recognised assessment bodies. And it teed the industry up for when the Building Safety Act came in. We didn't have to start for a new scheme looking at organisational capability. We said, you know what, we've got one of those, and a lot of people are signed up to it. We added in the building safety changes, the questions, so we hit the ground running, which is a first for the industry to be lined up, ready to go, and everybody saying, yes, we can do this.
David Frise: That's one of the big things, I think, for Visa members around that common assessment standard. How do you see that operating in the future? Many of our members have multiple accreditations. Is that how you see it continuing, or is there a better way?
Suzannah Nichol: Absolutely not. The objective is you should have one, you should have the common assessment standard, and that will be recognised by clients, contractors. Everything in construction is a long process. We're a huge industry. We all want the same objective, or most people, but we often try and get there in the most complicated way. I often say in construction, why have one piece of paper when you can have 10? So what we've done so far is we now have government recognises the common assessment standard. So the public sector is encouraged and advised to use the common assessment standard, and we're seeing that. We've just updated it for the new Procurement Act. Almost all of our contractor members now require the common assessment standard. The challenge comes in trickling that down through every division and every department in every contractor. So they ask for the common assessment standard. And stopping that construction not invented here syndrome. So we like the common assessment standard, but we want a few of our own questions. And it's saying, stop, bring the questions to the table. If they're valid and everybody wants them, we'll consider incorporating them. Stop adding layers just for the sake of it, and having those open conversations. So I see in the future that will be the requirement, the common assessment standard. It's in some of the frameworks now. It's in the government's biggest framework. It's been used by MHCLG for the cladding remediation project. So we're getting there. There's a huge role for the supply chain here as well. When they're asked for something, and they've got the common assessment standard, they should turn around and say, we've got the common assessment standard. We've jumped through that. We've achieved that. And then they should come and tell you, and they can come and tell me. And we can go and have that conversation saying, why are you asking for this? And often it's not really understood why. And I think we can do a huge amount in saying, you don't need to do that. This is the industry accepted standard. Now let's focus on something else that's really going to make a difference.
David Frise: That's one area where the industry duplicates a lot, and therefore that costs a lot of money and adds no real value. Productivity is one of the key areas you've focused on. Where do you see the kind of easy wins? Well, I think you've discussed there are no easy wins in construction, but where's the point of attack on productivity? Because we have lamentable productivity, not just in construction, but in the UK generally.
Suzannah Nichol: We have huge waste in construction. When people talk about productivity, the challenge is everybody sees it as slightly different, different reasons for it, different definition of it. Duplication is one way, and we find that all the time, where we'll issue a simple industry standard that the majority sign up to. And everybody says, we'll just add our own little bit to it. So we have to try and stop that mentality. And demonstrating how wasteful it is, I'd much rather, for instance, on pre-qualification or demonstrating organisational capability, people said, what will really make the difference on site? What will make us safer? What will improve the standard? It's not filling out another piece of paper. It's paying for whether you bring back your clock of works out on site. It's spending more time upfront in the design of your project. So you know it complies with building regulations. You've considered all the issues. You've modelled it. You've used BIM. Every time we do something that's waste, maybe we should actually start to say that, but this is incredibly wasteful. How can we do it differently? So that common terminology. But you see it everywhere. From the lack of use of technology on site, we could be so much more productive with some real simple adoptions of technology. Online forms rather than paper forms, up to some massive big decisions, such as sorting out design problems before we get on site. And then we're reworking out on site.
[00:11:35] David: Yeah, we often start projects too soon. And therefore, we're into building design rather than design and build. There's an ongoing conversation around the need for the industry to develop a new culture, and not least because of its response to the Building Safety Act. But what practical steps do we need to take to turn that into a reality, do you think?
Suzannah Nichol: Changing a culture is a really difficult thing to do. Again, everybody thinks you mean something different. And I often talk about if you want to change something, which is turning a big cog, you need to turn lots of smaller cogs to get that big cog turning. And the industry is reasonably compliant. It likes structure. It likes rules as a principle. So looking at some of those smaller things that make people's lives better, take competence. It's really difficult to turn the big wheel on making sure everybody's competent if we don't have the standards in place. If we don't, not everybody's checking cards when they go on site. Not everybody is clear on what qualification is good looks like. And when you have people saying, I've got 40 years experience in the industry, I'm fine. So addressing each of those little cogs and making a difference there actually starts to turn what some people would call the culture cog, the culture wheel. So by doing some of the smaller things, the pieces of the jigsaw, you will change the culture. You don't change a culture by saying we need to change a culture.
David Frise: Now, indeed, and there is a kind of a cognitive dissonance in the industry, the difference between what people say they do and what they actually do. And I guess the reporting piece around the payment leak tables shows what actually happens rather than what they say happens. I've just come back from the US. There was a huge, to the MCA conference, which is our equivalent in the US, a lot of talk about AI and how they are developing AI tools for back office function, but also in sort of engineering functions. Do you see the use of AI being used in construction a great deal more, and particularly around maybe that reporting, the difference between what you say you do and what actually happens?
Suzannah Nichol: The potential is huge,not just in reporting and some of the more ways we think of, the easy ways. Out on site yesterday, they're talking about using drones to deliver. They're talking about where you could have automatic paint sprayers. So you will no longer be looking for people to paint the wall. You'll be looking for people to operate the equipment that paints the wall. We are behind the curve in that. There's a whole range of reasons. Construction's high risk to change things. Change is so big, you'll only find out it's not working when you're into what could be a two, three, four, five-year project. So it's quite massive to actually take the step and say, we're going to do something different untested on this project. That's part of our challenge, but it's also a huge opportunity. So I absolutely believe that going forward, we will look back, a bit like we've all got a phone. I no longer carry an A to Z. I no longer carry a credit card. I don't even carry money these days. If I can't pay on my watch, I'm not buying. That's technology. That's AI that has crept into our lives that I didn't even know I need, but I now wouldn't be without. And I truly believe we've got that huge potential in construction. The fact that we require lots of small firms to make that investment is our big, big challenge. We need to say what would make the biggest difference and everybody lean in and say, do you know what, we're going to do that first.
David Frise: Yeah. They had an interesting slogan saying AI will not put you out of business, but a company using AI might.
Suzannah Nichol: Absolutely. First of all, we have got a skill shortage. We've got a labour shortage. So worrying about it, taking jobs absolutely should not be top of our list. I think the skills will change and I suspect that will play into the next generation as well, who are much more used to running their life on a digital platform. So inviting them into operate equipment that paints walls is probably a much more attractive proposition than inviting them in to paint the walls. So again, huge opportunity that will also then back to reduce our waste, drive our productivity. I'm back to, it's quite exciting working in this sector.
David Frise: We touched earlier about the skills crisis, shall we say, and you've talked already about open doors and going out to the HS2 site yesterday. Can you tell us a bit about HS2, sorry, open doors rather than HS2, but open doors, what it's about and how that's going to help us with the skills shortages?
Suzannah Nichol: Open doors is an initiative run by Build UK where our members and others open up their, not just construction sites, that's the main, but we open up offices, workplaces, we've got some virtual events, we've got plant yards, depots, anything and everything where we open them up across a week and young people, particularly schools, colleges, universities we target, but also anybody in the community can come on a live construction workplace and see what we get up to. We have so many jobs in construction that we find it difficult to explain in a 30 minute careers talk, it's really difficult. So bringing those young people outside and showing them what goes on means they start to ask the questions, they start to see the range of opportunities. And we know from our research that 88% of our visitors to an open doors site would then consider a career in construction. So it's that first step from their journey from education into employment, which is really difficult in this country. Even yesterday I had a group of college students join me and they didn't really know what they were up to. By the time they'd heard from people on HS2, they'd seen the project, they were buzzing. And the kind of things I was saying, well have you had any work experience? Well no. Right, you need to get out and get some work experience. But they were much more excited going back to their college course because they could see what they could be. The next step for us is when they leave is saying, and this is your next step. And we now have to build that because it's really difficult to get a job in construction. We've got a skills crisis but we make it really difficult for people to join us. And trust me, people want to join us. We do not have a recruitment problem, we do not have an attraction problem. We've got a lot of young people on courses, they just can't make that step from that course into the industry. And Open Doors is part of that. And it gets the employers engaged as well. Employers are seeing that potential and we often find they find their next apprentice on those Open Doors visits because somebody comes up and says, I'd love to work here. And they say, happy days. Our apprenticeship programme starts in a few weeks, here's the application form. So it really connects the industry with people we want to join the industry.
Suzannah Nichol: The average age, I think, is in the 50s in the industry. And we've talked a bit about culture change and how the industry is developing. Is it a generational change that's going to be required before we really start to see a, shall we say, purely digital, modern industry in the form that we all want to see?
Suzannah Nichol: I'm not sure life changes quite like that. There's lots of pockets of people of all ages who are doing amazing. Our industry does amazing, fantastic things. I saw that yesterday out on a site visit and my colleagues in Build UK have been out and about and are coming back full of what they've seen out on site. There are ways that we can help ourselves. We can look after our current workforce better, demonstrate to them the value that they're delivering. People really undervalue what we do as construction. We take buildings for granted, we don't understand or we find it difficult to explain. People sometimes aren't that interested in how things are put together. I believe we're missing a trick with our older workers not getting them into college when they can no longer work out on site. They've got to be the best people to go into college and inspire that next generation and talk about all the good things that we do and share some of those traditional ways of working, the good traditional ways of working, but pass on the skills that they've got and get that next generation excited about doing the same thing. Digital's part of that. A couple of the jobs you see out on site, you sit there going, we still do that by hand. There's got to be a solution to it and the next generation coming through will be the ones who say, well I wouldn't do it like that. Okay, tell us the answer. So there's waves, there's layers, it will change and I suspect that in 10 years time we'll look back and go, did we really used to do that? At least I hope so.
David Frise: Well that was one of my questions actually. The differences between sort of 10 years ago and now, I think if you went back you'd be going, good lord, did we used to do that? Do you see any massive difference between when you formed Build UK and now significantly? So you went on site presumably 10 years ago and now, would it be like going back in a time capsule?
Suzannah Nichol: I think they do say that if the Victorians were alive they'd be able to come and build a house because we pretty much still build houses. They've got a bit more tech in them but we still build houses the way the Victorians build houses. There are changes. Where you really see it is in health and safety, is in welfare facilities out on site. The site I was on yesterday, I think it was two kilometres long, it was spotless. It was just a beautiful project to be out on. Yeah, there were some new technologies there, the way they were pouring concrete for example, some of the precast coming out on site, some of the, you know, just seeing the tunnel boring machine. You talk about advances in technology. There are some, there's too much that's the same I would say but there are some things that we do differently. We just need to move more at pace but the only way to do that is everybody to stop rowing their own boat down the Thames, you know. We might get to Isleworth for a pint and say we're all going to play to our strengths and get on a liner and we're going to go to New York and that requires even more leaning in and everybody saying if we're going to fix three things what would make the biggest difference? Do those and then move on to the next three and that's the bit I'd love to see the industry doing more of.
David Frise: Indeed, well we're trying to do that with yourselves and BESA. We've done some research recently about how well understood the Building Safety Act is and I guess not surprisingly it wasn't particularly well understood as you go further down the supply chain but the shocking detail to me was the lack of understanding of clients and many of them considered that it didn't apply to them because they weren't involved in HRBs and it led me to sort of say that actually it feels more like the Construction Safety Act, not the Building Safety Act.
Suzannah Nichol: Is that something you're seeing? I do believe there's a lot of confusion, there's a lot to take in and I come back to the theory about shifting a larger cog and some smaller cogs and I would say to people what is your role in this? What do you have to do? When we talk about the Building Safety Act it's a lot of legislation, you try and read through it and I'm used to reading legislation, I understand hopefully quite a bit of this and it hurts my brain just trying to understand what the requirements are, what that looks like, how do you deliver it? It is not easy and we've got an average reading age of 11 in our industry so why we think writing 90 page reports and giving them complicated legislation is going to change behaviour I've honestly got no idea. So I would say where do you sit? First of all the Building Safety Act applies to all buildings so just because you're not working on an HRB it applies to everybody, there are additional requirements for HRB so maybe that's the way to look at it. But look at what are the cogs that apply to you so within your specialist contractors are they demonstrating their organisational capability? Are they organised? Have they got the common assessment standard? Are they showing that to their clients? What occupations do they employ? Are those people trained? Have they got the right skills? Are they behaving appropriately out on site? What are the building regulations that apply to their bit of work? Are they bang up to date on those? Do they understand them? Are they delivering work in accordance with those building regulations and are they able to easily demonstrate to their clients this is our standard, this is what we do, this is how I'm meeting that standard whilst I'm out on site. And then sectors I think this is where trade bodies such as Visa really come into their own. You actually look across your members and say what are the common bits of information that we need to provide to our clients for their gateway two application, for the gateway three application and for the golden thread? How do we make that consistent across our members so they are providing the right information that is easily understandable? So not trying to understand the whole Building Safety Act would be a good start. What do I have to do differently and how am I doing that within my organisation? Because then you're doing your bit and if we add all that together you're then actually getting the Building Safety Act moving forward.
David Frise: Which is what we're trying to do with our Play It Safe campaign for example is to break it down into ‘so what is your role and how does it impact you?’ The critical thing is that 90% of us spend 90% of our time in a building so it really matters if buildings work and I think is a source of huge frustration to our members when they see the buildings don't necessarily work because it's been value engineered or bought on price. We've made a big play on competence and can you do the job and our technical audit is robust and we've actually suspended quite a few members over the last couple of years for their failure to attain that standard. But our members will say well it's not always being asked for, do you think that will change? And we've designed it so that for a client or a main contractor it fulfills their duty of care. You select a BESA member you have carried out your duty of caring, are they competent to do the job? Can they do it?
Suzannah Nichol: I would completely subscribe to that, I'm a complete advocate of, well I would be in my role, of that the role of the trade association and membership of that. And part of our future work is how do we help clients and contractors recognise and understand that value? Again I think sometimes we make it a bit complicated, we're working with BESA and a number of our other members to look at how we make that more consistent. So they understand what being a member of BESA is and they say that's a good thing, so if I've got the common assessment standard and membership of BESA and I know they may become one, we've actually gone a long way down our due diligence to ensure that company is competent. The simple question to a contractor or client is why would you use an organisation that's not a member of BESA? Because if you use the BESA member they've done a lot of the work for you, if you don't what are you doing to ensure they are competent? I suspect at some point there will be either a building safety regulator prosecution or case where they will say to a client you didn't assess and confirm the competence or the organisational capability of that organisation, I think that will wake a few people up. And it's not difficult for clients and contractors to do, we don't need to make it so complicated. So in the future for me that would be really simple, I'd love to stand on a platform and say why did you use a non-Build UK member?
David Frise: I have to talk a little bit about payment because so many of our members are involved, are spending too much of their time chasing money that's due to them and it's not a value-adding activity, it's a value-destroying activity, it robs them of their time and working capital. Where do you think we're going with that, is there some light at the end of the tunnel for our members?
Suzannah Nichol: We're heading in the right direction in construction, look the nature of business it is always going to be commercial. I cannot change an individual company's payment terms, your members have much more power in saying I'm not going to work for you because you don't pay me on time therefore I can't deliver and you're back to that. It sucks the productivity out of a project, it increases waste both in time and it's incredibly frustrating, why you would not pay for a service. The challenging construction is again it gets quite complicated with valuations, with sign-offs and again I think that comes down to your design work, sometimes we don't quite even know what we're meant to be constructing so how can somebody tell you whether you've constructed what you said you were going and you kind of end up in this loop. We achieve more with our benchmarking, that transparency and holding a mirror up to companies who would say to me oh but but Suze I pay on time. When we showed them their figures some went well where'd you get those from? Well your FD, you submitted them and they were quite surprised because I think they convinced themselves that their payment terms were good. There is a shift coming and again maybe digital systems will start to change this, you know there's no longer the cheques in the post, I think we still have cheques don't we? I think some people are still paid by cheques. But it's those cogs again, so government has committed to enforcing payment performance on its projects. Contractors will have to pay 95% of their invoices within 60 days or they won't get to work for the public sector. The light is now on government, that spotlight is on government, okay. Are you enforcing that? Who is working on your projects that is not complying with that requirement and what are you going to do about it? And our benchmarking has really helped. The conversations on payment 10 years ago were adversarial, it was a tit-for-tat, it was on the front page of the construction media. Now it's much less combative, it is much more about right we need to do something different or understanding and rolling behind it. And the metrics on retentions have come in. So from later this year you'll start to see companies having to report on how much retention they have withheld from them, but how much they are withholding from others. You'll start to see where the money sticks. And I come back to your members have a lot more power to their elbow than I think sometimes they realise. I know it's brave to say I'm not going to work for you, but at some point that is a business decision you make to work for somebody who is going to pay you or isn't going to pay you. And we make it easy because we show you exactly what their payment terms are.
David Frise: Just to make sure we've understood this, if we could just summarise. So you've been going 10 years, the ambition is to have not a single voice but have a co-ordinated voice for construction and that's beginning to work. You see progress in a number of areas, particularly around the competence assessment standard to reduce the costs of PQ. We're seeing open doors as a huge success and driving new entrants and kids into the industry by opening up the industry. Actually while you were speaking I was thinking, actually I've got to get my staff to go around here, my colleagues, because actually they would benefit from that massively. And on payment, a bit of light possibly at the end of the tunnel with change of government, there's something will hopefully come forth on that. Have I summarised, I think, have I missed anything out from that?
Suzannah Nichol: Well I, while you're saying that, I think the one thing I would really like to mention is the way the industry behaved during COVID. So exactly as you've talked about, more coordination, that's a really nice way of doing it. The industry stayed open working safely throughout COVID because we'd got the industry under one umbrella. We wrote the site operating procedures. I stood in front of the Prime Minister's advisor, well probably down the line to the Prime Minister's advisor, and said we're staying open, we're going to do it safely, we've got some site operating procedures, and they said can you get everybody to do it? And I said yes. I think I probably crossed everything I'd got when I said that. And the industry did it because they were all in the same place, they all needed the same outcome, and that demonstrated to me that the common objective is the same ultimately when you come down to it. But the industry, when the prize is big enough, can all work together and make a difference.
David Frise: I think everybody goes to site or starts a job with the view of delivering the best they can, and we kind of get in the way of helping them to deliver that. Final question, so what does the next 10 years hold for Build UK, and are you optimistic or pessimistic about the future? I think I know the answer.
Suzannah Nichol: Oh well I'm always optimistic David, you know that. There is still a lot to do, but it's moving in the right direction, and it is gathering pace, and under the current government they're clearly ambitious. You talk about, you know, homes and infrastructure at the heart of government. So that's a big win for the industry. We've taken a lot of time, but I think it demonstrates our efforts have, we're right at the heart of government. Talking to Treasury, talking to MHCLG, you know, they want this to work, they want more homes, they want more infrastructure. It's a long way from podium to project, so we've still got to deliver that. So there's huge opportunity. It is now up to the industry to stop the duplication, to say, do you know what, we can deliver this, but we've got to look at how we are going to do it, not how we used to do it.
David Frise: Suzannah Nichol, Chief Executive of Build UK, thank you very much for coming in today.
Suzannah Nichol: An absolute pleasure, thank you for having me.
David Frise: And now on to the podcast news. Visa Academy has introduced a fully online health, safety and environment test for managers and supervisors, providing a convenient and accessible way to meet skill card requirements. The 45 minute test is tailored to professionals in the HVCA world and can be taken remotely with secure online proctoring. It's a key step towards obtaining a gold or black skill card. The Visa Industry Awards 2025 are now open for entries and it's your time to shine. Whether you're an apprentice, engineer, employer or innovator, these awards celebrate the very best in building engineering services with categories recognising technical excellence, commitment to training and outstanding contributions to the industry. There's something for everyone. Don't miss the chance to showcase your achievements and gain recognition for you and your team. Enter now at theawardsthevisa.com and be part of the biggest celebration of the Visa calendar on the 16th of October at the Brewery London. And talking of which, this year's BESA Annual Conference will be focused on forward thinking. It'll be about innovation, sustainability and how to deliver a safer built environment for all. Stay ahead of the game, connect with like-minded peers, learn from live sessions and stay up to date with industry trends by securing your tickets today. There are a limited number of early bird tickets available so grab yours now on the Visa website. Thank you for tuning in to Behind the Built Environment. Don't forget to subscribe to our podcast for more in-depth conversations with industry leaders. If you enjoyed this episode please leave us a review and share with your colleagues. Stay connected with Visa with the latest updates and insights into our industry. And until next time, my name is David Frise and this has been Behind the Built Environment. Goodbye.
Episode 8: Behind London Property Alliance
In this episode of Behind the Built Environment, BESA Chief Executive David Frise speaks with Charles Begley, Chief Executive of the London Property Alliance, about the future of London’s built environment.
They discuss economic growth, sustainability, and the need for public-private partnerships. Charles highlights how flexible planning policies could generate £100 billion in additional GVA by 2045. The conversation explores skills shortages, the rise of retrofit projects, and the growing role of investors in sustainable development.
David Frise: Hello. I'm David Frise, Chief Executive of BESA. Welcome to Behind the Built Environment, the podcast where I delve into the major issues facing our industry through in-depth conversations with key industry leaders. Join us as we explore the trends, challenges, and innovations shaping the future of the built environment. Today our guest is Steven Boyd.
Steven Boyd: Good morning.
David: Good morning, Steven. Steven Boyd has worked in property and infrastructure for over 30 years, leading on major change programmes and on the management of complex national and international estates. As a former head of the British Army Estate and at one time responsible for Camp Bastion in Afghanistan, and a former Chief Executive of the Government Property Agency, he has a hands-on experience of asset management and the maintenance of complex and varied portfolios.
An engineer by training, he has a long-term commitment to improving efficiency in the built environment, especially through supply chain collaboration and using data to enable better and faster decisions. He now balances his time between non-executive, strategic advisory, and consultancy roles. Welcome, Steven, again.
Steven: Thank you.
David: Thank you for joining us today.
Steven: It's amazing what you can get with an internet scrape, isn't it?
David: Yes, indeed. Can we kick off, and we're going to come to the five short questions in a second, but can we kick off really? If you could tell us a bit about yourself and how you ended up joining the Army and specifically as an engineer?
Steven: Oh, joining the Army was a great thing to do, but it happened by accident. I went along to meet the interview guy and he said, ''What regiment do you want to join?'' I said, ''I've no idea. What regiments are there?'' He asked me what A-levels I was doing and sent me along to the Royal Artillery. I was interviewed by a very agey gentleman. I thought that's not for me. I then went along to meet the Royal Engineers and was late for my interview, but they took pity on me and took me to a pub for the interview, and I thought this is the job for me.
I've been in construction and property and facilities management since then.
David: It's a route you'd recommend for anybody?
Steven: Oh, absolutely. I love being in the Army. There comes a point where you get rather too old for it, but fantastic opportunities, some of the biggest projects, great work, and really enjoyable.
David: Some of the best friendships you'll ever make.
Steven: You have to rely on your colleagues, and your colleagues rely on you, and that camaraderie sticks.
David: Let's crack on with the five, or six, in this case, quickfire questions, which simply require a yes-no answer.
Steven: You're getting your value for money with six.
David: We are indeed. Does the current regulatory regime support the goal of delivering high-quality built environment for the long term?
Steven: No, not really.
David: Does the approach of government departments to the built environment hinder the delivery of culture change in construction?
Steven: In some cases, yes, I'm afraid it does.
David: Does the built environment sector have a suitably skilled workforce to meet its long-term challenges?
Steven: No, not yet.
David: Yes, no, remember? Is offsite the future of the sector?
Steven: Yes.
David: Does BIM work for the sector as a whole?
Steven: Not for the sector as a whole, no, it doesn't.
David: Thank you for that. We will get back to some of those questions in a minute. I'd like to start off with the Building Safety Act, if I may because we've recently done a survey that showed while there was an awareness of the Building Safety Act, and that's rising, it was widely ignored by industry's clients at the moment, particularly on the operational side. Many believe their responsibilities and risk can be delegated to others. Is that your experience? Do you believe that clients think this is the, shall we say, the Construction Safety Act or the Building Safety Act, and therefore doesn't apply to the lifecycle of a building?
Steven: Listen, the Building Safety Act is a good thing. I think it's a great step forward. There's perhaps more to do. When you introduce something new, it always takes a little while to settle. Building Safety Act, I think in this case, building means asset. This is about the safety of the asset, not the Construction Safety Act. You always get that slight confusion with that word. I think important that it's designers, constructors, in occupation and also refurbishment. Inevitably, it's the whole life of assets, particularly high-risk assets. That means that clients need to take it seriously. Of course, many do certainly. I know that clients in government are, but it will take a while to settle. There's probably some education there to be done.
David: I know we said I'd talk about the operational, and I'll come on to that in a minute because I think there's some interesting stuff there. Do you think the industry is growing increasingly frustrated by the amount of regulation, which it thinks is hindering its ability to, was it just get on with things? Gateway 2 is proving to be a huge bottleneck in particular. Do you think there is frustration growing across the sector?
Steven: I think there is a little bit of frustration. I'm not sure I'd say was growing. Industry is demonstrated pretty well that it couldn't manage itself and the government to give some guiding hand on how to do things better. That's the first thing to recognise. Then second thing, as I mentioned before, when something is new, there's always a little bit of resistance. I do think the Building Safety Act is a good thing. There is quite a lot of regulation, though, and I'm not sure that all of it is as aligned as it could be.
I'm not sure that the bodies responsible for assurance are necessarily as joined up as they could be. There is potential for confusion there. As the Act begins to work through and the Construction Products Regulator comes in too, I think there's an opportunity to try and be clearer about how the various bodies and the various regulation all works together so that you don't have people duplicating and doing wasted effort, but I think generally good direction of travel.
David: Do you think in, say, five years' time, we'll see a tangible difference? Or is it longer than that, do you think?
Steven: Oh, no, I think we will see a tangible difference but will that be the end of the journey? I doubt it.
David: Is there a danger that with such a heavy focus on safety and fire safety in particular, we end up designing and constructing buildings that are safe for fire, but not necessarily the best building for people's well-being and health? Ventilation being an obvious thing.
Steven: That's my point, in that you can find regulations about most of the important things about a building, and those have got to be joined up and brought together so that you get the best overall while still being safe. I think the Building Safety Regulator has a real opportunity to help with that.
David: One example of just around government and how they are managing the estate, the government has vowed to transform the NHS. Our healthcare infrastructure is crumbling. Maintenance budgets are not adequate at the moment. I think last week it was reported that the backlog on maintenance now exceeds the annual estate management budget and is growing. Surely the government needs to focus on fixing this if the system has any chance of meeting the commitments to patients and staff.
Steven: Yes, listen, that's a real concern, not just in the health sector, but also for prisons and lots of other asset types. I think all big clients struggle with capital projects on one hand and operations on the other and joining the two up, I think it's common for there to be different teams and different supply chains that supports new works and operations and maintenance. You might say that's the client's fault, but it isn't. It's more to do with that's the way the industry's set up. Clients have to respond in that way. That can mean left hand doesn't know what right hand's doing.
It should be possible to use lots of the good work that's been seen on capital projects over the last, say, 10 or 15 years, and carry that forward into operations and maintenance. There are various reasons why that is a challenge, but it's not an undoable thing. It should be a doable thing. Taking a whole life whole estate view about the health estate, for instance, could make a real difference. I personally think you could end up spending less money and getting a better result.
David: One of the areas you were focusing on though is that transition between construction and operation. Certainly, our members see this throughout the lack of commissioning, the complex way in which we hand over buildings and the data, and the clients not knowing what they need, so they ask for everything. The whole thing is a bit of a mess all the way through. Can you tell us a bit about the work you've been doing to try and improve that, particularly when you were at the Government Property Agency?
Steven: It is a little bit of a mess. When I first encountered different approaches in construction and facilities management 10 years plus ago, I was amazed that they were different. I said, ''Well, we'll just change this. We'll just sort it out. Why can't we do it? Oh, no, don't touch that, because it's just too difficult.'' That red rag to a bull. Made some good progress on that. Firstly, when I was with HMRC, and then more laterally with the Government Property Agency, to try and work with the various data classification and data standards groups to get some alignment.
The data that is generated during design and construction, which is generally pretty good, is not completely lost at handover. Whilst lots of that information is gathered, and there's lots of work done on handover, a few months after the handover, normally, a great deal of that has been lost, which is such a shame and such a waste of money, and means that having a genuine whole life perspective is really quite a challenge.
Breaking that glass ceiling is something that I'm passionate about. I think he's very doable. I hope that we can see some progress on that shortly because if you can do that, then that not only means that you're delivering more efficiently through the life of an asset, but it starts to address some of the problems you were talking about before where you've got a discontinuity between construction and operations.
If you can make that handover work smoothly, then that helps to bring the two together and you get a more joined-up view across the whole estate and all the money you're spending because currently there tend to be different buckets of you spending this on operations and this on capital works and government, like any organisation, capital works are sexy, aren't they? Big shiny new thing that looks good, whereas operation's not quite as attractive, say, but both of them are important and if you don't look after your assets through its life, which might be 30, 50 longer years, then that will come back to bite you.
Not just in a very big backlog maintenance bill, but also safety issues, wellbeing issues, health issues, general staff and employee, and patient satisfaction. That's not a sensible thing to do.
David: Do we need a new term other than maintenance? Because if you maintain something and it's working in the way it's always worked, which says, ''If I don't do it, it's still working, I've maintained it?''
Steven: Maintenance is important and I'm not sure I'd start running around trying to change the name there, but I don't think it's enough. You need a broader approach, looking at how the whole asset can be sustained over time and that includes replacing parts of the assets and upgrading parts of the assets from time to time on a life cycle basis and life cycle planning tends to be very weak, weaker than maintenance, and importantly today, not just is life cycle important, but taking those opportunities to upgrade facilities so they're more carbon efficient, carbon net zero interventions too, joining life cycle and carbon net zero interventions together. That's an increasingly important part of an asset's life.
David: We're filming this or recording this the day after Storm Bert has just gone through and paralysing much of the West Coast rail line or certainly from the West Country. It's a growing challenge of having to adopt our existing building stock so that it's actually able to cope with temperature fluctuations, flooding and increasingly air pollution. Is this, do you think, on building managers' radars?
Steven: It's definitely on building managers' radars and it's definitely on asset managers' radars. I think part of the challenge for them is this all sounds really difficult. Where should I start? Looks expensive. How could I do it? I think getting to a complete net zero building is really difficult, perhaps even impossible, but doing some things that will make a difference, you can start tomorrow reasonably low cost with short payback times. Getting started on the easy things, whether it's lighting or lighting controls, whether it's PV or insulation, those things are quite straightforward to do before you start getting sucked into the important challenges of removing fossil fuels from a building.
Then, as you point out, there's the challenge of the mitigation of the effects of climate change. It will be hotter. It will be wetter from time to time. What are you going to do about that? Adjusting the duty points on your cooling, for instance, choosing a better cooling system, shading your building, better insulation are all things that can be done from a temperature point of view. Then from a flood mitigation point of view, don't have a building in the flood plane. That would be a good start.
If you are in a place where it might flood, do you have to have all your important stuff on the ground floor? Maybe move the expensive things up a bit. If you do flood, you don't want to, but at least make the recovery from that as pain-free as it can possibly be.
David: We talked a little bit about BIM particularly, but digital construction tools in particular, how can they be used to help us develop and design and build better buildings than we currently do? What do you think is not happening that should happen in that area?
Steven: For me, it's about bringing together data. There's lots and lots of data collected, huge amounts of data collected in new construction, and probably even more collected in operations, but quite often it's in silos. Sometimes it's in proprietary software and it's difficult to bring together. Adopting an open and interoperable approach, bringing data together so that it can support decision-making. That's a technical challenge that's certainly very doable, but then there's also a leadership challenge of what do you want to achieve? What's important? What are your priorities?
Once it's clear what the desired outcomes are, then structuring that data so it can answer those questions, help you make decisions faster, better, so that you can spend less, emit less carbon, have more satisfied employees. All those things sound expensive. Actually, I think in lots of cases, it's really quite possible to do all of those things for less cost if you're making decisions on the basis of hard evidence rather than supposition.
David: Do you think, and we're going to link this to the Building Safety Act, so the problems at the moment of a bottleneck at Gateway 2, but do you think longer term that will help BIM in particular in that currently we very quickly migrate into build and design? Will this force us to go into design and build in a true sense, which would then open us up to more offsite?
Steven: It might help. I don't think it's necessarily a bad thing. We'll see what the workload looks like with everybody having to have their proposals checked. For me, going back to my particular passion, there's possibly more to do with when you're moving into operations. Do you then have the information necessary? I'm really pleased to see the whole life information management that's in the BSA, particularly their safety golden thread. I think it applies to everything. You gather the right information during design and construction, carry that through into operations, and use that to make the building more successful over its lifetime.
Importantly, when you refurbish things, that's got to modify and update things. I think there's not been enough focus on refurbishment in the past. I think that will change. A lot of the buildings, I think it's 80% of the buildings we have today will still be in use in 2050. That means there'll be quite a bit of refit and refurbishment between now and then. I think the industry needs to do more to move away from design and construction, full stop, new paragraph, operations. That needs to be more of a continuity and recognise that there are quite major projects and refurbishments that take place during the life of an asset.
There are lots of parts of the industry that could respond to that. One of my favourite ones is REBA. Their plan of work is great. Lots of people use it. Six stages during a new project, during capital construction, one stage during operations. Not even operations and refurbishment, not even two stages. Come on, guys. If you're listening out, REBA, let's have an additional stage, at least one more.
David: Good point. Just one point on offsite, which we mentioned at the very beginning, and there's been a lot of talk about and also some very high-profile failures in that area, mainly because of the cyclic nature of demand. Is it really the future of the built environment, do you think, and are there limitations?
Steven: I'd challenge the language a little bit. On-site, off-site is a little bit binary. I think we should have a little bit more of an assembly line mentality, thinking about how you start with raw materials and they get integrated to create products, and then those products are integrated to create components, and those-- You see my direction of travel. If you went back to the medieval times, raw materials came to site, they were all integrated on the site to produce a building.
The 20th century approaches, I think cathedral builders would recognise that still a lot of raw materials coming to site, some products coming to site where materials have been pre-integrated, but still a lot of work is done on-site. I think there will be more work done off-site, but not necessarily in a single off-site place. Multiple off-site places to create a assembly line where raw materials and products are iteratively integrated so that there is less raw materials coming to site, and perhaps that should be a challenge.
How little raw materials can you have coming to site so that you're bringing pre-integrated products and assemblies to site where they can be brought together? Putting things together in the pouring rain in November is not a good idea.
David: Things are becoming more and more complex to build and to maintain. We talked a bit about the skill sets required for that. What do you think the long-term-- particularly on the engineering services side, what do you think the skill sets that people will require to be able to-- Let's talk about the maintenance in the operation.
Steven: There's green skills to start with. I think there's a general need to understand better where carbon is embodied and where carbon is used, so I think that applies to the whole industry. I think if you look at operations, in particular, facilities management, asset management, then there is a big step-up required in digital skills. If you look at it in the round, somewhere behind where design and construction is, that needs to catch up, and that would be a big step towards having a more whole-life perspective. It's not that people in FMO operations don't want to do that. They do, but there's work to be done to help that, not just their education and training, but also the software platforms that support that area of the sector are not always suitable for taking a proper whole-life digital approach. Then there's also that glass ceiling I mentioned before which takes place at a practical completion which we need to smash through.
David: Do you see the fragmentation of the industry as a problem to getting that holistic approach to --
Steven: [crosstalk] Yes, for sure, the industry is fragmented, far too fragmented. I can't wave a magic wand over that. I was looking at some of the consultation that had been done to support the Building Safety Act and that's led to the creation of 13 sector-led groups, so those 13 different sectors, but the consultation also took place with over 60 professional institutions and associations. That just seems like an awful lot. I suppose my view is whilst some reduction in the number of different bodies will be good, that might not happen quickly, so I'm keen on more collaboration between those bodies where that's possible and I think there's lots of scope for that.
Then also my interest in data is the backdoor to that. If you can get everybody using an end-to-end data set, there's a single version of the truth, then that makes collaboration easy and the fact that the different organisations are fragmented is perhaps less important. It might lead to some more integration between those organisations, but that's from my point of view, not the main aim. It's getting the whole sector to be more productive. I think there's a lot of scope to be more productive.
David: That's a great segue into the work you've been doing recently around the FM Alliance. Could you tell us a little bit about what that work is and what your hopes are for it?
Steven: Yes, I don't want to go too far on that because the bodies involved have not agreed to anything at the moment, but they have demonstrated in a number of projects over years, ones that I've been responsible for and others, that the data can be better aligned and that when it is better-aligned everything works better. We've seen iterative improvements across a number of areas and now there's talk about could that way of working be formalised and people agree to collaborate in an extended way over time and that can only be a good thing.
Here we're talking about a genuine whole-life approach, so the data classifications and data standards that are used in design and construction and those that are used in operations lifecycle replacement and also whole-life carbon, if all of those things can be brought together with cost, what a lot of time would be saved, just wasted effort mapping and changing and recalculating and misunderstandings would be a lot less. Why not do that and I'm hopeful that those organisations will continue to work together and that we might achieve some agreement that say, look, we're going to sign up to working together in the long term. We'll keep working on that, and perhaps we'll achieve something. Watch this space.
David: Steven, you and I have both been through the transition from a military background into civilian. What struck you most when you came out? I think your last job was managing Camp Bastion.
Steven: No, my last job was I was head of the Army State-- Director of Infrastructure for the Army. The Camp Bastion thing keeps coming back, which was quite a long time ago now, but to be honest, I don't mind it coming back. That was just such a fantastic job. Go and build me a small town. How long have I got? Not very long. How much money have you got? How much do you need? Get on with it. That was a brilliant job, everything from obviously accommodation, headquarters and communications.
That goes without saying, but we built an international standard airfield, we built a heliport, two hospitals, all sorts of facilities. Water supply being the most challenging. Helmand is one of the driest places on earth and securing water from deep wells was a real challenge and one that fortunately for my future career came good.
David: A fascinating story. You came out of that where you tell people, you give them an order, effectively I think is a bit of a misnomer that people obey orders in the way that I think people perceive of the military, but you come out of that into the civilian world and you tell someone to do something and then you go, sorry you didn't do it? Why not? How did you adapt to that?
Steven: Yes, it's definitely, as you know, not as it's portrayed and I think people these days with-- there's comparatively few people serving in the forces gain their impression of what it might be like from Hollywood films which are not even a good representation of what happens in the US Army, never mind in the British Army and for us, as you know, it's, ''This is the thing I'd like you to do, not this is how I'm going to tell you how to do it, just go away and do it.''
If you take Camp Bastion for a moment and you might say that the Permanent Joint Headquarters doesn't have a lot of expertise in construction but even putting that to one side there are some great people in that organization, no one told me what to do, just go away and do it.
David: Yes, it's a popular misconception.
Steven: I will pass on the same thing to my team hopefully, yes, come back if you need a bit of help but go away and do it.
David: Final question, are you optimistic about the future or are you pessimistic about the future?
Steven: I am optimistic. I am definitely a glass-half-full person. I always think it's possible to do things that other people say maybe it's not. It might take a little bit longer than you would like but I am optimistic, yes.
David: This is an unfair question because I haven't prepared you for this at all but if you were able to do one thing that would make a difference, what would that be?
Steven: I'm on joining up the data. I'm on definitely joining up the data and then once you've done that, you can exploit that data and you can realize some real productivity benefits and we can do that quickly with the right will.
David: Steven Boyd, thank you once again for joining us today.
Steven: Thank you, David.
Episode 7: Behind Government Property
In this episode of Behind the Built Environment, BESA Chief Executive David Frise talks with Steven Boyd, a property and infrastructure expert with over 30 years’ experience, including leading roles with the Government Property Agency and the British Army.
They explore key challenges facing the built environment, from the implementation of the Building Safety Act to tackling fragmented data management and inefficiencies across construction and operations.
Steven shares insights on integrating lifecycle data to improve decision-making, reduce waste, and achieve sustainability goals, including net-zero carbon emissions.
He advocates for bridging the gap between construction and maintenance, emphasising the importance of digital tools and offsite assembly in driving innovation. The conversation also highlights opportunities to streamline regulations, enhance collaboration, and prioritise refurbishment for existing buildings.
David Frise: Hello. I'm David Frise, Chief Executive of BESA. Welcome to Behind the Built Environment, the podcast where I delve into the major issues facing our industry through in-depth conversations with key industry leaders. Join us as we explore the trends, challenges, and innovations shaping the future of the built environment. Today our guest is Steven Boyd.
Steven Boyd: Good morning.
David: Good morning, Steven. Steven Boyd has worked in property and infrastructure for over 30 years, leading on major change programmes and on the management of complex national and international estates. As a former head of the British Army Estate and at one time responsible for Camp Bastion in Afghanistan, and a former Chief Executive of the Government Property Agency, he has a hands-on experience of asset management and the maintenance of complex and varied portfolios.
An engineer by training, he has a long-term commitment to improving efficiency in the built environment, especially through supply chain collaboration and using data to enable better and faster decisions. He now balances his time between non-executive, strategic advisory, and consultancy roles. Welcome, Steven, again.
Steven: Thank you.
David: Thank you for joining us today.
Steven: It's amazing what you can get with an internet scrape, isn't it?
David: Yes, indeed. Can we kick off, and we're going to come to the five short questions in a second, but can we kick off really? If you could tell us a bit about yourself and how you ended up joining the Army and specifically as an engineer?
Steven: Oh, joining the Army was a great thing to do, but it happened by accident. I went along to meet the interview guy and he said, ''What regiment do you want to join?'' I said, ''I've no idea. What regiments are there?'' He asked me what A-levels I was doing and sent me along to the Royal Artillery. I was interviewed by a very agey gentleman. I thought that's not for me. I then went along to meet the Royal Engineers and was late for my interview, but they took pity on me and took me to a pub for the interview, and I thought this is the job for me.
I've been in construction and property and facilities management since then.
David: It's a route you'd recommend for anybody?
Steven: Oh, absolutely. I love being in the Army. There comes a point where you get rather too old for it, but fantastic opportunities, some of the biggest projects, great work, and really enjoyable.
David: Some of the best friendships you'll ever make.
Steven: You have to rely on your colleagues, and your colleagues rely on you, and that camaraderie sticks.
David: Let's crack on with the five, or six, in this case, quickfire questions, which simply require a yes-no answer.
Steven: You're getting your value for money with six.
David: We are indeed. Does the current regulatory regime support the goal of delivering high-quality built environment for the long term?
Steven: No, not really.
David: Does the approach of government departments to the built environment hinder the delivery of culture change in construction?
Steven: In some cases, yes, I'm afraid it does.
David: Does the built environment sector have a suitably skilled workforce to meet its long-term challenges?
Steven: No, not yet.
David: Yes, no, remember? Is offsite the future of the sector?
Steven: Yes.
David: Does BIM work for the sector as a whole?
Steven: Not for the sector as a whole, no, it doesn't.
David: Thank you for that. We will get back to some of those questions in a minute. I'd like to start off with the Building Safety Act, if I may because we've recently done a survey that showed while there was an awareness of the Building Safety Act, and that's rising, it was widely ignored by industry's clients at the moment, particularly on the operational side. Many believe their responsibilities and risk can be delegated to others. Is that your experience? Do you believe that clients think this is the, shall we say, the Construction Safety Act or the Building Safety Act, and therefore doesn't apply to the lifecycle of a building?
Steven: Listen, the Building Safety Act is a good thing. I think it's a great step forward. There's perhaps more to do. When you introduce something new, it always takes a little while to settle. Building Safety Act, I think in this case, building means asset. This is about the safety of the asset, not the Construction Safety Act. You always get that slight confusion with that word. I think important that it's designers, constructors, in occupation and also refurbishment. Inevitably, it's the whole life of assets, particularly high-risk assets. That means that clients need to take it seriously. Of course, many do certainly. I know that clients in government are, but it will take a while to settle. There's probably some education there to be done.
David: I know we said I'd talk about the operational, and I'll come on to that in a minute because I think there's some interesting stuff there. Do you think the industry is growing increasingly frustrated by the amount of regulation, which it thinks is hindering its ability to, was it just get on with things? Gateway 2 is proving to be a huge bottleneck in particular. Do you think there is frustration growing across the sector?
Steven: I think there is a little bit of frustration. I'm not sure I'd say was growing. Industry is demonstrated pretty well that it couldn't manage itself and the government to give some guiding hand on how to do things better. That's the first thing to recognise. Then second thing, as I mentioned before, when something is new, there's always a little bit of resistance. I do think the Building Safety Act is a good thing. There is quite a lot of regulation, though, and I'm not sure that all of it is as aligned as it could be.
I'm not sure that the bodies responsible for assurance are necessarily as joined up as they could be. There is potential for confusion there. As the Act begins to work through and the Construction Products Regulator comes in too, I think there's an opportunity to try and be clearer about how the various bodies and the various regulation all works together so that you don't have people duplicating and doing wasted effort, but I think generally good direction of travel.
David: Do you think in, say, five years' time, we'll see a tangible difference? Or is it longer than that, do you think?
Steven: Oh, no, I think we will see a tangible difference but will that be the end of the journey? I doubt it.
David: Is there a danger that with such a heavy focus on safety and fire safety in particular, we end up designing and constructing buildings that are safe for fire, but not necessarily the best building for people's well-being and health? Ventilation being an obvious thing.
Steven: That's my point, in that you can find regulations about most of the important things about a building, and those have got to be joined up and brought together so that you get the best overall while still being safe. I think the Building Safety Regulator has a real opportunity to help with that.
David: One example of just around government and how they are managing the estate, the government has vowed to transform the NHS. Our healthcare infrastructure is crumbling. Maintenance budgets are not adequate at the moment. I think last week it was reported that the backlog on maintenance now exceeds the annual estate management budget and is growing. Surely the government needs to focus on fixing this if the system has any chance of meeting the commitments to patients and staff.
Steven: Yes, listen, that's a real concern, not just in the health sector, but also for prisons and lots of other asset types. I think all big clients struggle with capital projects on one hand and operations on the other and joining the two up, I think it's common for there to be different teams and different supply chains that supports new works and operations and maintenance. You might say that's the client's fault, but it isn't. It's more to do with that's the way the industry's set up. Clients have to respond in that way. That can mean left hand doesn't know what right hand's doing.
It should be possible to use lots of the good work that's been seen on capital projects over the last, say, 10 or 15 years, and carry that forward into operations and maintenance. There are various reasons why that is a challenge, but it's not an undoable thing. It should be a doable thing. Taking a whole life whole estate view about the health estate, for instance, could make a real difference. I personally think you could end up spending less money and getting a better result.
David: One of the areas you were focusing on though is that transition between construction and operation. Certainly, our members see this throughout the lack of commissioning, the complex way in which we hand over buildings and the data, and the clients not knowing what they need, so they ask for everything. The whole thing is a bit of a mess all the way through. Can you tell us a bit about the work you've been doing to try and improve that, particularly when you were at the Government Property Agency?
Steven: It is a little bit of a mess. When I first encountered different approaches in construction and facilities management 10 years plus ago, I was amazed that they were different. I said, ''Well, we'll just change this. We'll just sort it out. Why can't we do it? Oh, no, don't touch that, because it's just too difficult.'' That red rag to a bull. Made some good progress on that. Firstly, when I was with HMRC, and then more laterally with the Government Property Agency, to try and work with the various data classification and data standards groups to get some alignment.
The data that is generated during design and construction, which is generally pretty good, is not completely lost at handover. Whilst lots of that information is gathered, and there's lots of work done on handover, a few months after the handover, normally, a great deal of that has been lost, which is such a shame and such a waste of money, and means that having a genuine whole life perspective is really quite a challenge.
Breaking that glass ceiling is something that I'm passionate about. I think he's very doable. I hope that we can see some progress on that shortly because if you can do that, then that not only means that you're delivering more efficiently through the life of an asset, but it starts to address some of the problems you were talking about before where you've got a discontinuity between construction and operations.
If you can make that handover work smoothly, then that helps to bring the two together and you get a more joined-up view across the whole estate and all the money you're spending because currently there tend to be different buckets of you spending this on operations and this on capital works and government, like any organisation, capital works are sexy, aren't they? Big shiny new thing that looks good, whereas operation's not quite as attractive, say, but both of them are important and if you don't look after your assets through its life, which might be 30, 50 longer years, then that will come back to bite you.
Not just in a very big backlog maintenance bill, but also safety issues, wellbeing issues, health issues, general staff and employee, and patient satisfaction. That's not a sensible thing to do.
David: Do we need a new term other than maintenance? Because if you maintain something and it's working in the way it's always worked, which says, ''If I don't do it, it's still working, I've maintained it?''
Steven: Maintenance is important and I'm not sure I'd start running around trying to change the name there, but I don't think it's enough. You need a broader approach, looking at how the whole asset can be sustained over time and that includes replacing parts of the assets and upgrading parts of the assets from time to time on a life cycle basis and life cycle planning tends to be very weak, weaker than maintenance, and importantly today, not just is life cycle important, but taking those opportunities to upgrade facilities so they're more carbon efficient, carbon net zero interventions too, joining life cycle and carbon net zero interventions together. That's an increasingly important part of an asset's life.
David: We're filming this or recording this the day after Storm Bert has just gone through and paralysing much of the West Coast rail line or certainly from the West Country. It's a growing challenge of having to adopt our existing building stock so that it's actually able to cope with temperature fluctuations, flooding and increasingly air pollution. Is this, do you think, on building managers' radars?
Steven: It's definitely on building managers' radars and it's definitely on asset managers' radars. I think part of the challenge for them is this all sounds really difficult. Where should I start? Looks expensive. How could I do it? I think getting to a complete net zero building is really difficult, perhaps even impossible, but doing some things that will make a difference, you can start tomorrow reasonably low cost with short payback times. Getting started on the easy things, whether it's lighting or lighting controls, whether it's PV or insulation, those things are quite straightforward to do before you start getting sucked into the important challenges of removing fossil fuels from a building.
Then, as you point out, there's the challenge of the mitigation of the effects of climate change. It will be hotter. It will be wetter from time to time. What are you going to do about that? Adjusting the duty points on your cooling, for instance, choosing a better cooling system, shading your building, better insulation are all things that can be done from a temperature point of view. Then from a flood mitigation point of view, don't have a building in the flood plane. That would be a good start.
If you are in a place where it might flood, do you have to have all your important stuff on the ground floor? Maybe move the expensive things up a bit. If you do flood, you don't want to, but at least make the recovery from that as pain-free as it can possibly be.
David: We talked a little bit about BIM particularly, but digital construction tools in particular, how can they be used to help us develop and design and build better buildings than we currently do? What do you think is not happening that should happen in that area?
Steven: For me, it's about bringing together data. There's lots and lots of data collected, huge amounts of data collected in new construction, and probably even more collected in operations, but quite often it's in silos. Sometimes it's in proprietary software and it's difficult to bring together. Adopting an open and interoperable approach, bringing data together so that it can support decision-making. That's a technical challenge that's certainly very doable, but then there's also a leadership challenge of what do you want to achieve? What's important? What are your priorities?
Once it's clear what the desired outcomes are, then structuring that data so it can answer those questions, help you make decisions faster, better, so that you can spend less, emit less carbon, have more satisfied employees. All those things sound expensive. Actually, I think in lots of cases, it's really quite possible to do all of those things for less cost if you're making decisions on the basis of hard evidence rather than supposition.
David: Do you think, and we're going to link this to the Building Safety Act, so the problems at the moment of a bottleneck at Gateway 2, but do you think longer term that will help BIM in particular in that currently we very quickly migrate into build and design? Will this force us to go into design and build in a true sense, which would then open us up to more offsite?
Steven: It might help. I don't think it's necessarily a bad thing. We'll see what the workload looks like with everybody having to have their proposals checked. For me, going back to my particular passion, there's possibly more to do with when you're moving into operations. Do you then have the information necessary? I'm really pleased to see the whole life information management that's in the BSA, particularly their safety golden thread. I think it applies to everything. You gather the right information during design and construction, carry that through into operations, and use that to make the building more successful over its lifetime.
Importantly, when you refurbish things, that's got to modify and update things. I think there's not been enough focus on refurbishment in the past. I think that will change. A lot of the buildings, I think it's 80% of the buildings we have today will still be in use in 2050. That means there'll be quite a bit of refit and refurbishment between now and then. I think the industry needs to do more to move away from design and construction, full stop, new paragraph, operations. That needs to be more of a continuity and recognise that there are quite major projects and refurbishments that take place during the life of an asset.
There are lots of parts of the industry that could respond to that. One of my favourite ones is REBA. Their plan of work is great. Lots of people use it. Six stages during a new project, during capital construction, one stage during operations. Not even operations and refurbishment, not even two stages. Come on, guys. If you're listening out, REBA, let's have an additional stage, at least one more.
David: Good point. Just one point on offsite, which we mentioned at the very beginning, and there's been a lot of talk about and also some very high-profile failures in that area, mainly because of the cyclic nature of demand. Is it really the future of the built environment, do you think, and are there limitations?
Steven: I'd challenge the language a little bit. On-site, off-site is a little bit binary. I think we should have a little bit more of an assembly line mentality, thinking about how you start with raw materials and they get integrated to create products, and then those products are integrated to create components, and those-- You see my direction of travel. If you went back to the medieval times, raw materials came to site, they were all integrated on the site to produce a building.
The 20th century approaches, I think cathedral builders would recognise that still a lot of raw materials coming to site, some products coming to site where materials have been pre-integrated, but still a lot of work is done on-site. I think there will be more work done off-site, but not necessarily in a single off-site place. Multiple off-site places to create a assembly line where raw materials and products are iteratively integrated so that there is less raw materials coming to site, and perhaps that should be a challenge.
How little raw materials can you have coming to site so that you're bringing pre-integrated products and assemblies to site where they can be brought together? Putting things together in the pouring rain in November is not a good idea.
David: Things are becoming more and more complex to build and to maintain. We talked a bit about the skill sets required for that. What do you think the long-term-- particularly on the engineering services side, what do you think the skill sets that people will require to be able to-- Let's talk about the maintenance in the operation.
Steven: There's green skills to start with. I think there's a general need to understand better where carbon is embodied and where carbon is used, so I think that applies to the whole industry. I think if you look at operations, in particular, facilities management, asset management, then there is a big step-up required in digital skills. If you look at it in the round, somewhere behind where design and construction is, that needs to catch up, and that would be a big step towards having a more whole-life perspective. It's not that people in FMO operations don't want to do that. They do, but there's work to be done to help that, not just their education and training, but also the software platforms that support that area of the sector are not always suitable for taking a proper whole-life digital approach. Then there's also that glass ceiling I mentioned before which takes place at a practical completion which we need to smash through.
David: Do you see the fragmentation of the industry as a problem to getting that holistic approach to --
Steven: [crosstalk] Yes, for sure, the industry is fragmented, far too fragmented. I can't wave a magic wand over that. I was looking at some of the consultation that had been done to support the Building Safety Act and that's led to the creation of 13 sector-led groups, so those 13 different sectors, but the consultation also took place with over 60 professional institutions and associations. That just seems like an awful lot. I suppose my view is whilst some reduction in the number of different bodies will be good, that might not happen quickly, so I'm keen on more collaboration between those bodies where that's possible and I think there's lots of scope for that.
Then also my interest in data is the backdoor to that. If you can get everybody using an end-to-end data set, there's a single version of the truth, then that makes collaboration easy and the fact that the different organisations are fragmented is perhaps less important. It might lead to some more integration between those organisations, but that's from my point of view, not the main aim. It's getting the whole sector to be more productive. I think there's a lot of scope to be more productive.
David: That's a great segue into the work you've been doing recently around the FM Alliance. Could you tell us a little bit about what that work is and what your hopes are for it?
Steven: Yes, I don't want to go too far on that because the bodies involved have not agreed to anything at the moment, but they have demonstrated in a number of projects over years, ones that I've been responsible for and others, that the data can be better aligned and that when it is better-aligned everything works better. We've seen iterative improvements across a number of areas and now there's talk about could that way of working be formalised and people agree to collaborate in an extended way over time and that can only be a good thing.
Here we're talking about a genuine whole-life approach, so the data classifications and data standards that are used in design and construction and those that are used in operations lifecycle replacement and also whole-life carbon, if all of those things can be brought together with cost, what a lot of time would be saved, just wasted effort mapping and changing and recalculating and misunderstandings would be a lot less. Why not do that and I'm hopeful that those organisations will continue to work together and that we might achieve some agreement that say, look, we're going to sign up to working together in the long term. We'll keep working on that, and perhaps we'll achieve something. Watch this space.
David: Steven, you and I have both been through the transition from a military background into civilian. What struck you most when you came out? I think your last job was managing Camp Bastion.
Steven: No, my last job was I was head of the Army State-- Director of Infrastructure for the Army. The Camp Bastion thing keeps coming back, which was quite a long time ago now, but to be honest, I don't mind it coming back. That was just such a fantastic job. Go and build me a small town. How long have I got? Not very long. How much money have you got? How much do you need? Get on with it. That was a brilliant job, everything from obviously accommodation, headquarters and communications.
That goes without saying, but we built an international standard airfield, we built a heliport, two hospitals, all sorts of facilities. Water supply being the most challenging. Helmand is one of the driest places on earth and securing water from deep wells was a real challenge and one that fortunately for my future career came good.
David: A fascinating story. You came out of that where you tell people, you give them an order, effectively I think is a bit of a misnomer that people obey orders in the way that I think people perceive of the military, but you come out of that into the civilian world and you tell someone to do something and then you go, sorry you didn't do it? Why not? How did you adapt to that?
Steven: Yes, it's definitely, as you know, not as it's portrayed and I think people these days with-- there's comparatively few people serving in the forces gain their impression of what it might be like from Hollywood films which are not even a good representation of what happens in the US Army, never mind in the British Army and for us, as you know, it's, ''This is the thing I'd like you to do, not this is how I'm going to tell you how to do it, just go away and do it.''
If you take Camp Bastion for a moment and you might say that the Permanent Joint Headquarters doesn't have a lot of expertise in construction but even putting that to one side there are some great people in that organization, no one told me what to do, just go away and do it.
David: Yes, it's a popular misconception.
Steven: I will pass on the same thing to my team hopefully, yes, come back if you need a bit of help but go away and do it.
David: Final question, are you optimistic about the future or are you pessimistic about the future?
Steven: I am optimistic. I am definitely a glass-half-full person. I always think it's possible to do things that other people say maybe it's not. It might take a little bit longer than you would like but I am optimistic, yes.
David: This is an unfair question because I haven't prepared you for this at all but if you were able to do one thing that would make a difference, what would that be?
Steven: I'm on joining up the data. I'm on definitely joining up the data and then once you've done that, you can exploit that data and you can realize some real productivity benefits and we can do that quickly with the right will.
David: Steven Boyd, thank you once again for joining us today.
Steven: Thank you, David.
Episode 6: Behind CIBSE
In this episode of "Behind the Built Environment," David Frise interviews Fiona Cousins, CIBSE president and Arup leader, discusses her engineering journey, emphasising the need for broader problem definitions in building services, beyond cost and efficiency, to include carbon reduction, biodiversity, and social value.
She highlights how evolving client demands for decarbonisation and carbon neutrality shape the industry. She stresses integrating safety, climate change, and societal impacts into design goals to prevent issues like those revealed by the Grenfell Report. She also advocates for better building operation and AI tools to optimise energy efficiency, emphasising whole-life value over short-term cost in creating sustainable, functional buildings.
David Frise: Hello, I'm David Frise, Chief Executive of BESA. Welcome to Behind the Built Environment, the podcast where I delve into the major issues facing our industry through in-depth conversations with key industry leaders. Join us as we explore the trends, challenges and innovations shaping the future of the built environment.
Today's guest is Fiona Cousins. Fiona Cousins is CIBSE president and holds a multiple roles at Arup, including America's Region Chair, Arup Group Board Member. She is also an Arup Fellow, a rare honour reserved for the group's most admired leaders. She previously served as Deputy Chair of Arup's Digital Executive and as Automation Leader, advancing digital transformation and sustainable development. A mechanical engineer by profession, Fiona has worked on many award-winning projects globally, including the U.S Embassy in London and Fulton Street Station in New York.
Under her leadership, Arup's America's Region, with over 2,000 members across 16 offices in the US, Canada and Colombia, strives to realise a sustainable and inclusive built environment by providing expert guidance to clients. Fiona has been recognised as one of the most influential leaders in the US commercial real estate industry and featured in the 2023 Commercial Observer Power 100 list. She is a valued advisor on critical climate legislation and was appointed to the New York City Advisory Board for Local Law 97 in 2019. She is a Lead Fellow and chaired the US Green Building Council in 2016. Welcome, Fiona.
Fiona Cousins: Thank you. It's good to be here.
David: Glad you could make it. You're here for two and a half weeks, you said?
Fiona: That's right.
David: We're very privileged to have you here today. We kick off with five quickfire questions. Try and do yes, no. It's not always as easy as it sounds, but I think you'll be all right with this. Is the building service industry too focused on energy efficiency and carbon reduction?
Fiona: Yes.
David: Should biodiversity loss be a consideration for building engineering projects?
Fiona: Yes.
David: Can building services firms meet their performance goals with their current skill sets and workforces?
Fiona: Probably not.
David: I'll take that as a no, then. Does government have a role to play in delivering culture change in construction?
Fiona: Yes.
David: Will all high-risk buildings be safer by the end of this decade?
Fiona: Maybe.
David: Yes, I thought that one. Are construction supply chains currently fit for purpose?
Fiona: No.
David: Fiona, first question. How do you end up here today? You're president of CIBSE, you're a fellow of Arup. What made you become an engineer and what was your journey?
Fiona: When I was at school, I think careers advice was terrible. The only jobs that any of us were really aware of were the jobs that our parents had, and that our friends' parents had. For me, that was doctor, lawyer, nurse, teacher, engineer, because my father was one. There wasn't really any advice about what would make you suitable for one career over another career at any given time. My introduction to engineering with the women into science and engineering activities that did come through when I was in the sixth form at school. Then I went to university to do engineering and it turned out that actually I was very interested in what it is. I was very interested in creating places and spaces that people lived in that form the backdrops to people's lives.
It went from there. I got a job with an employer that I've been with for very, very many years. I have always found that we think hard and work hard to try and make places and spaces, not just systems, although we also make the systems and the engineering work as well. It just turned out to be sort of an interesting place for me to be in. I always liked the idea that we were not only solving the detail of the problem that was in front of us, but we were also thinking about the bigger consequences of that. I would say that that's always been a theme in my career. It's like, how do we make this place beautiful, functional, useful at the same time as making it properly designed and engineered so that it actually functions?
I think that connection between the sort of the broader impact and the detail of the systems was very clear to me from a very early age. I've continued to draw the connections between the two pieces over the course of my career.
David: The influence of parents, as you say. I was fourth generation in the Navy, so it's difficult to dodge, as you say. You spoke about your father was an engineer. Was there one mentor who developed your career, helped you develop your career?
Fiona: Not really one. I think there were a number of people over time who were kind and generous in the way that they worked with me over time. There were a lot of people who helped me in my sort of pre-university year when I really didn't know anything to just expose me to different parts of the industry, and to sort of gain enthusiasm around it. After I graduated, I worked as a computer programmer actually in building thermal response. The person who looked after me there was also extremely kind and encouraging about the things that I should do. Sometime shortly after that, somebody said, yes, of course, you could be promoted to be a director at Arup, when I asked them if I could perhaps one day be an associate. The confidence that those people had in the possibility was just enough, I would say, to keep me going over time. I've had a series of very good mentors and sponsors over the course of my career.
David: Great. There's plenty to discuss there. Is it more challenging, do you think, for building engineering firms to make social inclusion, climate change, and health and well-being a focus for their business when the economic situation is challenging?
Fiona: I think the answer to that is, yes, of course. I think that the second part of that is how we account for the things that we pay for, and how the building industry costs work. I think that one of the things that as a mechanical engineer I've always been challenged with is, that the first question out of anybody's mouth when you say I'd like to buy a better chiller is, "And how much will that cost me and what's the payback?" When actually the answer is not necessarily in how much will it cost me and what's the payback? It might be about and how will that reduce my carbon emissions and how will that improve the operations of the building? Is a chiller even the right thing to buy? Are actually the questions that people should be asking. The conversation very quickly revolves around costs. I don't think that that's necessarily always very constructive.
David: In the report that you wrote, the forward to that CIBSE produce excellent building performance reimagined. How should we be reimagining engineering services?
Fiona: I think that one of the issues with building services engineering, is that we spend a lot of time solving the problem that we defined for ourselves, really quite a long time ago. We solve the problem of how do we provide a comfortable environment that is cost effective, maybe energy efficient, maybe carbon efficient, and that the owner can afford. It's a fairly straightforward question to answer. Actually, over my career, and I think, probably over yours, what good looks like has actually changed quite a lot. If we look back five or six or seven years, none of our clients were asking for decarbonisation. Now all our clients are asking for decarbonisation.
If we look back 25 years, nobody was even really asking for energy efficiency and now people have asked for energy efficiency. Now they're more interested in carbon, as the electrical grid begins to decarbonise, energy efficiency is perhaps becoming less important, because people have been focused on carbon, embodied carbon, embodied energy are beginning to become more important. We've been working in a changing context for a really long time. I think that means we have to think really hard about what the question we're asking ourselves is as engineers.
Engineers are brilliant at solving the problem once the problem is defined. I think that what we actually need is a different problem definition, something that is a little bit broader, that takes account of more social, or more biodiversity criteria. That more directly addresses some of the carbon and climate change problems that we're aiming at.
David: I think from our members perspective, as contractors who come in, with a consultant led design, by and large, every project starts off with fantastic ambition. A lot of time and energy is spent on designing a building the client then works out they can't afford, or a quantity sphere says that. Then suddenly you get into value engineering. How do you stop that process when you still have this purpose, these ambitions?
Fiona: I think this is sort of back to that question of cost driving everything. The best projects that I've worked on have been projects where right at the beginning, the design goals have been set, so that they're not just something that I can afford. That it's something that I can afford that is also carbon neutral, or that also delivers a certain programmatic requirement, or that was also restorative for the natural environment. If you can bake those things in at the beginning of the project, the very, very beginning of design and say, actually, this project will be successful if, and it's more than just on time and on budget. Then those things begin to permeate all the way through. Then it becomes much more difficult to unravel some of the individual pieces.
The value engineering works by attacking the line items that look like they're costing more than they otherwise might. If everything is actually more fully integrated, that the reason you've got a heat pump is because you want to have a fully electric building, because actually you want to be zero net carbon over a period of time. You've got a very different set of criteria, you're not going to suddenly say, well, the heat pump is more expensive than the chiller would have been or whatever it is. This is a little bit of an old-fashioned example, given that nobody is putting boilers in anymore, but this idea that you can't strike out the line item on the basis of cost, if actually it's fundamental to other things that you have deemed as success points for the building.
David: In your forward to, the report, you point out that 90% of us spend 90% of our time in a building, so the buildings and the built environment is really important. I think we were talking about whole-life cost maybe, or short-term cost versus whole-life cost, but should we be really looking at whole-life value that that building brings to society?
Fiona: Yes, I think that whole-life value is probably the right way to look at it, and it's not just about value in terms of cost, as you say, it might be value in terms of what's the contribution to society in a broader way. Is it about carbon emissions? Is it about biodiversity? Is it about places that the community can gather at? Is it about buildings that face outwards and improve security on the street rather than face inwards and don't have any eyes on the street? Is it about buildings that have different purposes at different times of day, because that's one of the ways of getting the most value out of our real estate? Those kinds of questions, I think, are the questions that we need to begin to ask ourselves.
David: In the UK in particular, and I'll ask you about the US later. The Grenfell Report was published a few weeks ago, which is a damning indictment of the culture of the industry. How do that being integrated into this picture of a better built environment, but a safer one? Is there a danger we make buildings safe in the short term from fire, but actually in health terms probably less safe by sealing them up and not properly ventilating?
Fiona: I think that some of the things that we discovered in the Grenfell Report were about not taking the broader view. To your earlier question about cost, the costs were driven down, and they were driven down in the most effective way that they could be, and as quickly and as hard as they could be. The people involved have been shown to have taken their eye off the overall safety ball. They weren't perhaps as aware of the outside environment as they should have been. I think that this piece about what is the bigger problem that we're trying to solve? Where is the value? The value is in safe buildings. It's not in unsafe buildings. The value is in doing things right and doing things right the first time.
Some of those broader criteria, whether it's safety or climate change or society, are all about not solving just the problem that's in front of you. How do I design the cheapest façade system that I can put on the outside of a building and install it as quickly as possible? But how do I make a safe building that contributes to climate change mitigation that is safe in times of climate change adaptation that perhaps supports biodiversity? These bigger picture things need to be integrated into the design problem that our engineers and contractors are trying to solve, because if they're not, you end up with these other kinds of disasters.
It's not about a particular thing that you do. It's about a general awareness that permeates everything that you do. It's like, is this the right decision? Am I solving the right problem? I think we are not always very good at lifting our eyes to the horizon and thinking about it. We think about what's the problem I've been asked to solve? How do I do this thing at the lowest possible cost? If that's the problem you're trying to solve, you aren't going to get the very, very best answer.
David: We're very project-based, and we dig ourselves holes, get ourselves out of it, and then call that innovation by and large. You're based in the US now. What differences do there from the UK in the way services are delivered?
Fiona: The US is a very big place, and I think that there are some things that we see around regulation. The regulation is very variable, depending on which part of the country you're in, and actually even sometimes which city you're in. Some places like New York City have things like Local Law 97, which is a carbon emissions regulation that applies to all buildings retroactively. Whereas most of the country has building codes that only apply when you're building new or perhaps when you're renovating buildings equipment. There's huge variability within the United States itself, and I think that in the UK it's a little bit more uniform, but I think that there are still moves that could be started.
The building regulations largely apply to new buildings. There are some regulations that apply to buildings after they have already been built. Some of the European introduced legislation about reporting building energy use, putting energy certificates into buildings. Those kinds of things begin to sort of approach what happens after the building is complete, but not necessarily quite to the extent that New York City has gone to. Which is we'll fine you if you emit too much carbon, and we don't care that you're a brand new building, a really old building, that you've had a boiler for this long. It's a very different kind of view.
David: You were talking about in New York they fine you if you don't meet the targets. Is that something we should do? There's such a lack of enforcement in the UK that it's pretty much laissez-faire. As long as it looks like the thing you put in for planning, you're golden, so to speak. Whereas, we all know there are buildings that are nowhere near their energy performance targets and therefore their carbon targets.
Fiona: I'm not sure whether you should or should not fine people. As New York City always says, we don't really want your money, we want you to have a well-performing building. What we actually want to do is carbon emissions reductions, and so there's actually quite a lot of support built into the New York City regulations and rules about how you transition to become the building that does emit at the level that we want you to emit. It is somewhat revolutionary to begin to look at buildings that already exist and to put fines and price on non-compliance, but I think with every policy question, it's always what is it that you are actually trying to regulate? What is it you're trying to achieve? What is the most direct way there? Then what is the most politically possible way there? How do you get those things to line up?
David: Can we move on to climate change mitigation? We're at the sharp end of, I think, something that when I was a child would never have dreamt of, which is overheating in buildings. They were always massively underheated, is my recollection anyway. How are we going to deal with overheating, massive amounts of rainfall, but also water scarcity and air pollution in the future? What's our role in this?
Fiona: This is a slightly complicated question for me because I live in the US where actually overheating has been a problem for years, and most buildings, certainly in the south of the country are air-conditioned and have been, and that includes residential. The question becomes less about if you want a building to be cooler in the summer, then you air-condition it. There are ways of doing that, and as we move towards putting heat pumps in for heating, actually you put in a reversible heat pump and suddenly you've got cooling as well. There are ways of dealing with residential overheating, and many of the bigger commercial buildings are already air-conditioned or comfort-cooled because they have to be. There is definitely a change in the way in which we use buildings and a change in the way that buildings are operated.
One of the things that you can also learn if you live in a place that is regularly warm, is you can learn to keep your buildings cooler. There are many things that you can do sort of passively to make sure that your building doesn't overheat. I live in a non-air-conditioned apartment in New York City, and we always close the blinds before we leave in the morning. We always close the windows before we leave in the morning if we know that the temperature is going to be in the high 30s over the course of the day, because actually when we come back in the evening, it's then still more or less as it was when we left it in the morning and you can perhaps cool it off overnight.
I think there are some things that we can do in residential buildings that allow us to deal with overheating by operating the buildings better without necessarily providing air conditioning. It's an enormous sort of public awareness education campaign in order to be able to make that happen. More difficult in commercial buildings, because part of the problem is the internal heat gains, but there are still things that you can do by way of shading, controlling solar gain. All of the things that you would worry about if you wanted to overheat a building.
I'm aware I haven't really answered your question because your question was sort of everywhere, but if you are looking for climate change mitigation, the point is to do all of that in as low a carbon way as possible. What is the right thing to do? Is it to put in air conditioning? Perhaps. Is it to operate that air conditioning with your lovely new, clean, shiny carbon free grid? Maybe that's the right approach. Maybe a better approach is insulation, shading devices, building control, and so on and so forth. I haven't done the math, but the math needs to be done.
David: I think that's the most polite way someone said that was a rubbish question [laughs]. It brings up another point about operation of the building. We have a heavy focus on design and installation of the initial system where we save £25 here and £50 here, and the long term cost is much, much greater than that. Should we focus more on facilities management and how we actually operate the buildings to get the maximum benefit of the systems that we design and install?
Fiona: I think the answer to that is clearly yes. We have actually tools to do that we didn't used to have. When I was first working, perhaps when you were first working, it was the back end of pneumatic controls and you could just about manage to have a few on off switches in various places around the building. Things got better through DDC, and then they got better again. Now everybody's got web based controls, and sensors have become much less expensive because many of them can be wireless and self-powered, and so you need to run less wire. The whole thing has become much less expensive to control and manage.
There are definitely better tools now than there used to be to be able to keep control over what your building does and how it does it. There is a difficult part here, right? When you are designing a building, you build the very best energy model that you can to understand how the thing is going to work. You build into it all sorts of things about how you think the building will respond thermally, how the piece of equipment will be operated, what the partial load characteristics of that thing are, and whatever it is.
It's an enormously complicated model to build, and so we know that the energy models that we provide during design are approximate at best. Then we know that the contractor will install something slightly different. They'll buy a different piece of equipment, or the manufacturer will change the specification or something else, so whatever the energy model was, it won't reflect what is actually built. One of the things that I think we have seen a lot of in the last few years is instead of trying to build up an energy model from the bottom, system by system. Actually with the cheapness of the sensors and other things, what you're able to do is you're able to say, under these conditions with this many people inside it and using these kinds of characteristics, this is how my building is operating, and this is how much energy it's using.
Then people are beginning to use AI and other methods to say, okay, so how do I make this more efficient? If you let the AI do it, then actually you can get to a better place, perhaps from an operational standpoint. I think that it was always tricky. We know that 20% of people in buildings are always uncomfortable, that's what Fanger told us, and we still know that to be true. Somebody will always be uncomfortable, so somebody can always go and adjust something to make the person who's sitting in seat 11B a little bit more comfortable because they tend to run hot or they tend to run cold. Actually, what that does is it tends to put the systems more and more and more out of kilter over time and operate less and less as they were designed to.
I think with the AI tools, you can begin to get to a point where the buildings can be more readily optimised, but you've only got the data that you have from that building in order to build that AI. If it's a poorly operated building, you may still never get to the sweet spot. There's a thing that I think bears thinking about around what's the role of a bottom-up model compared to a AI data gathering model, and is there a point at which those two meet so that you get really good building operations? Then having decided that that's what really good building operations looks like, how do you then make sure that the people who are actually operating the building have the tools that they need to make sure that it stays in tune over time?
David: Skills, how do our skills developing? What areas should we be looking at to develop our skills so we can deliver these buildings with AI and other new technologies that are coming in?
Fiona: I think there's certainly some idea that we need to be more facile with data and digital understanding and have a little bit more conceptual understanding of how we might be able to get these buildings to work. I think that there is a piece that we can also build in. What is the thermal response of buildings? This question about how do you stop buildings overheat in the first place. That's a thermal response question, and it depends very much on the building. Is it high mass? Is it low mass? Has it got low mass finishes on high mass? What are we looking at? How does the building actually respond?
There are skills around digital, there are skills around understanding how a building might react to thermal stimuli of various kinds. There are skills around, well, what's the system here and how does this actually work? Then there are skills about what's the equipment and how do I actually make the equipment work? The role of an operating building engineer actually has to cover quite a lot of ground. I think there's been a tendency to emphasise the skills that are to do with keeping the piece of the machinery running as opposed to keeping the whole of the building running and optimised. It's a much broader skill set that I think is generally hired for.
David: I think contracts generally say keep the thing running rather than optimising performance as well.
Fiona: Right. Which brings you back to this question about keeping the thing running is the thing that is valued, that's the performance that is valued. Actually, it could be that what is really valued by society as a whole, and perhaps this is where the carbon taxation comes in. Keep the thing running and avoid my carbon fines would be a better criterion to be solving for. In other words, you need to change the problem statement.
David: One of the things we discussed before we came in over a coffee was diversity in the industry and the lack of diversity. It's a two part question. Firstly, how do we deal with that? How do we get less people looking like me in the industry? Is there a difference between here in the US in how they're dealing with that?
Fiona: Yes, the problem with the questions about the US and the UK is that I've worked almost my entire adult life within the US. I'm much more familiar with how things work there and the way that the industry is and the way that people interact than I am here. Obviously, I work for an international company, so I hear both ends of the story, but my experience is pretty much all American. I think things have changed enormously over my career. My first experience of a building site was a Women Into Science and Engineering trip to go and see the Elizabeth Conference Centre opposite Westminster Abbey when it was under construction. I remember walking in and thinking, oh, my goodness, this is what building sites smell like. It's that smell of fresh concrete that people who go to building sites are very familiar with.
I loved that visit. I sort of became an engineer partly as a result of that, and partly because I had very good experiences in my pre-university trainee year working at Arup. It was just a really exciting experience to be amongst adults who were trying to do something, trying to build beautiful things that functioned. It was a really inspirational year from my point of view. Even though I found that environment extremely welcoming when I left university and joined, I was 1 of 10% of women in my graduating class. I was probably 1 of 20% of graduates as a woman going into the company. By the time I was 26, I was the oldest woman in the room and I have been the oldest woman in the room pretty much consistently ever since, because I think things have got better.
I think that for the women who were a little older than me, it was a very unwelcoming environment. Society was different. Things became problematic when they wanted to do some time at home and some time at work. Sort of the idea that you become a very busy person in your in your 30s was less well understood and less well catered for by the working environment. It is definitely better now. The environment is also more welcoming. When I first went to work, there were page three girls all over the office and now there are not. There's a sort of a piece about respect that came in very quickly. 30 something years ago at this point.
The industry has become more welcoming, but there is still a question about you tend to have to prove your competence a little bit more often and a little bit more clearly if you come in from a minority standpoint. Certainly as a woman in engineering, it's like, what do you know. As you get older, you have more wrinkles, more grey hair, there's fewer of those questions, because you tend to not just be the oldest woman in the room, you become the oldest person in the room and people are a little bit more respectful of that length of experience. It has become better for me personally as I've got older, but I think it has also become better for the younger women.
I think that the issues that arise for the ethnic and racial minorities are similar. There's a sort of tendency to judge on stereotype and a need to prove and prove again a sense that, you might be the diversity hire and therefore there's not room for another one when actually that may or may not be the case. It's always like, well, you can get a woman promoted, but could you get two? You can get a Black person promoted, but can you get two? It's a sort of second question. There's a little bit where I think we see it and then we wonder if actually it's possible for that next person to come in or whether people feel that they've met their diversity targets. This proving again and proving again, I think becomes perhaps the biggest barrier for minorities of all sorts.
David: Within the industry, you're in your role as president of CIBSE. How can CIBSE and BESA, representing the contractors, what can they do together to improve the industry?
Fiona: I think there are lots of things that we can do as engineers to improve the industry. When we were talking over coffee, we were talking about how much of what we do, the very, very best that we can expect is it disappears into the background and nobody notices it. I think that the problem with-- That's clearly something to aim for. We definitely don't want people to be thinking about their heating systems all the time. We want them to be thinking about living their best lives while they're in the buildings that we have constructed and designed.
We do need people to understand a little bit more about what it is that enables them to live their best lives while they're sitting in buildings. A little bit more value needs to be attached to good buildings, things that keep you comfortable. Things that provide the environment for you to do the thing that you want to do. Things that mitigate climate change. Things that allow you to be healthy and well. All of those things I think are in the remit of the building services engineers and the building services contractors. Is the building properly ventilated? Is that ventilation safe? Is it comfortable? All of those things are things that we should value, but we've spent an awful lot of our time in the past trying to make them disappear.
There's a question about how does the industry make sure that the things that we provide are valued without necessarily making it so that you notice your heating system every time you walk into the building. What are the things that we need to do in order to be able to change how people think about and view the infrastructure that they rely on all the time. I think that the answers are things to do with advocacy, they're to do with scientific literacy, they're to do with demonstrating and showing what it is that we do over time and in different environments.
Fiona: Final question, and that is are you optimistic about the future or pessimistic?
Fiona: I think that it's necessary to be optimistic. I think that there is an enormous amount of work that we can do if we have hope. People will say things like hope is not a strategy, but actually I think hope is a strategy, because hope is only really hopeful if you back it up with action and with doing things. I think you have to be optimistic about the possibility of change, you have to have hope that you can change things, that you have some agency. Then you have to figure out what it is that makes that hope real.
David: What a great answer. If I can just summarise what we've discussed today, the engineering services are very important to everybody's lives, we all live in the built environment, spend 90% of our time there. Actually, what building engineering services, engineers and contractors do, makes a big difference to people's lives. Most of the time they're really unaware of what has happened, they only value it when it doesn't work.
We need to sharpen up our skill sets to take into account technological developments such as AI and new technical developments in equipment. We need to make buildings safe, but not at the expense of buildings that work. We don't want to create long-term health issues by sealing buildings but not properly ventilating them for example. We need to start to look at how we make the industry more diverse, and not simply to hit targets, but actually you get better results, people think differently from different cultures and they add to the overall picture. I hope that sort of summarises what we've discussed today.
Fiona: Yes, I think that sums it up.
David: Great. Fiona Cousins, thank you very much.
Fiona: Thank you.
Episode 5: Behind Water Management
In this episode of "Behind the Built Environment," David Frise interviews Dr. Jo Jolly, Director of Environment and Innovation at Ofwat. Jo discusses her journey from geophysics and hydrogeology to her current role, emphasizing her commitment to achieving the best outcomes for the environment and society. She highlights the urgent need to transform infrastructure performance using data analytics and innovative approaches.
Jo advocates for proactive collaboration between water specialists and building engineers to enhance water management and HVAC systems, improving water and energy efficiency. She also discusses the importance of using data to measure and improve project performance, stressing psychological safety within teams to encourage transparency and prevent issues from being overlooked.
David Frise: Hello, my name is David Frise, and this is Behind the Built Environment, the podcast from BESA, the podcast where I delve into major issues facing our industry through in-depth conversations with key industry leaders. Join us as we explore the trends, challenges, and innovations shaping the future of the built environment. Our guest today is Dr Jo Jolly from Ofwat. Welcome, Jo.
Jo Jolly: Hi, David. Thank you.
David: Jo joined Ofwat in August as their Director for Environment and Innovation. Prior to joining Ofwat, Jo was Head of Project Futures at the Infrastructure and Projects Authority in Cabinet Office. Leading the implementation of the Transforming Infrastructure Performance Program, and with over 20 years in project delivery, including the successful delivery of the Environment Agency's $2.6 billion Flood Risk Management Program, she understands firsthand the problems and opportunities we have in delivering better outcomes through all that we do.
She believes we urgently need to transform our approach in order to achieve the best outcomes for the economy, the environment and society as a whole. Jo is pioneering the use of data analytics in this transformation, including as a founder member of the Project Data Analytics Task Force. As I said, welcome, Jo. Thank you for joining us today. We always like to kick off with some quick-fire questions because it sets the agenda. You've got to try and do yes-no to these, okay?
Jo: Oh, that's quite hard for me. [laughs]
David: Quite hard for everybody. Number one, can better collaboration between water specialists and building engineers lead to improved water management for more efficient HVCA cooling and heating systems?
Jo: Yes, wholeheartedly.
David: Would integrating water-saving technologies in HVAC design improve both water and energy efficiency in building operations?
Jo: Yes.
David: Is regular communication between water specialists and building engineers essential for ensuring a reliable water supply for all uses, including emergency uses such as fire suppressants?
Jo: Hugely, yes.
David: Is there a role for innovation in data analytics and novel technologies to enhance HVAC system performance?
Jo: Yes, I'd love to explore it. [chuckles]
David: Great, we will. Would co-developing maintenance protocols between water specialists and building engineers help to improve the effectiveness and efficiency of these water systems?
Jo: Yes.
David: A note to our editorial team here, we need some no answers in here, otherwise, it's too easy.
[laughter]
Jo: They're great ideas running through all of that, David, aren't they?
David: They are. They are great ideas, and let's explore them. First, it's always interesting to know how you ended up here today. How did you end up? Why did you choose this industry at whatever age you came into it? What started you off on the sort of engineering path?
Jo: Interesting. I don't think I've ever had a grand plan in mind. Growing up, I certainly cared massively about the environment, growing up in the '80s. I think it was very-- the awareness of climate change, the impacts of it was very much around me then. Actually, I didn't study engineering. I studied geophysics at university, and I went to Liverpool because I loved the Beatles. What better reason?
I suppose I've followed my nose, and you could say my heart, throughout my life and been incredibly fortunate to be able to do that. I think coming back to that, how fortunate we are and what we do with that is a theme I want to bring out during this discussion as well. I studied geophysics and then hydrogeology as an MSc and eventually a PhD, and then thought I ought to get a proper job and worked as a consultant in groundwater and contaminated land.
Then I joined the Environment Agency, and I sort of moved into project delivery and particularly delivering the flood risk capital programme. A lot of infrastructure, construction and design. I think just over my lifetime, I've become, in my working life so far, hopefully, a few more years to go, become increasingly clear about sort of what's my purpose. What's my purpose in leadership? What's my purpose in life?
I've got to an age where I don't really care if that sounds cheesy anymore because I think if you're really clear on your purpose, then that's your driving force. That's what gets you through your hardest days. That's what puts a spring in your step. It does for me. It became very clear to me that a life well lived for me, David, will be that I've done the best I can through the work I do for the planet before I die. That's it. It's pretty simple, pretty clear.
There's quite a lot in that, what is the best we can do? My yardstick for that is Sir David King. I had the absolute privilege to be invited to a close meeting with him two or three years ago now. He talked about not only, as we all know, must reduce greenhouse gas emissions dramatically and draw them out of the atmosphere at scale, it's not enough. Certain climatic systems that we depend on for life on this planet have gone beyond a tipping point.
One of the ones he talks about was the Arctic. He whatever we do with greenhouse gas emissions, whatever we do, more ice in the Arctic now melts in the summer than can ever refreeze in the winter due to the shrinking ice, reducing reflection of the heat, more absorption of the sun's heat by darker water. That's gone into a feedback loop. Whatever happens, we're set on that path. I'm afraid that's pretty catastrophic. We're locked into a very different climatic future right now.
What David King chose to do, nobody told him to do this, he has established the Centre for Climate Repair, because what he's saying is we need to repair damaged climatic systems. He's established a Centre for Climate Repair with engineers at Cambridge University, and they're developing technologies to refreeze the Arctic using marine cloud brightening technologies. That's my favourite project in the whole world, because if that doesn't succeed, like I say, we're not on a good path.
That's what doing your best looks like, David, to me. Obviously, on a daily basis, I'm failing miserably. It's good to strive, isn't it? It's really good to strive and to think, "Yes, well, what could I do? What could I do today? What's in my gift through the choices I make in this privileged, fortunate position I'm in? What's the best I can do?" That's why I'm here.
I feel extraordinarily fortunate to be in an organisation like Ofwat, well, specifically Ofwat, because the organisation you're in really decides to a large degree what and how much you can achieve. To be in an organisation that is kind, empowering, trusting, bold and full of humility about how we can do things better, I can't imagine a more nourishing and enabling and ambitious environment to be a part of. That's why I feel extraordinarily privileged to be here. I will promise to do my best.
David: That's a fantastic answer. From a fairly serendipitous, you went to Liverpool because of the Beatles, through to your purpose, which I think you've perfectly described. I think purpose is something that, particularly for the younger generations, is something that's really important. When we set out in BESA, that our purpose was actually a better industry, because you get a better built environment that has huge social benefit, and also helps mitigate the climate crisis to a degree. That has helped us attract some really good talent, younger talent, because they believe in the purpose. That's really encouraging to hear that. It's very encouraging to hear that within our regulators, we have people who genuinely care, and you can't hide that, as they say.
Jo: Could I just comment on that, David?
David: Yes, of course.
Jo: I absolutely agree that younger generations who are coming through absolutely have climate and nature and a purpose pretty much at the top of their agenda. I think the thing you and I, and others like us really have to recognise is our last best years for doing anything to mitigate the impacts of climate change is now, is the next year in front of us, and the next year in front of that.
We're the ones in position of influence, we're the ones in position of power. Whilst the younger generation do care deeply, it's us that have to do the action, because we're here now, together with our younger colleagues, of course. I think I often hear, "Oh, it's the younger generation coming through." I think, yes, but it's us, it's here now.
David: It's easier to give it to them to deal with, then we don't have to worry about it, isn't it?
Jo: Perhaps.
David: Yes. A few questions now. Off-way shifting to be an activist regulator, how do you see that working? How can this further enable effective relationships between regulators and the wide industry and the supply chain?
Jo: Yes, I love this term, activist regulator. The person who really brought the meaning and how we live activism to life is a lady called Carmel McConnell. Incredible lady. She spoke at the Association for Project Management conference a year or so ago. She established the Breakfast Club for children who didn't have the means to have breakfast. before they went to school, which is so fundamental for children.
She talks about activism as being less about talking, more about doing. She talks about it being underpinned by passion and purpose, but also a plan for how you implement it. There's this real sweet spot between the passion and doing. I think the other thing that she talks about is not to underestimate the value of small steps. Whilst a lot of the challenges ahead of us can feel enormous and possibly overwhelming, take small steps because they have an impact. She's demonstrated that through the work she does. She has a great book. I'm not on commission, but I would recommend reading it.
Yes, as a regulator, what can we do? There's progress well underway at Ofwat, including how we are developing our sector performance directorate. That's led by a fantastic lady called Helen Campbell. Really, that's understanding how we make better use of data, sharing data, being more transparent, and really understanding how our sector is performing and what we can do as regulators to support, enable and hold to account.
Again, there's that real sort of sweet spot as a regulator where we need to be enabling and holding to account fairly and equitably and transparently. The place I'm really exploring, though, in that activist space is, as well as what we regulate and the measures, hard measures that we set, and quite rightly, companies are held to account on, what are the choices we can make around how we deliver?
I think the best example I've got of this is the Boston Barrier Flood Risk Scheme. It was a project delivered by the Environment Agency a few years ago now. What the project team did was they retrospectively mapped the benefits of the project against the UN Sustainable Development Goals, the 17 goals.
This wasn't something they planned at the outset of the project, but they did look back afterwards and say, "Well, as well as it being a phenomenal engineering project, what other benefits did we deliver through this multimillion-pound scheme?" They recognised that, well, actually, half the design team were female, so that contributes to better gender equality.
BAM Nuttall, the constructors, they only employed people within a 50-mile radius of the project. In a relatively deprived part of the UK, that contributed to more sustainable communities and contributed to decent work. The project team went into schools to talk about engineering and climate change and flood risk management. Again, contributed to better education. Actually, when they went through the whole 17 goals in varying degrees, they actually contributed to every single goal.
What we recognised was, well, imagine if we start every project thinking through the lens of these goals. All those things were just choices. They weren't in the project mandate. They weren't in the contract. They didn't cost any more. They were choices people made because they could. Back to choices, back to Sir David King.
Over the next five years, the water sector is going to be investing more in infrastructure than we ever have since privatisation. How do we, through every pound that is spent, wring out the most value for society, for our customers and for the environment? I know, and we've demonstrated, there is so much more we can do, but it depends on collaboration. It depends on data sharing. It depends on having the will and the passion to do this.
If I can just finish with just last week, I was at a conference, the UK Summer Forum with British Water. They hosted an event for the supply chain, and water companies were there. It gave me so much heart and so much optimism that we can and will be able to achieve this because everybody in the room was advocating a similar mindset. I found it phenomenal. I think there's a coalition of people who want to make a big difference for the greater good because they know we need to. That's the activism I want to be tapping into in my role as Director of Environment and Innovation.
David: That makes great sense. I'm currently reminded by, in the week where ISG have collapsed, you talked about choices being made. Quite often, there's this cognitive dissonance between what people say they do and what they actually do. You have centred on the use of data. Do you use data to actually unearth the difference between what people say they do and what they actually do? Particularly in things like energy performance, we see that they claim they've made these savings, and actually, they haven't at all. How do you use data to unearth any of those discrepancies, shall we say?
Jo: Maybe not one to get into around ISG and the impact that has on people, homes, livelihoods, lives. It's absolutely devastating. I fundamentally believe that the whole system is set up to fail in terms of how we procure, how we contract, how we reward, how we incentivise, how we pay. I fundamentally believe the entire system needs to change. I think it's in our gift to do that.
How many things need to fail before we do that? That's not something in my gift or influence, sadly, but I know there are people, there's a lady called Louise Lado-Byrnes, who is leading a different approach. She procures purely on behaviours, purely on behavioural workshops, not about cost, not about scope, purely on behavioural. She gets a more diverse team innately, and their delivery performance outstrips the norm. The payment mechanism is different, the incentivisation mechanism is different, and what they value is different. They largely value behaviours.
How do we start to drive a different model, and again, what can we do? What can we do? Okay, maybe I can't change the whole system, where could we start to explore more of these things? Where could we start to try to do things differently? Again, that is something I'd love to explore. There's people doing it, but only in small pockets.
When you talk about how much can we believe what we're hearing, I think is a large degree what you're saying, isn't it? Sometimes what we're hearing doesn't seem to play out in reality. This is my huge interest and focus on psychological safety, David, because every single lessons learned report that's ever been published, what does it say? The reason a project went well is, why? It's not because we had a brilliant risk register or a fantastic forecast or a great Gantt chart. They are important. Absolutely, they're important.
Why did it go well though? When things went wrong, we had each other's backs. I could come up with great ideas and people listened to me, and we all pulled together. When projects fail, what's the main reason? It's people, it's behaviour. I spoke up, but nobody listened. I was too scared to speak up. The tragedy of the Challenger disaster. People knew those O-rings were going to fail. We look back on every single lessons learned. People in the team knew, but they weren't heard or it wasn't acted on.
One thing that we trialed at the Infrastructure and Projects Authority when I was there, and it's something, again, I'd love to explore more, is with the use of data and analytics, we can capture and start to quantify human behaviour. I don't mean in a sinister way. What we did was it was very simple app. It's called Meeting Quality. I have no shares in the company. I just don't know another product that does this.
Every week after the project team meeting on our transforming infrastructure performance delivery project, after the team meeting, the email would just plop into our email box. A very simple 60-second survey. How motivated are you feeling? How likely do you think this project is to succeed? Just a sliding scale. Are we measuring risks? Sliding scale, very quick. Then a bit of free text.
Ours was, if when you leave the room, you're asked by a trusted colleague, how's the project going? What would you say? You put a bit of free text. It's all anonymous, but everything is shared verbatim with the team. Everyone will see the comments, but you won't be assigned to names. Then the AI that runs across all that data starts to give real insights around how the team are feeling. Are they quite optimistic? Is the language positive? Is it fearful? Is it negative?
Also, what are the trends over time? Not on our project, but on another one, the team was staying very optimistic. Yes, we're going to deliver. The sustainability of their working practice, how they felt was dropping off. That's a lead indicator that a team is beginning to burn out and get tired. As a leader, you could step in and say, "What's going on? Let's talk about it. How can I help?"
Back to the sort of question about, how do we know what's really going on? This gives people a forum to be able to say, "I'm concerned about this," because we only really report on projects. I'm talking very much about projects, but you could substitute this for any performance measure. We only measure time, cost, and quality. The lag indicators, by the time you see anything in time, cost and quality, it probably happened many months ago. Unless you've got psychological safety in your team, which I would challenge most teams do not, then how can you trust that data? How do you know people aren't just telling you good news because they're too scared to tell you otherwise?
These insights, these behavioural insights start to give us lead indicators on how the team are feeling. Why not have that on your dashboard next to your time, cost and quality? Then you start to get so much more of a rich picture. I think, in that way, we start to-- again, it's small steps. It's activism. We start to shift the dial on everyone having an equal voice around that table, everyone being heard, and those good news cultures not being allowed to fester in all honesty.
David: We have a feeling that there's a toxic relationship with information, that if you're asked to provide some information, the first question you ask yourself is, how can that be used against me? It will be in the contract.
Jo: Fear, isn't it? Fear, psychological safety. Absolutely. How will this be used against me? Even when I was at the Infrastructure and Projects Authority, even sharing data between government departments, there was a fear. How would this be used? Is this going to be used as a stick to beat me with, someone said, just between departments.
David: We just had to abandon a project on quantifying defects in buildings, totally anonymized. People were very enthusiastic, but when it got to the commercial departments, it was stood on. People wouldn't give us totally anonymous information.
Jo: Here we are trying to improve health and safety. Here we are trying to tackle the greatest threat to our existence. We manage the wrong risks, David. We worry about the wrong risks. In doing that, we make the risks that really matter so much worse.
David: The human condition, I think. How can the water industry and building engineering sector work together to deliver higher-quality water management strategies to make buildings safer, healthier, and more sustainable? Are we currently missing opportunities to improve the built environment water services? I guess from your last answer, yes.
Jo: [laughs] I had the enormous privilege of coming along to the BESA conference last year. As I said, I've never met people like you all. You and Claire Curran stood up at the start and you talked about the nature and climate emergency. You talked about, we're going to do it, whether we're being told to or not. It was, again, that sort of choice, the doing the right things. It's the right thing to do and connecting people. By the time I got up to speak, I thought there's nothing more for me to say. [chuckles] These people are incredible.
What became so sort of shockingly obvious to me, and it had never even occurred to me, I think you're some of the most well-hidden heroes that there are, because like you said, everything that you and your members manage and deal with are at the heart of our biggest problems. Health, healthy buildings, the health issues that come from poor air quality, nature and climate emergency, so reducing carbon and the cost of living, obviously the cheaper, more effective we can make heating and air ventilation, the better.
You and your members have the ability and are unlocking so much potential and so much solving so many thorny issues that are at the heart of what our country is grappling with. I don't know what those connections are right now, but given that water, as the fabulous Ewan Rose said, is like the lifeblood of a building, then there must be connections. There must be ways to explore how we can work better together and how-- yes, what are the opportunities for us to be working better together? All of the potential that your members and your industry leave us is extraordinary. I'd love to explore how we can work more with you in the best way we can.
David: Yes. We like to describe ourselves as the industry you've never heard of but has a massive impact on your life.
Jo: That's it. Simply championing what you do, that's where I'm going to start, David, just championing what you do.
David: Most of it's hidden, and if you succeed, people aren't aware of it.
Jo: True.
David: When it goes wrong, that people are aware of it, as you know in the water industry, they take for granted clean potable water until they haven't got it. Then it's a disaster.
Jo: Yes, it's a fair analogy. When things are going well, maybe, you're doing well. Oh, sorry. When things are quiet, you're doing well.
David: That's the thing that makes it very difficult for people to value because it's a given. It's like breathing air, you just assume it's there until it isn't.
Jo: Yes. I remember chief executive of the Environment Agency for a good chunk of time while I was there was Sir James Bevan. He talked about wanting to make the Environment Agency better known and better loved. That was a phrase he had. He said, there isn't a town or a village in England, because that's what the Environment Agency covers now, where the air quality isn't better or the water quality isn't better or the ground quality or the waste, because the organisation sort of touches everything everywhere. Now, of course, we're all striving to do better. Of course, those standards need to be ever-improving. I'm not questioning that. Like you say, what we often don't know and don't realise what's going on when things are working well, that's for sure.
David: In your role, do you influence planning approaches, or can you influence planning approaches to ensure that built environment projects take water management issues into account at the design stage to avoid future problems?
Jo: At Ofwat, and this is an area that I'm getting more involved in, but it's very much early days for me at the moment, there is a collaboration between the Environment Agency, Ofwat and the Drinking Water Inspectorate around how we support and enable those early design stages of major infrastructure projects in the water sector. Yes, there's a huge role to play. I'd be interested to explore where BESA and some of the sort of building regulations and other aspects of water usage in planning and building, not that we have a regulatory role there, but it would be interesting to explore where we might be able to input, inspire, and enable more.
I think back to my earlier point, whilst that is very much focused on water usage, water quality, vitally important things, obviously, I also want to be saying, and what else? Let's be thinking about the UN Sustainable Development Goals. It is a framework that exists as a country. We are committed to delivering on it by 2030. Although curiously, we seem to have stopped reporting on it, which I don't understand why.
David: Sustainability in net zero. There's a big drive for growth at the moment. Where do you see sustainability in net zero sitting in the list of priorities? I think I know the answer to this, but if you could just tell us what you think.
Jo: If you'd asked me not that long ago, David, I'd have really worried about where it is sitting generally in the list of priorities, where it is in my list of priorities. Did you see David Lammy's speech last week? Our foreign secretary is saying our biggest threat is the nature and climate emergency. He's saying it's a bigger and more immediate and more urgent threat than Putin and terrorism. I'd encourage anyone to read the speech. It's on gov.uk. I think that's profound and correct.
When our foreign secretary is saying this is the biggest threat we face and this is what we as a government are going to be tackling, for me, that's a massive sea change. Whilst I really want to encourage everybody to do what they can, regardless of the limitations around this, I often hear people say, "Oh, well, we can't do that because it's not in the Treasury Green Book funding rules or it's not in the contract."
Just a few years ago, the Institution for Civil Engineers ran a survey about what makes good design. One of the questions was, what's the biggest blocker to including greenhouse gas emission reduction and climate adaptation in your designs? The main answer was, it's not part of the project brief. I just remember thinking, oh my God, when did this happen? When did this sort of learnt helplessness set in that we have to be told to do the right thing?
Let's wake up to what we can do. Let's really test the limits of what we can do within the rules, within the policies, within the funding, but make sure you're at the absolute limit, not down here somewhere, which is, I think, is often where we are. Of course, if you have leadership from the top, from our government saying this is our most important and biggest and most urgent threat and this is what we're going to be taking action on, that's massive. That is massive.
Also, within DEFRA, we have our first Minister for Nature, Mary Creagh, extraordinary leader, and the work that Steve Reed is doing to advocate for the environment and for nature. I think with the messages coming from the top it's very clear where it sits in the priorities. I was going to say encouragement, that's a bit light, what I want people to do is irrespective of whether you're hearing those messages from the top, please think about what you can do, what you can do every single day in the choices you make because your agency, your influence is always so much bigger than you realise.
David: How can building services firms get involved in Ofwat's Breakthrough Challenge and gain access to the funding available for collaborative innovations and projects, and what sort of innovations would you like to see from our sector?
Jo: Yes, so we have our Breakthrough Challenge, which runs on an annual cycle. For the Breakthrough Challenge, a water company has to be sort of the lead partner, but they can absolutely collaborate with people across all sorts of industries and sectors. I'd really encourage people to get involved. That runs on a cycle between September and April for putting submissions in and through to getting the funding. Now is a great time to be looking at it.
In terms of the innovations, it would be great to see, I'm not sure, and what I'd say to anyone interested is please get in touch with me and my team if people have got ideas that they'd love to talk through or some advice or anything about how to get more involved, then we'd be more than happy to help.
I suppose the one thing I'd say though about innovation is often we think about shiny things or gadgets, but I'm a big believer in just sort of doing the basics well, and that can be remarkably innovative and have a massive impact, positive impact on how we do things. For example, how we visualise data, how we share data, really driving up productivity, really enabling collaboration through data and technologies.
Sometimes it's the very simplest things or some of the broader enablers that drive the biggest benefits. I'd encourage people not necessarily to be thinking about shiny gadgets, which are great, too, but how can we fundamentally change the system for the benefit of all to deliver the best outcomes? Any ideas, nothing's too unusual or possibly even dull to talk about. I think sometimes the dull things, the things that seem a bit boring is where we need to focus our time and effort, [laughs] but I mean it. It's the grunt, and we don't want to do it.
David: That's all my questions, and our time is up, so I always like to try and summarise what we've discussed today, which is going to be a bit of a challenge today because we have been everywhere from Liverpool and the Beatles through to the Arctic Ocean. Just to summarise what I think we've said here is that it was your passion for the environment, sustainability, the climate disaster that drew you into the industry.
You want to make a difference through having a purpose that you think you can make a difference, and for people to do things, have agency over the things they can control and do them, and specifically don't be hidebound by contracts. Just do things because they're the right thing to do if, for no other reason, than it'll make you feel better about yourself and your future, and you'll be able to tell your kids that you've done it. To get involved in things, and particularly with yourself and Ofwat, because the worst you could say, I guess, is, "No, we can't do that," but if you don't, you can't do it.
Jo: Try me.
David: Does that about summarise things?
Jo: Sounds great, David. Thank you for listening and thank you for asking this wonderful question.
David: Dr Jo Jolly, Director of Environment and Innovation at Ofwat, thanks for joining me on Behind the Built Environment podcast. Thank you.
Jo: Thanks, David.
Episode 4: Behind the Building Safety Act
In this episode, we are joined by Nick Mead, Technical Director at Laing O'Rourke and Chair of the BESA Building Safety Act Advisory Group. He discusses the transformative impact of the Building Safety Act on the construction industry, emphasising the importance of compliance, collaboration and cultural change. Nick shares insights on navigating new regulations and the industry's future. The episode also introduces BESA's "Play it Safe" guide, designed to simplify what everyone’s roles and responsibilities are for complying with the Act.
David Frise: Hello, my name is David Frise, Chief Executive of BESA. Welcome to Behind the Built Environment, the podcast where I delve into the major issues facing our industry through in-depth conversations with key industry leaders. Join us as we explore the trends, challenges, and innovations shaping the future of the built environment. Today, I'm delighted to be joined by Nick Mead. Welcome, Nick.
Nick Mead: Hello, David.
David: Nick is the technical director for MEICA Systems at Laing O'Rourke, and also chair of the BESA Building Safety Act Advisory Group. Nick joined Laing O'Rourke back in May 2017 as a chief engineer. He is an experienced chartered engineer with over 45 years in contracting and consulting. Nick has a wealth of experience in a wide range of sectors and has worked within many industry bodies covering fire and technical issues.
Most recently, his role has been to support the business through the Building Safety Act and changes in CE marking. Between 2015 and '16, Nick held the position of CIBSE president. He has a Bachelor's Degree in Environmental Engineering and is a fellow of CIBSE and the IMechE. Again, welcome, Nick.
Nick: Thank you.
David: Thanks for joining us today. A long career.
Nick: Very long, yes. Very enjoyable, though.
David: That's good. If you get to the end of your career and you think it's been enjoyable, that's something. You're not quite at the end yet.
Nick: Not yet. No.
David: We kick this off with some quick-fire yes-no answers. Say yes or no, please. Not as easy as it sounds. Interestingly, we had Lorna Stimpson on from Building Control as our first one, and we asked her five questions on the Building Safety Act. I'm going to ask you the same five questions and hopefully, you give the same answers. Question 1, is the Building Safety Act the most important change in construction in your career?
Nick: Yes.
David: Does it cover all buildings?
Nick: Yes.
David: Yes. We'll come back to that, obviously. Is everyone in construction impacted?
Nick: Yes.
David: Will the Building Safety Act result in behavioural change in the industry?
Nick: Yes.
David: Will the industry be better because of it in five years?
Nick: Yes.
David: Do good companies who are competent and compliant have anything to fear from the Building Safety Act?
Nick: No.
David: We're on to the main body of the questions. You can do more than yes and no from here on. First off, so as a tier 1 contractor, one of the largest contractors in the UK, you're at the front line of the Building Safety Act. How are you adapting to what was described as the biggest change? You've agreed the biggest change in your career. How are you adapting to that at Laing O'Rourke?
Nick: It feels like I've got a small army on it, to tell you the truth. We've really put a lot of effort into this. We've been really fortunate that the company have recognised the significance of the change, and we've adopted a small team to pull this together and work across it, not only internally with our own procedures but to support industry and work with others to see how we can manage the change, but also look at how we work up and down. Up in our consultants, our design partners, our clients, and then down through the supply chain, manufacturing, and everything. A lot of work. I think we're in a good place but we're at the beginning of a long journey.
David: It must be considerable investment on the part that you want to do this.
Nick: Yes, considerable investment. I'm really grateful to be part of it and the support that the company has given us all internally but allowed us to also to work with industry and share and help develop industry. It's been a really good journey.
David: We were discussing, off-air, before we started, about the highly fragmented industry that construction is and engineering services in. How is that being disseminated down through the supply chain, and do you believe that they're listening and adapting?
Nick: It varies in a lot of the sectors and the areas you work in. I think those who are most impacted, particularly those who have design responsibilities, the sprinklers and the fire alarm, they're recognising what they've got to do and the impact of it. I think some companies are working with it. I think the problem the supply chain has is typical government information is quite open to interpretation, and it's how do they get their understanding of it, particularly smaller ones who don't have large budgets. We're trying to work with them to support them and bring them on the journey but it's so variable across the board depending on who you're working with.
David: Is that a danger for the industry?
Nick: Yes. I think in the tier 1 sector where we're working with it, I think, as the industry goes down and you start looking at tier 2s and tier 3s and people affected with it, I think it'll be a lot of hard work for some people and I hope that the regulatory doesn't come down too hard on people who just don't have that capacity or capability to develop it.
David: How about up the supply chain, shall we say, amongst clients and the professional teams that you take designs off?
Nick: Yes, it's an interesting one. A lot of clients, they are more intelligent now—not being rude to clients—but they understand more, understanding more their impact on it. I think where we have to get through it and where this is all stemmed from is we can't keep going bottom line fastest programme. All this now has an impact on what we price and what we programme to do, and make that clear to the client and to the professional team for the client.
I think the consultants and the architects have got a big learning curve. We, thankfully, should go back to design and build with this, and not this, "Well, it's good enough to start on site and we'll tweak it as we go along and we change things," and then we argue about the cost and get it designed, get it sorted and build it. the IKEA pack-type approach, "There's the pack, just go and build it."
I think that will be great for the industry. The client might struggle because that ability to change his mind as he goes along will be much harder for them, but it's got to be a better way to build a building.
David: Yes, I can't disagree with that. Is it a recipe, at the moment, though for indecision? I can't make a decision because I don't really know what my liabilities are going to be?
Nick: Everything's slowed down. The industry has slowed down. The two-staircase rule brought chaos into the industry. We see a lot of government projects in that process because they recognise that they've got to be more sure in their design and output before we can start on-site.
I think it's going to help a lot of the contracting industry because they have that skill set to be involved earlier to support the consultancies. That will be a better approach to how we go. We're in that journey now, and we talk about HRBs and non-HRBs. The Building Safety Act is quite specific in what it's defining, but the industry has got to recognise the massive amount of regulatory change that's gone on that affects everything we do in the construction industry, and that will be the hard part.
David: I'd like to come on to that bit of it. It's not just the Building Safety Act. Before I get to that, what's your view on how long it will take to settle down so that you have a period where we're no longer saying, "Well, I don't know what the law's going to really be interpreted in that way." Are we talking 2 years, 5 years, 10 years?
Nick: It's a very difficult call. I would hope we won't be talking Building Safety Act in five years. I think that's when we get that business as usual. Some sectors will move quicker because they're forced to. Some will try and understand where regulations are affecting them and responsibilities affecting them. The day job will take time to get there. Some sectors, probably two, two and a half years. The industry as a whole will probably be about five years, a few.
David: Going back to that question around what else other than the Building Safety Act, I've noted, in the Building Safety Act, you make the point of saying it's not just the Building Safety Act. There are other changes coming down the line that you need to be aware of.
Nick: The Building Safety Act is all about what they call the high-risk buildings. It is predominantly residential. It talks about care homes and hospitals, and hospital's a bit of a hybrid in the gateway process. The Building Safety Act on its own is only an ability to create change. It's a tool for government to bring other regulatory change. There are masses of them. They've changed the number of the building regulations and they are changing more. Building regulations affect every building.
There's the Fire Reform Act. There's the architects bill. There's the procurement bills. All these things are coming on through it on the back of the Building Safety Act. It's every building that we build, every structure that we build, has an influence of those rules and regulations. I think that's where some people might struggle in thinking, "Well, it doesn't apply to me."
If they're not up to date with all the regulatory changes and standards and things like that, it's going to keep going. That's probably going back to the last question, why I think it's five years, is we will still see changes in those regulations and standards that we'll adapt as we learn more.
David: In that vein, do you see a danger that the industry will be highly focused on making buildings safe for fire, and in doing so, they'll make them airtight, sealed, but actually won't ventilate them properly, for example, and we end up causing another problem as a result of too high a focus on one thing?
Nick: This is a problem we have with all rules and regulations and things, you've got the fire safety and types of insulation and things like that, but Part L energy is out there, we've still got part M, there's lots of things going on, and I think that's where you've got to try and look at where they all work for your project. Then how do you agree where there's a conflict? Because they will have a conflict. Insulation and fire rating of insulation, and types of insulation. You've got to look at what's the aim, and then you've got to agree that process with the building control officer to say, "Well, these are my conflicts, we think that's more important, so we're going to drive that." That's where the industry will have to get that skill set and knowledge developed in the whole industry.
David: We've just had a change of government, the sun has come out. Previous government were pretty sanguine in the fact they said, "Well, we've brought the Building Safety Act, we've done our bit. Over to you as an industry to develop that." Do you see the new government having the same attitude or do you think they will be more hands-on at this point?
Nick: I don't think so, I think they were still-- The Hackitt review always said industry had to change it, it was industry who would have to drive change, and they've got to. They're the people with the skill set. The civil servants and the government, they're not contractors, and builders, and building services engineers, they write a standard, typical with all regulations and guidance, is guidance, and it points you in a direction.
Providing we can, as an industry, work together with the likes of BEEs and things like that, give the industry a route to travel, then we should be able to do it. We don't need anything too rigid, because it stifles us, and also then if it goes wrong, that's why it's quite vague. I think it is up to industry. I don't see the government bringing in specialists and saying, "This is what you're going to do, this is how you're going to build it." It'll be up to us who have the skill set to go and make it work.
David: That's a great segue into the next question, which is really about skills, or SKEB—Skills, Knowledge, Experience and Behaviours, an unfortunate acronym that really, but in the quickfire questions, will it change behaviours, you said yes. Can you expand a bit upon that? How do you think that's going to change behaviours?
Nick: That will be the hardest thing for our industry, the culture of our industry. I think, for too long, now we've been forced into a position where we are building it quickly, we have the lovely term "value engineering," we're all about getting it quicker and faster. Change control will be very important now, and how we manage change. I've been doing it for 40 years, culture has got to go. I think there's going to be far more need for having systems and procedures in place and processes, understanding who's responsible for those decisions and processes, and people recognising, if they do something, what is the consequence of them doing it.
Quite often in the contracting world, we'll change a wall type without realising that the fire stopping, the fire damper now, doesn't become compliant. There's got to be far more integration. In the building services world, we build systems. A pipe doesn't work on its own without it going into a heating system. We have to think of buildings as systems now, and system engineering is the way our industry has got to survive and develop and strive to get through that.
Knowledge is good, we have good knowledge in our industry, we can prove paper qualifications. It's the culture skill set and proving competency, and what is competent, and who assesses, who is competent to assess someone as competent. That's the steep climb I think we've got.
David: Does it require everybody within the supply chain to be responsible for their own element of work? I'm trying to get to the point of-- there's often a cry for we need more clerk of works, we need them to come back in, but didn't that engender a feeling that if the clerk of works hadn't spotted it, we've got away with it? Isn't it now the responsibility of every contractor to evidence how they've been compliant?
Nick: Yes, I think everybody's responsible for their own actions. They need to be aware of the consequence of their action on others, you can't just change something because it suits you, or put something in a different place because it's easy. We've got to be better at how we go to work, and own what we take on-site.
David: You mentioned earlier about value engineering, something that delivers no value and little engineering, by and large. Do you see that the gateways, in particular, will see the end of value engineering as it's currently employed?
Nick: It will help it a lot, because if you are changing something between the gateway, you've got to prove that it's still compliant, meets the regulations and standards, and isn't just done for cheapness and cost. That will help, and I think, by having far more detail at gateway 2 before you start on-site, will give greater opportunity to get it right. Value engineering is a fantastic term we just use for getting it done cheaper, but what we've got to make sure is that, if that is done between gateway 1 and 2, it's managed properly and it's defined properly, and we still end up with something that is compliant and safe, and to a quality we expect it to.
David: If you were, let's say, building safety regulator for a day, is there one thing you would do that would make everything happen quicker, shall we say, or more effectively or efficiently?
Nick: Make sure people have read the rules, and know who they sit in a team.
David: How would you do that?
Nick: I think it's meeting with the right people, it's making sure you can sit down at the beginning of a project, make sure everybody understands their role and responsibility and how they're going to develop through the life of the project.
David: You hear an awful lot about, "We're just waiting for the building safety regulator to prosecute someone properly, and then everything will fall into place because people say, 'Oh, you're taking it seriously.'" Do you go with that view?
Nick: I think there's a little bit of that out there. I think people are nervous as to what level they will come down. I think this Building Safety Act will have to do something with impact to make people aware. Hopefully, it won't be too severe, and it won't be on the wrong people. It's a difficult call at the moment because I don't think we'll see things for a while. Where the building safety regulator, I think, will flex their muscles is in a chain control, and they will impose an 8 or 12-week hold to make sure something is picked up and changed. I think that's where they'll work first, hopefully before we go into the standing somebody in court, nothing serious.
David: Yes, fundamentally, this is about doing the right thing, isn't it, in the industry? Making sure everyone is both safe and the building's there for the long term, not short-term gain, which is the big culture change, I guess. Are you an optimist or a pessimist about this in the future?
Nick: No, I'm an optimist. This is great for our industry, how it used to be. We get back into the pride, deliver really something you can walk by and go, "I worked on that project, I'm proud of it."
David: I think that's a big thing. People come into work to do a great job, and we get in the way, stop them doing it. Finally, Nick, you're chair of the BESA Building Safety Act group. What does that involve, and what does the group do?
Nick: It brings the M&E contractors together who are working in this area. It opens good discussion for people to, not raise their concerns, but openly talk without fear of thinking, "Well, am I going to be branded? I don't know what's going on." It's a great forum for people just to talk and discuss on how we, as a group, through BESA can support not only to the tier 1 M&E contractors, but right through down to the smaller groups, and bring everybody on board to bring the building services along in line with compliance and regulatory standard.
David: You've recently launched a campaign in the group.
Nick: Yes, the playbook, I think it's really good. The trouble with the regulations is you could give it to five people to read and you'll get seven interpretations of that regulation. I think the playbook is really good because it enables people to understand how the construction industry works from right through to the client, down to the end of maintenance and handover, but puts it into the relationship of the football world from the owner of the club, down to the linesmen, and things like that, and how their people will relate to it.
It puts it in a very simple language that just gives some clarity on where people fit. If you imagine how clockwork a football team runs and how important everybody is in that team, it recognises it. In the construction side, everybody's as important. It's a really useful tool for people to understand.
David: Back to that, everybody needs to evidence their compliance.
Nick: Yes.
David: Now I know I said finally, but finally, finally, I'd like to do a little roundup to make sure that I've understood and hopefully our audience have understood and interpreted what you've said today makes sense. The Building Safety Act is the biggest change in construction in a generation, probably several generations. Yes, definitely. It has an impact upon all buildings, some more than others, and it certainly will bleed into others over a period of time.
Nick: Definitely, yes.
David: Everybody in construction needs to sit up and pay attention to this, because it's going to impact you no matter what you do on site.
Nick: Definitely, yes.
David: I'd add to that I think many people don't recognise change that's come as the Building Safety Act, but it's the Building Safety Act that's driven it. It may come from Laing O'Rourke, for example, now asking me to do this. It's the Building Safety Act that's driven it. The Building Safety Act, you're going to have to change your behaviours without a doubt. That's everybody if we're going to deliver a built environment that works and is safe.
The good news is the industry is going to be better because of it in five years. It has to be better where good companies can thrive, because the playing field is effectively level. There is nothing to fear for good companies. They can find out everything they need to know through your group on the BESA website.
Nick: That's right.
David: Great. Nick Mead of Laing O'Rourke, thank you very much.
Nick: Thank you, David.
[music]
David: Now the podcast news. As discussed earlier with Nick, we're thrilled to finally launch the BESA Play it Safe Guide. The football-themed interactive resource explains what your roles and responsibilities are in relation to your position on the pitch. We've taken all the massive information which is out there, simplified it, and made it relatable to you as a contractor, and your supply chain within the building engineering services sector. Visit thebesa.com/play-it-safe to download your free copy now if you're a member.
What should BESA do next when it comes to the Building Safety Act? What further support and guidance do our members need to ensure they are competent and compliant with the Act? Our Building Safety Act, the industry awareness and readiness survey has been launched to help answer these questions and will allow us to accurately gauge levels of awareness and understanding whilst identifying areas needing attention to drive cultural change.
Please complete the survey. It will take no longer than 10 minutes and you will be entered into a prize draw to win a signed and framed Euro 2022 winner Rachel Daly football shirt. Visit thebesa.com/play-it-safe to complete. The deadline is Friday the 30th of August at midnight.
Unfortunately, there's been more news hitting the headlines regarding companies filing for administration and job cuts. The BESA Legal and Commercial team has been busy dealing with member inquiries who may be affected in their supply chain by retentions or unfair contract conditions. BESA membership includes free expert legal advice with no hidden fees, which, when utilised, can exceed the value of your annual membership fee.
There are a number of fact sheets and resources and guidance in the BESA member resource area which can help with managing the risk of insolvency in construction contracts. We also offer BESA members a free introduction to contract law course via our online academy. For more information on that, log into your BESA member resource area, and if you're not a BESA member, we'd like to find out more. Visit thebesa.com/besa-membership.
Finally, the countdown is on for the BESA annual conference which takes place on the 17th of October at the Brewery in London. It's sponsored by Mitsubishi Electric. The one-day conference will set out how to inspire a better building engineering services industry for a safe, sustainable, and efficient future, with a broad programme of technical and topical seminars.
Brand new for this year is our dedicated skill zone which will introduce employers to a comprehensive suite of training services and recruitment support along with a guidance on how to identify and address skills shortages. Tickets are available on our website. BESA members receive a discount, and young engineers can attend for free.
Thank you for tuning in to Behind the Built Environment. Don't forget to subscribe to our podcast for more in-depth conversations with industry leaders. If you enjoyed this episode, please leave us a review and share with your colleagues. Stay connected with BESA for the latest updates and insight into our industry. Until next time, I'm David Frise, and this has been Behind the Built Environment. Goodbye.
Episode 3: Behind Better Indoor Environmental Quality
Join us as we discuss the critical issue of indoor air quality (IAQ) and indoor environmental quality (IEQ) with Dr. Phil Webb, Chief Executive of Health & Wellbeing 360 and a seasoned healthcare professional and industry representative for the Promoting Awareness of Air Pollution Delivery Group for the Welsh Government. Discover why indoor air quality is a major health concern, surpassing even the impacts of cancer and heart disease.
In this episode, Dr. Webb sheds light on:
- The staggering statistics on air quality-related deaths.
- The role of engineers in solving indoor air quality issues.
- Innovative technologies and systems to improve air quality.
- The importance of monitoring and maintaining air quality in buildings.
- How good air quality can enhance productivity and well-being in workplaces.
Tune in to learn how better indoor environments can lead to healthier, happier lives and why it's crucial for employers, building owners, and policymakers to take action now.
David Frise: My name is David Frise and this is the Behind the Built Environment podcast episode three. Our guest today is Dr. Philip Webb. Welcome, Philip.
Dr. Phil Webb: Thank you very much.
David: Philip or Phil?
Phil: Phil.
David: Welcome, Phil. Not Dr. Phil?
Phil: No, just Phil.
David: Just Phil. Great. Phil is Chief Executive of Health & Wellbeing 360, who recently became BESA affiliate member. Congratulations and welcome to the BESA community.
Phil: Thank you very much.
David: Dr. Webb is an experienced healthcare professional with extensive knowledge of academia, healthcare industry and the public sector. He's currently the industry representative of the Promoting Awareness of Air Pollution Delivery Group for the Welsh Government. Dr. Webb has a PhD in cell and molecular biology. His postgraduate academic work interests include health economics, prioritisation and advanced physical and digital engineering, including 3D printing and artificial intelligence.
His experience includes a 10 year career in industry with two major pharmaceutical companies within sales, marketing, R&D and medical and regulatory affairs. 20 years experience within UK National Health Service in national commissioning, specialised services, regional cancer delivery, innovation and value based healthcare. A firm believer in user-centric design and in understanding the importance of socialisation and the human machine interface in the development of technology and committed to net zero, smart and intelligent technology development and importance of making work and workplace fun. Thank you for coming today.
Phil: It's a pleasure being here.
David: We always kick off with a few quick-fire questions. The idea is yes or no to these.
Phil: Okay.
David: The first one, is indoor air quality a major health issue for the whole population?
Phil: Yes.
David: Do engineers hold the solution to the problem?
Phil: Yes.
David: Will filtration, purification and airflow technologies play a part in this?
Phil: Yes, as well as monitoring.
David: Is the state of our indoor air quality a public awareness issue?
Phil: Yes.
David: Finally, is the Net Zero agenda an obstacle to good indoor air quality?
Phil: Possibly.
David: Yes or no?
Phil: Yes.
David: Okay. You did better than most actually. It's very difficult just to say yes or no. We should turn it into a quiz game. We're going to kick off, if we may, with very little public money and resources are being spent on this issue, but you think that air quality is responsible for a very high number of excess deaths. More than the COVID pandemic, is your view, and cancer and heart disease and mental health combined. Where do the figures come for this? How do you justify that?
Phil: The figures come from nationally available statistics from public health bodies. The numbers that I usually quote, when I quote numbers, are all from verified, factual statements made by accredited and regulated bodies like NHS Public Health Wales, NHS Public Health England. It's quite astounding when you start talking about some of the impact of the figures. I usually talk too, in terms of numbers, in terms of deaths per 100,000 that are statistically adjusted for populations.
If you look at the COVID issue, and everyone knows that COVID was an international pandemic and a horrible time period in people's lives, really, it saw the biggest changes to our civil liberties with lockdown. Things that are unprecedented didn't happen since the Second World War. Really severe political measures to reduce infection rates for COVID. COVID death rates were around 34.8 in Wales per 100,000 population. If you can put that into context for major chronic diseases, cancers are about 278 per 100,000, cardiovascular diseases, heart attacks and strokes are about 290,000. The biggest killer per 100,000 is mental health, which reaches about 1,000 per 100,000, okay?
When you look at the statistics which are verified from national data on the impact of air quality, they range from about 1,500 per 100,000 in Wales to estimates around 10,000 per 100,000 in parts of London. In fact, if you combine all the other diseases together, they don't reach the same mortality rates that poor air quality actually reaches and attains. In fact, WHO just had a publication today to say that 1,800 people die every day in Europe just from poor air quality.
David: 1,800 people a day?
Phil: A day.
David: That's a staggering figure, isn't it? Before we get back onto that, what are the solutions that engineers offer that can help particularly with indoor air quality?
Phil: I think, Dave, the way that governments have tended to look at this is that they tend to concentrate their activities and their available resources on ambient air quality or outdoor air quality. It's the things that you see on all sustainability reviews and programmes. It's associated with pollution, vehicle pollution, agricultural pollution, et cetera, yet very little attention has been placed on actual exposure risks to our populations.
If you look at some of the statistics, Western populations spend over 90% of their time indoors. Even on a maths basis, exposure time for populations that we're involved with are all about indoor environmental quality. It's probably the indoor environmental quality, which has been an unrecognised and very silent killer in those statistics that I just mentioned at the beginning of this interview.
David: What sort of systems can we, as engineers, install that mitigate that problem, mitigate the risk?
Phil: If we believe that we're spending 90% of our time indoors, engineers and architects build buildings. They design buildings. They look at the materials around buildings. They look at planning around infrastructure. They look at the standards and specifications for the building themselves.
Engineering facilities management and building management systems, in my opinion, have a tremendous potential to improve the overall health and well-being of populations, bearing in mind, we're spending 90% of the time in buildings, our homes, our places of work, public spaces, schools. If we have the ability to design think our way through better buildings, we will end up with better health and well-being for our populations.
David: One of the things we often say is that we install products, we stick them in and don't really check that they work. A critical feature of this is the actual long-term operation and maintenance, isn't it? It's no good having a fantastic air filtration system, ventilation system, purification systems, if you're only concerned about where they've been installed, but they don't work. How do we ensure that?
Phil: I think it's the regulation around facilities management. I think that apart from a legal responsibility to ensure buildings are maintained to a certain quality and standards, and that includes all the technology within the building, including ventilation systems, filtration systems, purification systems, sensors, meter and monitoring, which we don't do enough of, and hopefully we'll cover a little bit about how we actually know that particular environments have got particular concentrations in there.
I think there's a social and an ethical responsibility on us as engineers to be able to do this in a way that not only puts innovation at the beginning and at the centre of any building design, but maintains it for the longevity of the building. We're talking of the fact that actually from a building's perspective, we're probably reaping the health and well-being benefits or disbenefits for really poor planning in the 1970s around buildings.
If we are very interested, and I think we should be in the well-being of our future generations and our children and their children, we really need to focus on the 60-year life cycle and lifetime of a building. That's how long they last for, that's how long we should be maintaining them at a particular standard and a particular level.
David: I don't think anyone would disagree with that, but there is a problem of perception, is there not, with air quality? People are rightly outraged by pollution of our rivers and the beaches, but you can see it and it has a direct impact. Whereas air quality issues tend to take much longer, often only appear at post-mortem as the cause of death. How do you educate the NHS, clients, that actually you need to invest in this now for long-term prevention of disease in the future?
Phil: That's a really good question. I'll use a medical anecdote to illustrate this. Hypertension never used to be measured, but it's a leading because of cardiovascular death, and people just didn't bother measuring it until they realised the consequences of very high blood pressure on the human system, and particularly cardiovascular events like heart attacks and strokes.
We now routinely measure your blood pressure when you go into a GP's. If there's anything wrong with you, they usually take a blood pressure check. They usually check your heart rhythm, okay? It's exactly the same with buildings. If you're not measuring anything, and this goes back to the conversation that we might go into about sensoring, metering and monitoring, you actually don't know what the problem is, but you need to know what's happening in a building and in various different parts of a building in any given time.
Because as we'll see, and we'll talk a little bit about the British Standard, which is BSI 4102, that mandates you to be able to meter and measure what's happening in your environment and in your building, and then look at rectification around how you use your ventilation systems, how you use advanced digital technologies like artificial intelligence to tell a building, don't open the windows outside because the outdoor monitor is saying that there are high levels of pollution for PM2.5 and nitric oxide. Keep the windows closed.
The BMS system will kick in. It will ventilate, purify and take it down to levels that are consistent with BSI 4102. It's the advancement of the combination of different technologies and smarter technologies that I believe is the future for buildings in the next 5 to 10 years.
David: Again, I don't think I'd disagree with any of that. I've been in buildings that have advanced BMS controls and the windows open automatically when you're in a room and people didn't like that, they don't feel there's a control. The point I'm getting to is, how do you inform people that the air quality in this building is bad, is poor? Because they might get a headache eventually from high CO2 levels, say, but how do you immediately inform people you're going into a space that is not good for you and these are the consequences of that in a way that doesn't scare them to death but just informs them?
Phil: I'll take the scare them to death bit first because people get less afraid when they become familiar with information and the familiarisation of the information that surrounds us, bearing in mind that we're inundated with information on a day-to-day basis; on your phone, on TV screens, on monitors that exist everywhere. I came through the tube, there's monitors everywhere.
There's nothing stopping us informing the public of the air or environmental quality in a particular space because we're already used to monitors being around everywhere. We're already used to be told on the TV that the temperature today is going to be 18 degrees centigrade. The pollen count is going to be high or low if you're allergic to pollen. What we're trying to say is part of that information dialogue needs to become mainstream to people.
People should be getting used to the fact that actually, weather reports should say your temperature today is this, it's going to be a bit cloudy, it's going to be a bit humid, the pollen count is this. By the way, your local pollution level in your surrounding area is going to be this today. If you're thinking of going out on a picnic, the best places to go out to picnic for pollution for outdoors is going to be this area or this area.
On an indoor basis, you should be able to walk into a building and it should be able to tell you on a large iPad on the side of the wall exactly what the environmental conditions are in that particular building based on the good quality sensors that that building has and an interpretation that allows you to have health and impact interpretations for you so you don't have to worry too much about it. You should be able to form a choice about where you go.
Part of the choice agenda is the bit that we think is going to change human behaviours. If you're faced with information and a choice about which shopping mall you want to go, because the indoor environment in St David's Centre in Cardiff is at such and such a level, but if you went to another shopping mall, the indoor environment is better, most people would act on the information given to them and choose to do one or the other, which then derives the issue around commercialisation. Commercial advantage for people who own buildings is to ensure that their buildings provide the best environment and the best experience for anyone using their buildings.
David: How advanced are we in that link between good air quality and say, productivity, something that has commercial value to clients? The reason I would say that is it's fine doing the temperature report every day, the weather report, because I can't do anything about that. The moment you tell somebody who I'm asking to come and work in a building that I own and occupy that actually the air quality is rubbish, I have a duty to do something about it. I can see that actually better off if I don't know, then I don't have to do anything about it. It's there a link between the commercial value of giving people clean air.
Phil: Dave, let's unpick this. If you're an employer, you employ people and you'd like them to come back to the place of employment post-COVID now because people feel that productivity has dropped slightly because people are working at home. You want to positively incentivise your workforce for coming and working in your office now. You run a sickness and absence rate, and there's already good evidence linking high sickness and absence rates with poor quality environments that we're talking. If you talk about the NHS, their sickness and absence rate is about 7.2% to 8% of a workforce that's multi-hundreds of thousands of people.
Even if you look at government policy, there's a commitment manifesto for people to put more professionals and train more professionals for the NHS. Surely you'd be better off creating better environments for them so when they went to work, they didn't get ill. Actually if you do the maths on that, that creates more people returning to work than you would ever be able to employ and train in a short space of time.
My retort back to somebody who has an organisation that has people is that the best way to get the best people is to prove that you care for them and you prove that you care for them for creating the best environment for them to work in, number one. You retain them from creating the best environment to work in, number two. They don't go off as sick if you create the best environment for them to work in as well. Actually, your conversation with your staff would be, "Come to work. It's a better place for you to work. You'll be more productive and you will be weller and healthier than you would be at home."
David: Actually, that conversation came up today. We invested in air quality products for our office and the air is cleaner and it's cooler. Both Claire and I came in today because it was better in there than at home, as they say. We touched on the development of a new British Standard 40102 Part 1, which you were heavily involved in the development of. Can you tell us a bit about that and what drove you to get involved in that?
Phil: That's part of our story about how we became Health & Wellbeing 360, really, Dave. Originally, BSI 4102 was driven by EFT Consult, which is part of the group that we now work for. Their perception at the time, this goes back pre-COVID when this actually kicked off, originally as a PAS, they looked at the health and wellbeing impacts that were happening in and around built environments. They went through a process of looking at international standards to see what the measures and the parameters would be to measure and to be able to do something about indoor environmental quality in buildings.
What they actually found was, is that the international standards all disagreed with each other. WHO doesn't relate to what the UN said, doesn't relate to what different countries said, doesn't relate to what different sectors said. They thought having a unified PAS at the time to be able to be consistently measuring the same thing across geographical areas would be a really good thing to do.
What actually happened was COVID came. They had to wait until COVID finished from a British standards perspective, but then there was an unprecedented speed of accelerating the PAS to a British standard. Literally it went through in record time because there was an acknowledgement from British standards that this type of standard was critical in moving us forward on the built environment engineering agenda.
Now, that went through EFT consult. At that time, my company was called Respiratory Innovation Wales Limited, which was a company funded by Welsh Government specifically to look at the population impacts of innovation in the respiratory space. We were working on exactly the same thing but from a very different perspective. We were taking a health and wellbeing, health and social care perspective around this, EFT consult were taking a technical building engineering perspective around this.
Then on the 29th of February at midnight, our natural progression was to go to a limited private company from Welsh Government, which we completed with EFT and we became Health & Wellbeing 360, combining the health and social care approaches that we had adopted on population level health and wellbeing, together with a technical building and services engineering perspective that was promoted and developed by EFT resulting in the British standard.
David: We're talking about whole building solutions to this. There's been a big problem with the quality of metering and monitoring devices for airborne contaminants. What do you think needs to be done about that?
Phil: I think there's been largely a positive response, particularly in the low-cost sensor area. What we're really talking about is low cost, but reliable sensors that can be deployed at scales. If you compare these, and I don't know whether you're familiar with them, with the government funded big URLs that exist dotted around through DEFRA, those sensors are very sensitive, very specific, but they cost in the hundreds of thousands. You're talking about £50,000 to £100,000 for a unit like that.
We know in the buildings environment that is unaffordable on infrastructure. Nobody can afford to put that type of level sensor in place in buildings at scale. We're talking about trying to scale these up across all buildings.
In the low-cost sensor sector, we're probably talking about sensor array. If you talk about the British standard, we're trying to work towards a British standard array that covers about the 11 variables in the British standard; heat, light, humidity, gases, particulates. We're talking about the £400 to £600 per sensor, not the £100,000 sensors. There are key issues around this though.
Firstly is, the British standard advocates concentrations measurements, not derivatives. We would not want people to invest in sensors that derived a calculation based on voltages that didn't actually measure concentrations at all. We think that they are largely unreliable. In the sector that we're in, poor quality data and information leads to poor quality decisions made on people, which, as I've said to you, results in massive amounts of mortality rates per 100,000.
We want good quality data based on good quality sensors that measure concentrations, that come in an affordable price to deploy, whether it's your home-- The British standard on domestic has started, as you may be aware. We want them in commercial buildings, public spaces, et cetera. We need to be able to independently verify that the sensors work to existing parameters when they're tested. We are looking for the development of an independent testing sensor for low quality sensors. We're already having conversations with some university partners about where we set this up and how we do it.
Actually not to make price of testing a barrier to the industry. This also is going to be at low cost and reasonable. Then we're looking at how do you actually get this in a place where we can scale this up? Does this need to be about infrastructure development at the point of architectural development and planning stage for buildings? Does it then gets absorbed in the cost of the building? How are we looking at retrofitting? This requires an industry-think about how best to embed some of these technologies at low cost, but still reliable and deployable in the way that we look at buildings, both new buildings and retrofitting.
David: It is the key, is it? Not that until you've measured it, you can tell what the air quality is. You can't do anything about it.
Phil: Yes, and I'd go back to the medical analogy. You never sit in front of a doctor and he says, "I know what's right for you" just by looking at you. There's usually a set of diagnostics that are done and we're saying exactly the same for buildings. You have to be able to identify in order to rectify.
David: Makes the invisible visible to people. How long before you think that every building will have air quality-- Well, just environmental meters and monitoring devices, just as standard. It's just a thing we all have.
Phil: I think this should become-- there's two ways of looking at it. The first one is, if we collectively believe that this is the correct thing to do for buildings, then we have a collective responsibility to ensure that the standards that apply are basically maintained and embedded in the way that we design thinking buildings. That's the first thing. BSI 4101 came into being in April last year, and we've deliberately spent time trying to make people aware of it so as they don't get a surprise when your insurance company gets a notification to say that your building's not compliant with BSI 4102.
We don't want to make an enemy of the partners that we need to work with. There's a process of awareness that people become familiar and aware of the standards and what is required to implement them at affordable cost.
The other way of looking at it is competition. Industry thrives on competition. It's a conversation that we've had with hoteliers. If you really want an advantage on TripAdvisor, rather than just price, advertise that your entire hotel chain and every single room in it is equipped with a way of telling the person who's booked that room exactly what the environmental quality is in their room and in their hotel, and actually positively promote it as you will get your best health and wellbeing experience because we have state-of-the-art technology that ensures that your stay at the Celtic Manor or at the Hilton Hotel is protected and you know what the environmental quality is in your stay, a positive experience.
There's the legislative bit that you have to do it, and then there's a competitive bit, which is can people make a competitive advantage, which affects their price point on how they sell environmental quality to people using their services.
Hotels, cruise liners, I've been on Great Western Railway and the Tube, yes? How do you positively use the fact that you spent money to improve your environmental quality to get a commercial advantage and a return on investment by promoting it? We believe that actually results in several pounds on your price point, if you're a Costa Coffee, for example, or several pounds on your booking rate on booking.com.
David: That requires a complete flip on the current status though, because people don't value building engineering services until they haven't got it. If you get it right, they don't notice because they're not hot, they're not cold, and they can't hear it, can't see it or smell it. Therefore, it's not something that impacts until it doesn't work and they're suddenly hot, or they're in the dark or whatever.
This still requires you to be able to say, hey, look, the air quality is good in here to promote that. I completely get that. Can we move on to a topical thing, which is about black mould and the impact of black mould, which we've seen, I think, nationally in some pretty awful cases in homes. Do you think there's another scandal heading our way through mechanical ventilation with heat recovery that's been badly installed and is not effective, not working, and therefore we effectively have a sealed building, but not correctly ventilated?
Phil: I think it goes back to design principles, if I'm being honest, Dave, okay? If we have a conversation with the industry about what we're trying to create in reality-- I was delighted to present to SIBC patrons group, and we had a conversation about this. There are fundamental questions for the building and engineering services industry. Why are you building buildings in the first place? Are you building them in a way that just stops you being sued for poor design, which is the minimum, very conservative way of building a building?
I'm building this, but I'm only building it so I can't be sued as a consequence of it legally or are you building a good quality building? If you're building a good quality building, in reality, what's the difference in the price point for how much it costs to actually build it? The difference of building a poor building and a good quality building is actually negligible, particularly if you're looking at some of the suggestions we're making on the embedding of technology as part of the infrastructure of the building.
I don't think it's a big jump to move away from building adequate quality, defensible buildings to actually building good quality buildings based around the design principle of the health and wellbeing of the users of that building at the center of it. There's a bit that my chair, Dave Keefe, always said, which is, "If you look at it and design a building from a net zero decarbonization perspective, you end up with a hermetically sealed, well-performing box, which is horrible to actually be in there as a human being." We're not trying to build unlivable buildings and unworkable buildings, we're trying to build good buildings.
David: I think the same could be true of the Building Safety Act, where we seal them for fire safety, but neglect the ventilation. We're still buying it at the cheapest price. All these products are perfectly good. Mechanical ventilation heat recoveries are fantastic products, but when poorly installed causes problems. Do we have a skills and training problem in the UK that we need to address?
Phil: It depends. I always look at the definition of a problem. I don't see it as a problem, I see it as an opportunity. I think that there's an opportunity to address skills and training. There's an opportunity to look at good design thinking, both architecturally and in terms of designing buildings, period.
I think that there's plenty of evidence about things we can learn from previous failings in the past. We've gone through decades of different types of buildings being developed, all of which have got recorded deficiencies against the design of the building. I don't think it's too far a push for us to learn from the failures of the future, to design better for the future. The past should light our way to build better buildings for our future generations.
I don't think it's a huge step to do it. I think there's an opportunity to train people to think differently when they're designing buildings, as well as the ability to then install and develop the installation of new technologies in buildings. It comes all back to design thinking. I used to do a lot of work with IBM, and the first thing that IBM would say on any given problem, is "Take as much time as possible to design think what you think you're dealing with, and then get as many views into how you're dealing with it as possible."
David: Somebody, I think-- Well, a couple of European associations around this area issued a manifesto recently calling for good air quality to become a basic human right in European law. Do we need a new Clean Air Act?
Phil: NHS, well, not the NHS, Welsh government have just produced a Clean Air and Soundscapes Act for Wales for 2024. It's quite interesting because there's certain devolved powers for Wales that has got direct control, particularly around buildings. Now, the dialogue with Welsh government, as with all governments, has largely been around ambient air quality to begin with, but because of certain lobbying and a consideration of the actual facts around exposure times and risk, they've started to think about the impact of indoor air quality, actually, on the population. That's an emerging thing coming from Wales. They've already got a new Act. I was at the Senate when it got passed.
Legislation is one thing, human behaviours are another. I'll put a different spin on this. If Mrs. Jones talked to Mrs. Williams and liked Mrs. Williams' new house, and Mrs. Williams said, "You know what? My house has got ventilation in there, it's got purification in there. I go into my front room as soon as I walk through the door and there's my little keypad for my security system. There's a little iPad on there that tells me every single room's environmental quality, and Little Johnny, he's got asthma, he hasn't had an asthma attack since we moved into this new house. Temperature's fantastic. My energy bill's actually reduced."
We'll talk about the relationship between energy and air quality in a minute. Mrs. Jones turns around and says, "How much does that cost you, Mrs. Williams?" "Same as it cost you, Mrs. Jones." Mrs. Jones as a consumer starts to want what Mrs. Williams has got. I would say legislation's one thing. Legislative bodies are one thing. The real thing we need to get to is how you drive human behaviours to want the benefits of environmental quality. Why they want it, whether they want it for themselves or whether they want it for their families or their children, why people would want something like this.
I think the consumer side of this and the consumer advantage around this is the thing that will actually change and drive human behaviours, not the legislation. The legislation is about organisations who would want to build in a specific way. The driver commercially comes from demand from people and demand from people is about an awareness programme of why you would want this for yourself and your family.
David: Okay, so that ends my formal questions on this. I'd like to really try and summarise what we've learned today from you. 90% of us spend 90% of our time in a building, therefore there's significant social value to getting the environment correct within those buildings. The solution to the problem is that you first identify the air quality by good monitoring, good metering of the air quality within buildings.
Phil: Yes, I would broaden it to environmental quality because you have to include heat, humidity, temperature.
David: It's not a single thing, it's a range of things that you need to monitor that improve wellbeing, shall we say.
Phil: Yes.
David: The benefits of a good environment, as we said, are a huge social benefit, but actually, if we invested more in the environment of our buildings, we would be able to reduce the NHS bill through prevention of ill health rather than waiting for people to get ill and treat.
Phil: Massively.
David: In fact, the poor air quality in particular is killing more people than a range of other diseases in this world. The building engineering services sector has the ability to massively influence this agenda and to deliver buildings that actually work. In BESA, we describe it as the heart and the lungs of the building, the stuff that makes a building work. The benefits of that are clearly there and what we have to do as an industry is work out, have value proposition that people start to value the air they breathe in a different way than they currently do.
Phil: Absolutely correct.
David: They should use the British Standard as a template to how we are going to take part in this journey to improve everybody's mental health, physical health and wellbeing.
Phil: I think that's a brilliant summary.
David: Oh, thank you very much, Phil. You can come again. Final, final question. Are you up to mystic about the future or pessimistic about the future?
Phil: I'm very optimistic about the future, actually because I think there are certain moments in time that we can actually positively, in reality, do something about a problem. One of the reasons why I moved away from the NHS and went into the job that I'm doing currently is because the NHS doesn't tackle population level wellness and disease prevention well because it can't affect change in the areas that it needs to. It can't look at energy. It's not involved in food. It's not involved in buildings. It's not involved in environmental controls.
Those are the biggest key determinants of health that actually work out whether you're going to end up in hospital in the first place and what stage of your life you are going to end up in front of a doctor anyway.
As I said to Claire, there's a calculation that I'd like to end on. You are going to spend 7,256 times the amount that you're going to see your doctor in a building that you're going to be in, whether it's a public space, your home or a place of work. Even if these interventions were 17,256 as good as seeing a doctor, we'd still be in front of the NHS in providing good health and good wellbeing. The opportunity to change things for the population, for the UK as a whole, for Europe and global is massive just through changing the way that we think about buildings.
David: Dr. Phil Webb, Chief Executive of Health & Wellbeing 360. Thank you very much for coming to the Behind the Built Environment podcast. Thank you very much, it's been a pleasure.
[music]
Now for the BESA news. This week sees World Refrigeration Day and to tie in with the coolest day of the year, we have launched a new technical bulletin, TB57R290 in Air Conditioning and Heat Pump Equipment. That rolls off the tongue, that's a really catchy marketing title, which is available to download for free on the BESA Knowledge Shop. Also, we offer a range of refrigeration and FGAS courses via the BESA Academy. If you are looking to subcontract FGAS work, then look no further than the UK's leading FGAS register, REFCOM, which has over 8,000 FGAS approved companies on it.
To tie in with today's podcast talking about air quality, last week we celebrated Clean Air Day at The Wave in Bristol. We want to remind everyone that we have a suite of award-winning free IAQ and mould guidance available to download, again on the BESA Knowledge Shop. We've launched the BESA Manifesto with our range of policy proposals for the next UK government, which includes fair payment, building safety, IAQ, Net Zero and skills, all the burning issues which affect our members daily.
The digital SKILLcard is now live for both Apple and Android users, enabling contractors to assess sites quicker via the SKILLcard QR code on your mobile. Plus, it reduces the amount of plastic use, so we're all playing our part in reaching our Net Zero targets. Visit the SKILLcard website to find out more. Whether or not you like it, our footy fever is sweeping the nations, not with England's performances to date and Scotland's untimely exit, but with the kickoff of UEFA Euro 2024, we've been working on something exciting, which we can't wait to share exclusively with BESA members next month.
We know the Building Safety Act can be challenging to grasp, which is why we've developed a very straightforward interactive guide that uses football analogy, making it easier for you to understand what your role or position is and what your responsibilities are for meeting organisational capabilities and individual competencies in the Building Safety Act. The Building Safety Act applies from everything from a shed to the shard.
The Building Safety Advisory Group met last week to review the content, so we're making our final tweaks before our mid-July launch of the BESA Building Safety Act "Play it Safe" campaign, so watch this space.
Finally, the deadline is fast approaching for submitting your entries in this year's BESA Industry Awards taking place at The Brewery, London, on the 17th of October. Entries are coming in thick and fast, so make sure you, your employees, colleagues, apprentices and businesses get the recognition they so well deserve. Deadline, Friday the 12th of July, so visit thebesa.com/thebesaaawards to submit your entries for free. Thank you for watching and listening to the Behind the Built Environment podcast. Join us for the next episode in about a month's time. Thank you.
Episode 2: Behind Gratte Brothers Limited
In this episode, the spotlight is on Remi Suzan, the newly appointed Managing Director of Gratte Brothers Limited, a family-owned UK building services company that has flourished since its founding in 1946. With a turnover of over £250 million, Gratte Brothers thrives on repeat business and a commitment to innovation. Remi emphasises the significance of offsite construction in boosting efficiency and quality while addressing skills shortages. He also discusses the evolving impact of the Building Safety Act and the challenges of implementing BIM in the industry. From operational improvements to strategic leadership, Suzan's insights paint a dynamic picture of Gratte Brothers' journey and future in the building engineering sector.
David: Today we're joined by Remi Suzan, MD of Gratte Brothers Limited. Gratte Brothers, one of the UK's leading independent building services companies, set up by Derrick and André Gratte as an electrical contractor in 1946 in Knebworth with £100 of share capital. Three generations later, they are still family-owned with a turnover of over £250 million. Remi took over in April after 20 years in the business. He's been design director, engineering director, as well as deputy managing director. Remi, congratulations on your appointment, and welcome to Behind the Built Environment.
Remi Suzan: Thank you. Pleasure.
David: Now, we like to kick off with just some quickfire questions just to set the thing up. Yes, no, if you possibly can. Building Safety Act, do good companies have anything to fear from the Building Safety Act?
Remi: No.
David: Is offsite the future for the industry?
Remi: Completely, yes.
David: Should M&E contractors do more principal contractor work?
Remi: That's not an easy yes-no. It depends.
David: I'm going to press you.
Remi: If they can, yes.
David: If they can, yes. Great. Does BIM work for the contractors?
Remi: No.
David: How would you describe the current building services market in the UK?
Remi: I think it's very varied for different companies that are operating in different elements of the environment. At Gratte's, we're very focused on the commercial work rather than we don't work in the public sector. I don't really have a view as to what's going on there. We don't really do domestic either, but we commercially work on office blocks, data centers. Data centers has been the big thing for us over the last 20 years. At the moment for us, it's very busy.
David: Very promising then.
Remi: Yes.
David: I think you described in a recent interview we did for the Top 30, you described Gratte Brothers as being in a very stable place. What are your business priorities for Gratte Brothers?
Remi: Most of our work is repeat business. 80% of our turnover is with existing clients. The focus is to keep the existing clients happy so that they want to keep coming back to you. Obviously, we do look to expand our client base, and we will tender work that comes in from those avenues. Generally, it's about repeat business, keeping your client base very happy.
David: You've had a focus on, shall we say, operational improvements like digitalization and those areas. Are they key to you?
Remi: Oh, completely. You've got to move forward. The world is changing very quickly. The industry has moved into BIM and 3D coordination, which is the obvious thing that people think about when it comes to digitalization, but there's so much more to it. There's now the automating programming packages you can use, the dashboards that feed into the management teams from automatically taking data from programmes, from logs such as RFIs, information, all sorts of things.
David: It's essentially the medical jargon, do no harm, first of all, but improve the operational efficiency of the business as you do that?
Remi: Completely. We've taken an operational director that was very IT-based, and we basically gave him that role in the business. He's no longer operational in terms of project work. He's got the title strategic director, and his role is completely looking at new technologies, how we can integrate them into the business and delivering of projects. I think we've always had that, but it always used to be a job for a director that was busy doing his day job. Therefore, it always took forever to bring anything new in because the day job always took over and the improvement things got dropped. By actually taking a director and saying, "Right, you are responsible, and that's all you're going to do," we've ensured that that has progressed continuously.
David: You're using things offsite increasingly to help combat your skill shortage, but also improve quality?
Remi: We've got two offsite facilities. We've got Worthing, and we've got Chelmsford. Worthing is a welding facility, and Chelmsford is what I would call offsite pre-assembly. We're making all sorts of things in Chelmsford, from full electrical risers to distribution boards, to mechanical pipework, pump skids, but we do it all with our own labour. It's actually skilled electricians building it or skilled pipe fitters. There's no de-skilling. People have argued that you could save money, but then that's where you drop off on the quality side of things.
Just the act of how you build in that controlled environment is so much better. They've got, all their tools are all bolted to benches. There's none of this balancing on the edge of a toolbox with a chainsaw or whatever. All of the materials are to hand. You can go to lunch break, and you can just leave your tools next to what you're working. Go to lunch break, come back, rather than having to pack them all up and get them out of the stores or whatever, and you waste hours on a building site. At the moment, I would say that on some of our bigger projects, we're building between 30% and 40% of the projects in Chelmsford, and just delivering it and bolting it into place. The vision is eventually 70% to 80% of the projects.
David: This also helps one of your other challenges, I guess, around sustainability, and your carbon footprint reducing that.
Remi: There's an argument that you're increasing your double handling things because you're having stuff delivered to Chelmsford, you're building it, and then you're moving it again to the site. That petrol or diesel offset is far reduced when you look at the significant reduction in waste because every bit of off-cut is kept at Chelmsford. Then when you need 400 millimetres of a piece of pipe or a piece of conduit, you just go to the rack and you get that 500 millimetres that was an off-cut, where, on-site, it would have ended up in a building site skip.
No, the amount of waste is reduced massively. Like I said, the improvement in production is huge as well. My team at Chelmsford could build an entire electrical distribution board, pre-loom it, pre-test it in a day, where if you were doing it on-site with electricians, you're looking at four or five days' work.
David: It's a significant savings then.
Remi: Significant.
David: An improvement in quality presumably.
Remi: Quality, but also from a client point of view, if you've got an electrical switch room, then I can't start until the builder's build the room, and often painted the floor, put a lock on the door. I'm landlocked, I'm locked, I can't move forward until that room is ready, where, if I build all that off-site, I've disconnected the programme, and then when the room is ready, it takes me three days to fit the room out when it could have been four, five weeks' work.
David: In a sense, it also allows you to take control of the elements that were out of your control in the conventional way of vetting.
Remi: Oh, completely. It decouples the programme, so you can get on with your work, even if you can't get on on-site.
David: Presumably that's where the greatest risk to you is financially, is the programme.
Remi: From the client as well.
David: Yes. Now I'm going to take you right back to the very start now. What drew you to engineering in the first place?
Remi: Absolutely nothing. I knew nothing about what this job is. My father was a chef, he was French, obviously, with a name like Remi there.
David: Certainly, you should be a chef, a famous chef. You said he worked for the Roux brothers, didn't he?
Remi: No, he knew the Roux brothers.
David: He knew?
Remi: He was the head chef of the Savoy Hotel. He came from Paris, he was headhunted, brought over to Paris. He worked in a lot of the West End restaurants and stuff like that. At 16, I was under threat, "You either find a job or you're going to come and work in my kitchen." I would have done absolutely anything than be my father's apprentice. I ended up going to the careers office, which I know you'll have to explain to your viewers what that is because it doesn't exist these days. Basically, at 16, you went to the careers office, you filled in a multiple choice list of questions, they fed it into some very basic computer, and it spat out what jobs you were most suited for.
Mine said either engineering or a policeman. They looked through their Rolodex, which I guess is the old version [crosstalk]
David: [unintelligible 00:09:21]
Remi: An old version of the database, paper version of a database. This lady pulled out a job opportunity for a local company called Benham Building Services. All she said was, "I think it's the tool makers." I had no idea what a tool makers was or what Benham Building Services was. Anyway, I had an interview, my father drove me there, made me take my earrings out and comb my hair. I was packed off in, I did the interview, I had no idea what I was being interviewed for. The guy halfway through it, started talking about plumbing. I'm like, "Oh, plumbing. Yes, I could do that. Yes, that's a trade. It's a good thing to get into." Then he said, "You'd be expected to wear a suit," and I thought that's weird, like it's pretty like posh plumbing. At the end of it, he said, "You've got the job, I'll take you, I'll show you where you work." He brought me up into the drawing office. I had no idea what I'd been interviewed for. I got the job, I started and ended up on-site for six months, strangling pipes and generally being a dog's body to all the tradesmen on-site. Then I was in the office for five years doing an apprenticeship.
David: Now we need a picture of you as a 16-year-old with your earrings.
Remi: I could furnish you with one, but I won't. [laughter] After that, the recession hit, and everyone was being made redundant, so I decided to hide it out at university. I did the traditional way and the academic and came out, and the rest is history.
David: With the knowledge of the tools to help you through the process.
Remi: Exactly.
David: I've got to ask, is the chef skills in the DNA? Are you a cook yourself?
Remi: Oh, yes. I do all the cooking at home.
David: It must have been touch and go there. Was your father not disappointed?
Remi: No, I don't think so. I really enjoy cooking, and ultimately, if I hadn't got that job, I would have been a chef.
David: Well, there we go.
Remi: That's right, yes. One of life's junctions.
David: We talked a bit there about the development of skills and how you develop your skills by doing a bit of on the kit and then at university. As a company, Gratte's has always had a great reputation for training both engineers and apprentices. What do you think has gone wrong with the way we recruit and do our training nowadays?
Remi: Competitive tendering.
David: Competitive tendering.
Remi: The drive to reduce costs. The first thing that gets slashed is training budgets. I did my day release when I was at Benham's at Vauxhall College. I believe that's gone now. There's literally only three colleges in London that you can send people to. I think the industry didn't help itself by focusing entirely on the academic. You can't become a chartered engineer. CIBSE will argue, yes, there is a route for the unqualified, as it were, without a degree, but it's so difficult to navigate that route. Basically, if you want a career in this industry now, you have to have, well, it was an engineering degree, now it's a master's degree.
Therefore, all of the training has come via the academic route. When they come out of university, these graduates, they're more focused to design because that's what the courses are for. I guess, in my generation, all of the trainees came from 16-year-olds joining contractors, doing their time in contracting. Then when they qualified, then they would move into consultancy and bring that practical knowledge to the design side of things. It switched. Basically, all the graduates now go into consultancy, and they don't come back to contracting because why would they?
David: What are you doing at Gratte's to try and overcome that?
Remi: About three years ago, when I first became deputy MD, I introduced, we call it a graduate trainee programme. Basically, what we've done is we've created a full training scheme, which runs all the way from Day 1 over four years. The whole idea is that they work in every section of the business. We've got different entry points. Up until now, what we do is we take our blue-collar apprentices, so the ones that are doing the electricians and the pipework and the plumbing, and our labour manager will basically speak to them when they're in their fourth year, and say, "Are you interested in coming out of the tools and going into the office?"
If we feel that they're made of the right stuff, then we'll bring them in at that point and start them on the four or five-year training programme to bring them through. Again, it means sending them to college, HNC route, rather than a degree route. If they want to after that, then we would be interested in that as well. From my point of view, I think that them coming in at that point with that five years of site knowledge is so valuable to an engineer manager because you can't teach that in a classroom, can't teach somebody how a building site works, how a piece of duct is actually hung up in the air.
David: It gives them those buildability skills that they wouldn't have if they only did the design side.
Remi: Management of labour and all sorts of stuff that academia misses.
David: That's really interesting on the skills side. We talked briefly about off-site before. I know you've got the two facilities at Chelmsford and Worthing. Out of that, what do you think needs to improve to encourage more of that? You see, you hear a lot of off-site specialists, they go bust because it's, they've either got too much work or too little work.
Remi: The reason why I try to avoid the word prefabrication is because that sounds like you're making a product. In order to get your productivity, you want to make a standardized product. If you take someone who makes bathroom pods, then you buy a bathroom pod, and you then have to change the design of the building to fit the pod into it. You can't do that in UK building. Every building is bespoke. It always amazes me, like, you have an architectural consultancy team client, they build a building, they go through all the problems of coordination, getting it right.
Then they build the next building, and they throw everything that they've done away and start from scratch. It's madness. There's nothing standardized in UK building. Every core is different. Every riser is different. Every bathroom is different. What we look to do is to take the unique riser and build that offsite rather than saying we're going to build a range of electrical risers and you pick something that suits your building because it just wouldn't work.
David: You're effectively doing offsite for yourself in that it's all your teams doing it.
Remi: Yes.
David: That has advantages.
Remi: Definitely. Going back to what we were talking about, decoupling it from the programme, improvement of productivity in terms of time, the quality. The original concept was that the electricians would come to Chelmsford, build what they were going to build, and then they would take it back to site and install it themselves. That way you've got none of the finger-pointing. It hasn't quite worked out like that because of logistic reasons. We've got people that live and work near Chelmsford, and it makes sense for them to stay at Chelmsford. One of the things I'm very conscious of is to stop that finger-pointing, the site going, "Oh, Chelmsford mucked it up," and Chelmsford going, "They didn't give me the right information."
David: Moving on to the other big changes in the industry that are coming up and the Building Safety Act is probably the major piece of legislation, and as I was reminded recently, and all the other regulation change that's coming with it, that's a huge change for everyone. Do you see that as a threat or an opportunity?
Remi: I think the industry should hang its head in shame that we've had to have this legislation hoisted upon us because basically, what it's meant is we've been caught doing it so badly that the politicians have had to step in, and actually tell us how to build things, which is terrible. We shouldn't be in that situation. It's obviously going to have a massive change. You've now got to prove your entire supply chain is competent. That sounds stupid, doesn't it? If you're buying something, a piece of kit, then you would expect the people building that bit of kit to be competent to build that bit of kit.
You should be competent that the installer, the subcontractor is competent to install it. We're in a terrible state where you can't, hand on heart, say that that bit of kit has been competently built and that the installer isn't competent to install it, or the architect isn't competent to know that it shouldn't go in that position. It's awful.
David: Are you starting to see the impact of the Building Safety Act, though, in the requirements for Gratte's on projects? Is that starting to bleed through?
Remi: We're principal contractor on a lot of our jobs now, like, 90% of our work, we're principal contractor. I think you'll see it more when you're tendering, in terms of all of the competency statements and [unintelligible 00:20:15] to prove that your supply chain and your staff are competent. You'll see, it'll be interesting, a lot of the changes are to do with building regulations and planning.
I'm not sure how the clients are going to react to it because, in theory, you should have all of the design sorted before you go to planning permission. That means that D&B doesn't work. I can't see the industry wanting to let go of D&B, so I'm not sure how they're going to square that circle.
David: Yes, I would agree on that. Most of the time, though, it's build and design rather than design and build, isn't it?
Remi: Yes. I think you've got that element to it. Then you've got the changes to Building Control because, obviously, Building Control were quite friendly previously, in that they would take a fee to help the design team, and the architect would trundle off to Building Control, show him his designs, and Building Control would go, "I don't think that's right, I don't think that's right, and I don't think that's right. You need to do this, you need to do that." Then they'd go away and rework the scheme, come back and show him again, and so forth.
You'd have this iterative process. Now Building Control aren't offering that service because they haven't got enough staff to do now what they need to do. They've said, "We're not going to do that. As professionals, you should know what you need to do to achieve Building Control sign-off. We're not going to help you." I think that'll be interesting as well.
David: You mentioned that majority of your work is now as principal contractor, presumably working directly for clients. I think you described why that's a really good-- Closer to the money as well, I guess.
Remi: Oh, yes. All day.
David: Does that bring other pressures and risks that you don't get as a Tier 2 or Tier 3?
Remi: I think you need to find the staff that can understand the principal contracting role. That was a bit of a lesson for us in that you've got some very good M&E project managers, but that doesn't necessarily mean that they can build staircases and decoration, and stuff like that. Over the last four or five years, we've had to bring in a lot of what I would call CSA, so, construction, structural and architectural engineering. We've taken on a director now responsible for the CSA element, and that team that we're building. That was a step change for us, and actually taking ownership of that.
In terms of risk, as long as you're managing the process and you're not making any mistakes in that side of things, the risk is the same. If I'm main contractor and you're working as a subcontractor, if that job goes off the rails, then you're all in the lifeboats together. It's no different.
David: Yes, and design liability and responsibility gets pushed down the supply chain regardless.
Remi: Exactly, yes.
David: I get that completely. One final question I had. This is the equivalent. I'm going to take the pin out the hand grenade now, and I guess we've only got three hours left or whatever. BIM, one of your favourite topics, do you think that's been a good thing or a bad thing for the industry as a whole?
Remi: I think the concept is brilliant. The idea to digitally build something before you actually take it to site is a brilliant idea, but it doesn't work. Where I think when it was first trumpeted by government that you needed to do this and it would save 30% on projects, absolute rubbish. It costs an absolute fortune. That's because people don't put the real level of detail that they need to. As M&E contractors, because we've been drawing in 3D for a lot longer than all the other trades, and we have much more mature libraries, so you can actually get a fan coil unit and put it in the model, and you can take individual pipes to it, and everything else, but the builders don't have that same information.
They literally rely on the architects and the structural design models. That's given to the M&E contractor, and you spend an absolute fortune coordinating to it. Then they go out and procure the steelwork. That steelwork contractor comes up with a completely different idea of how he's going to put the building up. The steelwork model changes and then there's clashes everywhere and everyone looks at you and go, "You're rubbish." You go, "Well, you just changed the goalposts." You then have to re-coordinate it again. Then all of the secondary trades start coming in and windposts suddenly start appearing where there were no windposts in the structural model.
Then there's door lintels, and there's all these things that aren't in the architectural and structural models. When they do appear on-site, they clash, and so you don't solve anything. Until the rest of the industry catches up with the M&E and they really do model what they're going to install, then you'll see the benefit.
David: I think what you were describing there is what we were talking about earlier, which is build and design rather than design and build. Whilst you're starting on-site before you finish the design, BIM, how can it possibly work?
Remi: It can't. You have to have that time upfront. If you're going to build a building digitally, then you have to be given the time to build that building digitally. Also, you've got to look at the people that are doing it. The guys, the BIM operators, whilst they're super clever, IT-wise and being able to use the programme, they don't actually know how to install M&E because, otherwise, they would be engineers. Therefore, it's very difficult for them to actually get that. We try and get round that by bringing our site managers into the office to sit with our CAD operators to let the CAD operators have a go.
Then the engineers and site managers will come in and look at the model. We do model reviews and they go, "You can't do that, you can't do that, and that doesn't exist in reality." We'd have a go, but like I say when you get to site and all of these things come out of the woodwork, which aren't shown in anybody else's model, and there's clashes everywhere, you're still doing exactly what BIM set out to do, which is not have that redesign, re-coordination on-site, but it still happens.
David: I think we've discussed this before about how you have so much design time is spent on designing a building that the client can't afford or won't pay up for. It comes back to you as the contractor to make it for the buildability bit. All the stuff you've been talking about, about having people with the skills to know how to build it, the site savvy, as well as the design, is the thing that you bring to the party to make it happen, but your programme is compressed all the way through. That's another reason to take it off-site so that you take out that risk. It sounds like a strategy, really.
Remi: I think you still need that. If you want to take something like a riser and fully prefabricate that or pre-assemble it off-site, then you actually need the time in that coordination process to be able to model it completely. That needs to be built into the programme. That's where the PCSA arrangements really come into their own, where you sign up on a fee to work with the design team prior to the actual pricing of the projects. That can give you real advantages. On a traditional way, you'll literally price it, appoint it, and you're meant to be on-site in a couple of weeks time, then clearly, you can't do everything you'd like to do, pre-assemble, pre-fabricated.
There are still elements you can look at it and go, "Right, we'll do that in Chelmsford, we'll do that in Chelmsford, or we'll do that in Chelmsford," because you're literally taking a room and you're going, "That's how I would install that. Let's go and do that on a still frame in Chelmsford, and then we'll bring it to site."
David: Great. Final question. After 20 years at Gratte's, years in the building, are you now an optimist or a pessimist about the future?
Remi: I think an optimist. I think from our point of view, we've moved into the principal contracting world. We're taking on projects that we would never have taken on 10, 15 years ago in terms of build content. We've learned our lessons along the way. We seem to have quite happy clients behind us. That's reiterated with the repeat business that we keep getting asked to price and deliver. No, as I said I'm quite optimistic for GBL anyway.
David: That's great to hear. Remi Suzan, MD of Gratte Brothers, thank you very much.
Remi: Okay. Thank you. Pleasure.
[music]
David: Now for industry news, a big week, of course, with the announcement of the general election in early July. We'll be looking to talk to both parties about their growth plans, which are so important. Net Zero, which seems to have gone off the agenda for both parties at the moment. Skills and training are obviously a big area of focus for us. Finally, around payments and onerous contract clauses, and the old favourite, retentions. We are optimistic that both parties are beginning to get a better understanding of how damaging retentions are for our sector. In other news, we understand that industry accreditation or grandfather rights changes is really the number one issue on the doorstep, as politicians would say, particularly, those who have relied on grandfather rights for the validity of their skill cards. It's important to us that you have the support and resources necessary to navigate this transition effectively.
To assist you, BESA Academy's skills advisory service is available to address any enquiries you may have regarding accessing the requisite training, but there's little doubt that the deadline set by the CLC at the end of this year will not move, and therefore, it's only adaption that we could hope for. In other news, our annual conference is back on the 17th of October at the brewery in London, and it's the premier event for industry professionals. We've got visionary speakers, leading industry exhibitors, and aspiring leaders. It's a perfect place to connect with a trusted community and help shape the future of the industry.
Early bird tickets are available till the 2nd of July, so book now for your place. Also, on the same day, 17th of October, at the brewery, the BESA Industry Awards, which recognises excellence in building engineering services, you should get your entry in now. They're coming in thick and fast, get yours in before the deadline of the 12th of July. If you haven't already downloaded the Top 30 M&E Contractors Report, you can do so. It features the latest industry trends, insights, and key players, such as Gratte Brothers Limited, which we heard from earlier.
If you're watching this, then scan the QR code on your screen now, or visit thebesa.com.top30m&econtractorsreport. We also have a webinar coming up with myself and Gokhan Hassan on the 13th of June, where we'll discuss the report in greater detail. Register for your free place now. We recently launched our BESA NextGen network, which inspires and connects the next generation of building services professionals. If you'd like to join or know someone who wants to provide new innovative ideas and make a difference in our industry, visit thebesa.com/nextgen to find out more. That's the roundup of the news. Join us again for the next in this series of Behind the Built Environment podcast. Thank you, and goodbye.
Episode 1: Behind Building Control
In this episode, David Frise, Chief Executive for BESA, chats with Lorna Stimpson, Chief Executive at LABC, about the Building Safety Act and its impact on the construction industry. Lorna discusses her background in building control and emphasises the importance of cultural change, competence, and putting safety first. They explore the significance of the Building Safety Act, the need for behavioural change and the responsibilities of duty holders in ensuring compliance.
David: Hello, I'm David Frise, Chief Executive of BESA, and welcome to our new podcast, Behind the Built Environment. The podcast where we will delve into the industry's latest news in the building engineering services sector. With leading industry experts, we'll explore the trends and innovation shaping the future of the built environment and the impact they will have on you and your business. Today, I'm delighted to welcome our first-ever guest, Lorna Stimpson, Chief Executive at LABC.
Lorna: Thank you.
David: Lorna's career in public service building control spans over 30 years in roles from building control surveyor up to senior managerial positions. Lorna joined LABC in 2008 as Business Development Director, advancing to Deputy Managing Director in 2015, and Chief Executive in 2019. Lorna has a proven track record in delivering complex projects and strategic reform. She works with DLUHC, HSE, the National Fire Chiefs Council, and Local Government Association as a member of the Joint Regulators Group, defining, piloting, and testing the new regulatory approaches.
She sits on the Industry Competence Committee and the Fire Protection Board. Lorna is a Board Director of LABC, the Construction Industry Council, and the Building Safety Competence Foundation. It's a wonder you've got time to come and see us today, to be honest, with all of that on a busy life.
Lorna: It's a busy time. Busy time for the construction industry generally. Yes, and I think we're all feeling the same at the moment.
David: How did you come into the industry? What was your entry point into this?
Lorna: I became a trainee building control surveyor at 16 and I've never looked back. It's the best career choice. We've just been taking on trainee building control surveyors, and I can honestly say to them that I wouldn't change a thing about my career. The 30 years in building control surveying, probably not quite 30 years, but in building control surveying was just fantastic. Fantastic. I would do it all again.
David: That's good. If you get so senior in your career and you do it all again, then you must have made the right choice.
Lorna: Yes.
David: We'd like to start off all these podcasts with a quick-fire question. Yes or no, if possible to this.
Lorna: Okay, I'll try.
David: Building Safety Act is clearly the dominant thing for you over the recent the last few years. Quite a few of these will be around Building Safety Act. Is the Building Safety Act the most important change in construction in your career?
Lorna: Absolutely. That wasn't yes, was it? I'm sorry. Yes.
David: Even more affirmatively, yes. Does it cover all buildings?
Lorna: Yes.
David: Is everyone in construction impacted?
Lorna: Yes.
David: Will the Building Safety Act result in behavioural change in the industry?
Lorna: It should. Yes.
David: Will the industry be better because of it in five years?
Lorna: Yes.
David: Do good companies, those who are competent and compliant, have anything to fear from the change?
Lorna: No.
David: Great. Thank you. All yes and nos. That was good. An absolutely. That's a huge boost. Could you just start off by just describing what you understand the Building Safety Act is about and why it's so important for the industry?
Lorna: That's a difficult question. Why is it so important and what is it about? It's about putting right the wrongs that we've had for so many years in construction, I think. It is fundamentally about cultural change. I know that is seen as quite a fluffy thing. It's not. It's not something that you can pin down, but it is about people doing the right thing for the right reasons, and consciously doing that. It's about competence. It's about culture. It's about putting safety before profit and a legislative process and framework by which that is the driving force. I truly believe that the Building Safety Act, if implemented appropriately, will do all of those things.
David: To make the building process safer, more certain, would you say, over that period of time?
Lorna: Yes.
David: To drive, we talked earlier, or you answered yes, to behavioural change. It's not just process. It's not a tickbox exercise. It requires people to change the way they operate and view the operations.
Lorna: Without a doubt. I'm obviously heavily involved in building control, and we are at the sharp end of that. Building control is becoming a regulated profession or has become a regulated profession. We're leading that change. I think the work that I do on the Industry Competence Committee as well is about driving cultural change across the whole industry. That's about attitudes. That's about people understanding what the legislation is trying to achieve, and the fact that that legislation is trying to drive safer buildings.
David: I guess with all change of that nature, you get we always divide them into threes. You get 33% immediately get it and change. 33% wait for something to happen and then change. You get 33% who never change. Where do you see us on that spectrum at the moment? I see quite a lot of the top third really going for it. Are we really getting into that second segment yet?
Lorna: In building control, we certainly are because we've had a deadline and we've had to work to it. In terms of construction, I think it will take a long time and a long time to filter down. The driver for this change was Grenfell, the Grenfell tragedy. That was what? Seven years ago now. Dare I say it, the impact fades from people's memories. If it's not something that's in your mind all of the time. It is obviously in ours because I'm working closely with the building safety regulator and DLUHC as part of this programme. We live and breathe it every day. Other people can be forgiven for not having been touched by the implementation yet.
I think the whole idea is that, gradually, over the years, this new way of working, the cultural change that we've talked about, the behaviours will start to trickle down throughout the industry. Construction is an unusual industry, and I think it will take some time. It's also a massive spanned industry, isn't it? I think we were talking earlier and you said something about from the shard to the shed. That is construction, isn't it? That is the massive breadth of construction. How long is it going to take for these new behaviours to come down to those people working on the shed?
It's going to take a long number of years, but it will happen. I'm very sure it will happen, whether it will be in my lifetime or career. I don't know, but it will happen. Or [crosstalk] determined.
David: I guess my career will end roughly the same time as yours. I would really like to have seen something happen by then. I was at an event last night at the Tower of London from the mechanical contractors, Vonterio. They held their conference in London, and their president said that they counted the number of cranes in London alone. It was over 100. They were staggered by the amount of work going on. Are you concerned about the resources available to planning and building control departments to actually deliver that, so they're not delaying the whole process?
Lorna: I don't think there will be any further delay than there ever would have been. capacity and local authority building control. Will we ever have enough people? I don't know how many is enough. I don't know, but certainly not impacting on delays to construction. The registration of building control professionals has now gone through that process, and we continue to work towards full implementation. What we're also doing within LABC, with massive support from English and Welsh governments, is to bring new recruits into building control. We know that we were an ageing profession. We know that there was a lot of people in the latter end of their career at this moment in time in building control.
We've been very, very conscious to bring in as many new starters and trainees into building control as we possibly can. We've done that over the last 12 months. We've taken on about 130 building control surveyors, and we continue to do that with government funding. Whilst we're losing people at the top end of their careers to retirement, as we would naturally, we're bringing people in at the bottom end to replace them, and to backfill those more experienced people that we're losing. It's all about the training. It's all about competence and building that professional network again, which is something that's very much part of our strategic direction.
David: The press will always focus on negative stories because that's what people want to read, by and large, you don't need to hear the good news stories. How useful is the three-month delay announced by government to building control officers complete that registration process. I'm assuming you agree with that decision to delay?
Lorna: I wrote to the building safety regulator and Welsh Government to request not a delay but an extension and that's what we've been given an extension to the deadline. Just to allow people to go through the process. I think what perhaps industry don't generally understand is it isn't just a registration process. Building control surveyors have got to prove their competence as part of that registration so through an independent company organisation. LABC's organisation that we set up some time ago the Building Safety Competence Foundation is gaining UCAS accreditation in 17-024 to be able to assess the competence of building control surveyors.
The surveyors have got to go through that really rigorous process to get their proof of competence before they're able to register. It's not a simple registration process and that three-month extension to the deadline that the BSR Welsh Government gave six months extension to the deadline. Very much welcomed by the industry and by LABC because it has given us that opportunity to get more professionals through this process. The building control professionals, they're willing they are ready and able, and going through that programme as we speak.
I think come July and in October for Wales, we will have the vast majority of current building control professionals registered in the system and practicing as registered building inspectors.
David: We represent mainly tier two contractors although they typically can now do more than half the work on a project but tier twos and below. They're very time-strapped there's I think still a lot of confusion in the industry about what's covered and how it's going to impact them. As a tier two contractor, what do you think they need to know and what should they prioritise in the way they operate in the future?
Lorna: I think it's fair to say that many people who aren't involved necessarily directly in HRBs so higher-risk buildings think that maybe the Building Safety Act doesn't impact on them. It does and the legislation has changed, and anybody who has an impact on a building whether it be a subcontractor the main contractor, they're what is now called duty holders. They have a duty to do their work in a certain way, and most of that is about competence and knowing their abilities. Whilst that might not necessarily have filtered down to your members yet, they are duty holders. That duty holder role doesn't just apply to HRBs the tall residential buildings it applies to every piece of construction.
Whether it be a kitchen extension or the shards, there are duty holders, and that duty holder isn't just the main contractor or the principal designer. The principal contractor principal designer it's everybody who has an impact on that building, or on that design. They are dutyholders, and they have responsibilities. Part of that responsibility is to understand their competence. Now, maybe at this moment in time, there isn't a requirement for them to prove that competence or be on a register. They are expected to understand their competence and their sphere of competence. The grey areas around what they are competent to work on what they have.
Competence, let's forget is about skills, knowledge, experience, and behaviours, and so it's not just about what you learnt in a book. Have you worked on that type of building before? Are there things that you don't quite understand, and it's your responsibility as a duty holder to understand where your skills, knowledge, experience, and behaviours lie.
David: Interestingly today, we've got a meeting in Rotherwick House which is where our offices are to discuss competence and the apprenticeship for ductwork. We've got 40 ductwork contractors coming in to do that. I guess the point I'm getting across here many of those competencies haven't really been fully defined yet. How long do you think the industry has to get that in place so that there's something to define competence against so someone who has a duty of care can understand what competence looks like?
Lorna: I think that many professional bodies, many organisations are already going down that route that you're starting to go down now. I think it's absolutely the perfect time for these disciplines, quite unique disciplines to start to understand what good looks like. I think what you're doing is what needs to happen, but that can only be done by the industries themselves. You can't tell building control what good looks like in building control if you're not from a building control profession. It's the same with your members.
It's for them to decide what good looks like and start to as you say develop the newcomers into that industry with that blueprint of what good looks like in a competent person in your industry. That can't be done to you that is for industry to do it themselves and that shows a mature industry.
David: Well, that's what we're trying to develop. We've operated competence assessment standard for 25 years, and it's only now just beginning to come into its own. That's because it's third-party accredited. Crucially also ask the question that many PQ processes done this, is that can you do the job? Which seems bizarre that we've never. We've asked, "Have they got insurance, have they got policies in place?" The question about, "Are you actually competent to do the job?" Never comes into question.
Lorna: No, and that's the difficult question, isn't it? That's where culture comes in, that's where behaviors and ethics comes in. Have you done this before? If you haven't can you find out how to do it? Are you competent to work on that scheme, so absolutely, your question is perfect. Can you do the job, not just do you want to do the job?
David: Is the price right?
Lorna: Is the price right, yes.
David: Many people have suggested that it's the end of value engineering as it currently exists, which is a euphemism for I need the price cut. Do you see that ending with the Building Safety Act really beginning to bite?
Lorna: I think it depends the extent that you're going to go with value engineering. If you're impacting on safety, then yes, it's the end of value engineering, but that should have never have been a thing. Value engineering shouldn't be to reduce something from compliance to non-compliance by using substandard materials or substandard labor that should not be a thing. It's about quality, isn't it? Value engineering no, I don't see personally, there's no reason why you can't do things just as safely or compliant or as compliant, but maybe a little bit cheaper, but not when you're compromising safety and standards. Absolutely not.
David: Many people have also questions about when it will really start. I think I use the term when will it really bite, and many people are suggesting that we need some prosecutions, and then people will go. Now we'll take some notice. How long do you think we are away from-- The industry fully understanding the consequences of the Building Safety Act.
Lorna: I think as you say until people start to be prosecuted, people don't sit up and notice. I don't think the HSE who obviously the building safety regulator is formed within the HSE. I think we all know that they don't stand off from prosecuting when they need to. If it needs to happen they will serve their notices.
David: Pre-Grenfell, I guess I'm pre the Building Safety Act. There was always I felt the perception in the industry that if building control didn't spot something or Clarkworks, for example, then we've got away with it. Actually, the building I live in that was the response of the developer that well, building control signed it off. There was always the perception that building control was somehow fully responsible for things and not able to do things properly. How is the industry responded to that?
Lorna: That was absolutely the perception before. It was never a fact. It was always the responsibility of the person carrying out the work to comply with the legislation. Building Control are there to secure compliance, if they see non-compliance, to do something about that. Things haven't changed, but now what has changed across the industry is that there will be an expectation for that principal contractor to say that they have complied with the legislation. That is their application for completion. Entirely changed, turned on its head.
The perception was wrong before, but what the legislation has done is made it clearer that it is the duty holder's responsibility to comply. Just because Building Control didn't happen to pop onto site when they were doing something inappropriate doesn't mean to say that they could continue to do something inappropriate. Again, it comes back to culture and behaviours. Why is that okay? Just one, we've been interviewing recently, and I have said this before, but we were interviewing recently for trainee Building Control surveyor. One of the questions was about integrity. What does integrity mean? Obviously, that question is because for Building Control or anybody in our industry, you've got to have integrity.
One young person, their answer to me was integrity is doing the right thing even when no one's watching. That was absolutely perfect. I think if the whole of the construction industry used that or just kept that in the back of their mind, then we would have a safer construction industry, we would have a safer built environment. Integrity and ethics is the thing for me.
David: Would you advise our members to have evidence, a full bank of evidence of how they have complied with the package of work they've done at the time?
Lorna: This isn't meant to be something that is difficult or hard to do or an imposition. This is just proving that you've done what you should do. In the same way, with Building Control surveyors now having to prove competence and register with the regulator, that's not about doing something different than they've done before. Dame Judith, in her report, was really clear. She wanted proven, measured competence, not just I say, "I'm competent or I passed an exam 30 years ago and therefore," this is not anymore. The construction industry is not, pass an exam once, practice for life.
I think that that's got to be the same for every part of our industry. You've got to keep up to date. We know that construction products alone change so often. It's such a massively innovative, area that how can you stand still? That constantly keeping yourself up-to-date is part of being a built environment professional and so very important.
David: Lorna, just to summarise what we've heard today to make sure that I've fully grasped this. The Building Safety Act is the key legislative change over the last few years. It affects the whole industry. I think we said the shard to a shed, everything and everybody. It requires cultural change, ethical behaviours on a scale that we haven't seen before and people need to do the right thing. I think we say even when people aren't watching you, it's for the industry to decide competence, what competence is, and indeed, I guess, what compliance is from that.
That tier two contractors or our members should always evidence their compliance, have a record of it for the future. It's your responsibility to provide that evidence. Nobody else is going to do it for you. Certainly, not building control.
Lorna: No.
David: I think we've reached the end of our time. I've got one final question and that is really, do you leave or are you currently optimistic or pessimistic about the future of the industry?
Lorna: Optimistic, but that's because it's Thursday. If it was Monday, maybe not. No, I'm definitely optimistic because I can only see good things. It's been difficult. There have been some hard decisions. There will be hard times coming for the whole industry. We've got to be better as an industry. We've got to be better. I think that we will be.
David: Lorna Stimson, Chief Executive at LABC. Thank you very much for joining us this morning.
Lorna: Thank you
David: Now to industry news. This is the week that T. Clark were acquired by Regent Acquisitions for £90.56 million, taking them from a public company back into private ownership. Interesting comparison with the failure of MJ Lonsdale recently. There's still plenty of flux in the market and some consolidation, no doubt, to come. Having just interviewed Lorna Stimpson from LABC, it's interesting to note as well that the Grenfell inquiry has been further delayed, and we will see when that finally gets published, and the impact that has.
In BESA news, BESA are very proud to be the competition partner for refrigeration and air conditioning, along with Mitsubishi and Refcom. The national finals will be held in November, with the WorldSkills finals being held in Shanghai, China. BESA have also launched TR19 Air, along with complementary courses from our approved suppliers. That is an opportunity to evidence your competence and compliance, as we discussed earlier in the podcast. In Scotland, new build heat standards have been introduced, which came into force on the 1st of April.
Finally, I had a letter published in the Financial Times, which you've no doubt all read, about boiler pricing strategies and the consequences of government consistently changing policy at the last minute. A quick reminder that we operate, as BESA, the competence assessment standard, a three-part standard business management review, a technical audit, and organisational capability. Which is UCAS accredited, which is your opportunity to evidence to those duty care holders your competence and compliance. Crucially, we ask the question that many PQ processes don't, is can you do the job? On that note, thank you and goodbye.