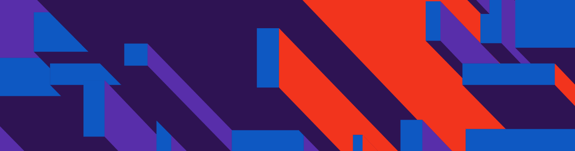
Health & Safety in the construction industry - Supported by BESA
BESA's Health and Safety Service provides reliable, responsive, and practical support on safety standards and compliance for the construction industry. As a free service for members, it not only saves you hundreds of pounds annually but also removes the stress of dealing with health and safety issues, providing peace of mind.
Ensuring Health and Safety in the Construction Industry
Health and safety are critical priorities for construction companies and contractors operating in the United Kingdom. The construction industry inherently involves numerous hazards and risks that must be carefully managed to protect workers, comply with regulations, and maintain operational efficiency.
For heating and ventilation contractors, prioritising health and safety practices is essential. These professionals work in high-risk environments, often dealing with hazardous materials, heavy equipment, and confined spaces. Failing to adhere to stringent health and safety protocols can lead to catastrophic consequences, including falls from heights, exposure to asbestos or other dangerous substances, electrocution, and injuries from power tools or machinery. Mental health is often overlooked in the construction industry, despite the high-stress nature of the work. Construction workers face unique challenges like demanding schedules, physical labour, and potentially hazardous conditions that can take a toll on their mental well-being.
Implementing robust health and safety measures is crucial for heating and ventilation contractors to mitigate risks within the construction industry. By prioritising worker safety, companies can minimise accidents, reduce downtime, and avoid costly fines or legal repercussions for non-compliance with health and safety regulations. Furthermore, maintaining a strong commitment to health and safety practices enhances a company's reputation for professionalism and reliability within the competitive construction sector.
BESA can support you with access to unlimited health and safety advice when you need it most, simply join BESA Membership to access free guidance and resources.
How we help you with Health and Safety in the Construction Industry
The in-house team of health and safety experts at BESA offers advice and support via the BESA Members' Resource Area, where you can download free templates and guidance documents, including:
Risk Assessments
We have a range of free risk assessment templates depending on your needs, such as mechanical hand and power tools, general plumbing, hot work, and working on flat roofs. Each document provides a comprehensive framework for identifying, evaluating, and mitigating potential risks in the workplace, ultimately enhancing worker safety and compliance with construction health and safety regulations. We can also provide custom risk assessment templates based on your individual needs.
Health and Safety in the Construction Industry Policies and Procedures
We have a range of free health and safety policies and procedures for members to utilise, including accident investigation templates, asbestos policy statements and procedures, health and safety policy statements, and lone working policy statements and procedures. Comprehensive policies and procedures are essential in the construction industry to ensure worker safety, regulatory compliance, quality control, effective risk management, and consistent training and accountability across projects. These guidelines promote a safe and efficient working environment while minimising risks, errors, and legal liabilities.
Health and Safety Bulletins
The BESA Health and Safety Bulletins are regular publications that provide BESA members with critical updates on regulations, safety alerts, hazard awareness, best practices, training requirements, legal developments, and industry collaborations related to health and safety in the construction industry and building services sectors. These bulletins aim to educate members, promote compliance, and share practical guidance to proactively address risks and maintain a safe working environment. By staying informed through these bulletins, you can implement effective health and safety measures across your building activities.
Free one-to-one Health and Safety Consultation for Construction Businesses
BESA members can book a private one-to-one session with BESA's Head of Health and Safety, Rebecca Crosland, to discuss any construction-related health and safety support or guidance needed, such as:
- Health and safety questions impacting your construction business or staff - take advantage of our experience and knowledge. If you can't find the answer in our online FAQs, we will research and provide the information you need on any topic within health and safety for the construction industry.
- Specific health and safety templates for the construction industry - if we don't hold it in our health and safety template library, we can create the templates you need based on your individual needs.
- Assistance with the SSIP (Safety Schemes in Procurement) process for construction sites - we can help you meet the health and safety requirements and certifications necessary to satisfy the SSIP certification for working on construction sites.
- Guidance through the health and safety section of your BESA Competence Assessment Standard (CAS) audit - we ensure you have the key documentation and health and safety processes you need to pass the audit, retain your BESA membership and demonstrate your competence and compliance every three years.
Collaborative Partnerships for Construction Health & Safety
We work closely with the HSE (Health & Safety Executive) and industry safety bodies, ensuring our construction members benefit from their range of technical contacts, local knowledge, and shared expertise. Our partners include:
- IOSH (Institution of Occupational Safety and Health)
- BSC (British Safety Council)
- BOHS (British Occupational Hygiene Society)
- SHEP (Safety Health Engineering Partnership)
- IIRSM (International Institute of Risk and Safety Management)
- FPA (Fire Protection Association)
- CCS (Considerate Constructors Scheme)
- CICV (Construction Industry Collective Voice)
Exclusive Health and Safety Discounts for Construction Businesses
BESA members can access exclusive discounts on SSIP Certification, Health and Safety Executive (H&SE) Courses and Tests for obtaining Craft or Operative SKILLcards, and much more.